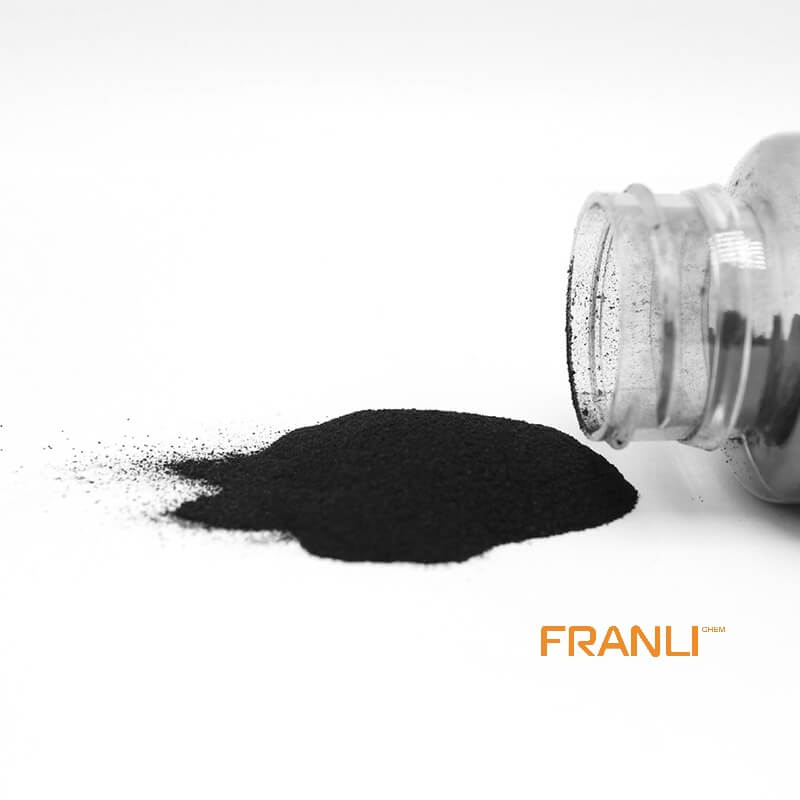
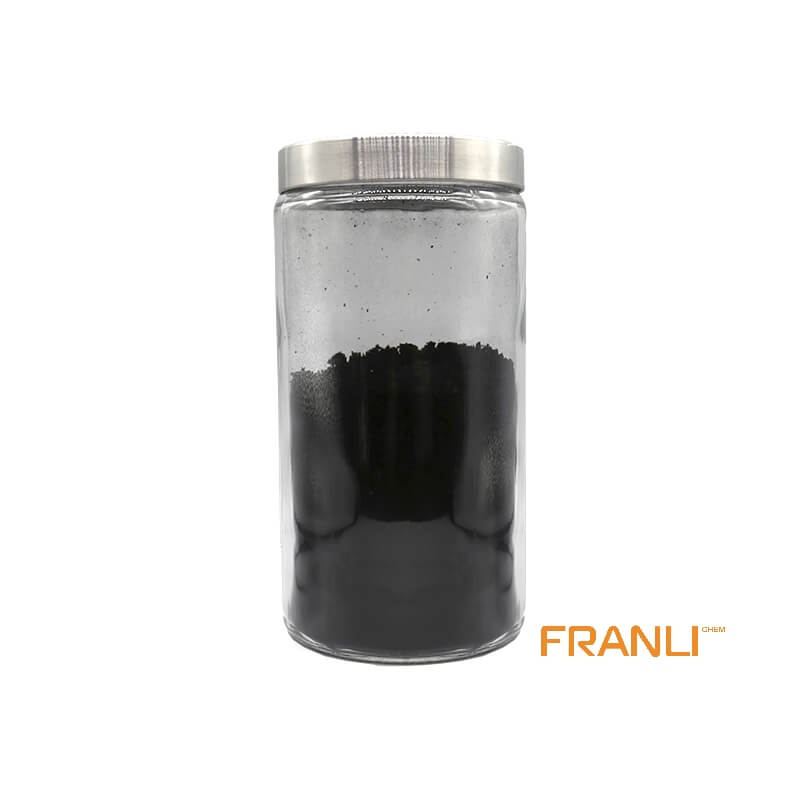
Graphene
Size
1-2nm thick x 0.5-5microns wide
Package
According to customer requirements
Features
High strength, high electrical conductivity, etc.
Application
Can be used as filler(between 0.01% and 5%).
Graphene, as the thinnest, toughest and best conductive nano material found at present. It is a two-dimensional crystal composed of carbon atoms stripped from graphite material with only one layer of atom thickness. Known as “black gold”, it is “the king of new materials”. Scientists even predicted that graphene “will completely change the 21st century”.
Request a quoteGraphene has a wide range of applications, and coatings are an important part of many graphene applications. With various superior properties, graphene has very far-reaching application prospects in terms of electrical conductivity, corrosion resistance, flame retardancy, thermal conductivity and high strength.

Why graphene is suitable for paint industry?
Graphene has the advantages of large specific surface area, good electrical conductivity, strong chemical stability, excellent mechanical properties and thermal conductivity, etc. Once it came out, it has attracted widespread attention from all over the world. Based on the excellent properties of graphene, graphene has become the focus of a new generation of coatings. Functionalized graphene with a large number of oxygen-containing groups has a strong binding force with resins and polymer materials, and is extremely suitable as a reinforcing material or functionalized material. Graphene coatings have excellent performance in anti-corrosion, electrical conductivity, anti-static and other fields.
The applications of graphene
(1)Graphene in conductive coatings: The surface resistance of the electrostatic conductive coating is usually between 106 and 109, which can effectively prevent the phenomenon of static conduction, so it is generally used in occasions with high requirements for fire protection and explosion protection. For example, the inner and outer walls of oil storage tanks, oil pipelines, oil tankers and other oil storage and oil transportation equipment in petroleum, chemical, railway, transportation and other industries, and anti-corrosion coatings for equipment in coal mines, aviation, textiles, food and other industries generally use electrostatic conductive coatings as Anti-corrosion coatings, which can not only prevent equipment corrosion to the greatest extent, but also avoid problems such as fire accidents caused by static electricity caused by charge accumulation. Graphene has both good electrical conductivity and corrosion resistance, so it works well in conductive coatings.
(2) Graphene in high thermal conductivity and heat dissipation coatings: Graphene has a high thermal conductivity. Adding graphene to the coating can significantly improve the thermal conductivity of the coating. Therefore, graphene modification has become an important development direction of heat dissipation coatings. In addition, graphene has a large specific surface area, and the paint film contains a certain amount of graphene, which can greatly increase the heat dissipation area of the paint film, help the heat dissipation on the surface and inside of the paint film, and make the internal and external temperatures tend to be consistent. Because graphene coatings have good mechanical properties, corrosion resistance and aging resistance, graphene coatings are usually used as heat dissipation coatings for components in many harsh conditions.

(3) Graphene in anti-corrosion coatings: Environmentally friendly paint is the main direction of paint development today. Due to its low VOC, water-based coatings have become an important development target for environmentally friendly coatings. Water-based paints use water as a dispersant, which has a high surface tension, and the film-forming property of the paint film has not been ideal. Adding graphene to water-based anti-corrosion coatings can effectively improve this.
The two-dimensional structure of graphene monomer is dispersed into the paint film layer by layer to form a dense isolation layer, which can play a role in fire prevention and flame retardancy. If resin is added to the coating, graphene can also be cross-linked with resin molecules to further strengthen the isolation effect and enhance the flame retardant effect. In addition, in addition to carbon dioxide and water, the products of graphene coating combustion will leave a continuous carbon layer in place, thereby improving the flame retardant effect again. For this reason, graphene also has good applications in flame-retardant coatings.
Anti-corrosion coatings have always been one of the important branches of coatings and are widely used in industrial production. In the production of the national economy, the use of a large number of metal products makes the anti-corrosion requirements of equipment very high, and the market demand for anti-corrosion coatings continues to rise. According to statistics, the global economic losses caused by corrosion are as high as trillions of dollars every year, far exceeding the economic losses caused by natural disasters. Franli’s company found that Adding graphene to the existing epoxy anti-corrosion coatings improves the impact resistance, adhesion, water resistance, hardness and other indicators of the anti-corrosion coatings in addition to the original performance. It is widely used in the anticorrosion of equipment in the fields of marine engineering, transportation, large industrial equipment and municipal engineering facilities.