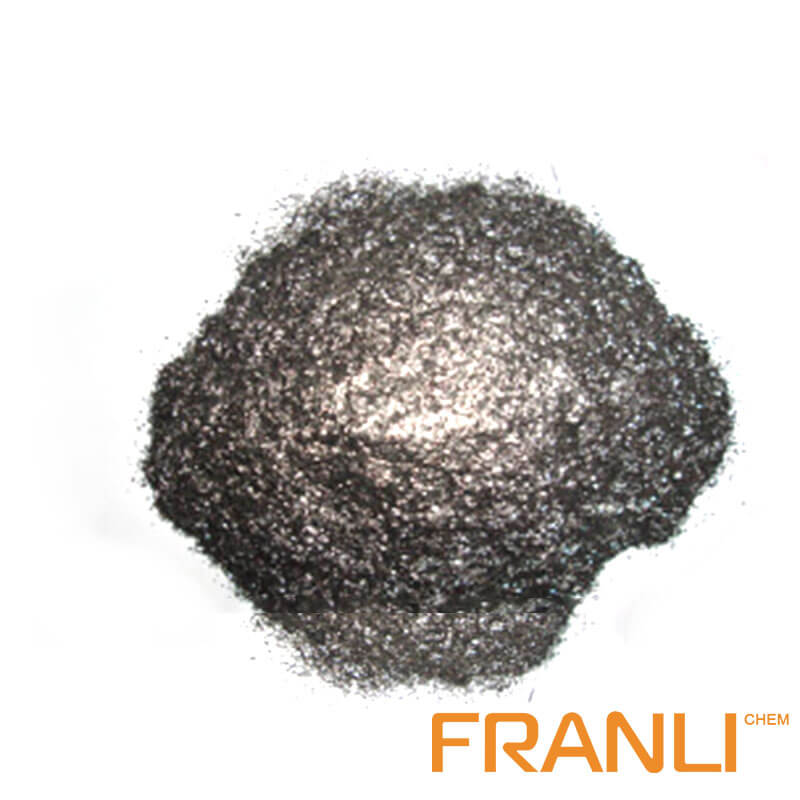
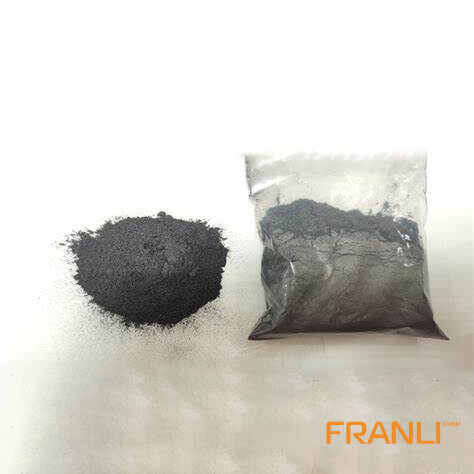
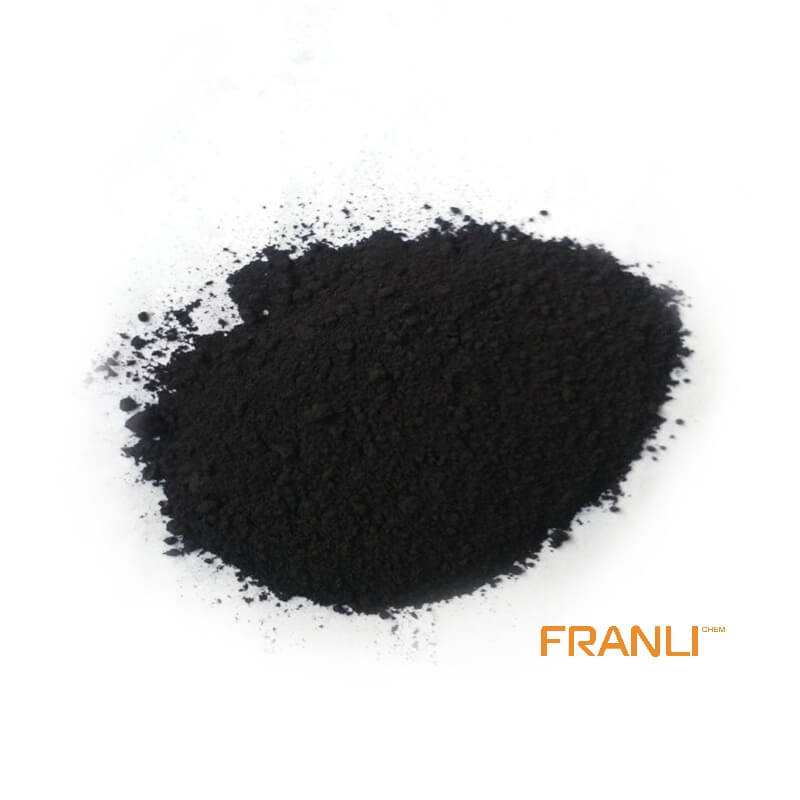
Flake Graphite
Size
0.01mm
Carbon Content
99%min
Package
25kg small bags into ton bags
Origin
China
Features
thermal shock resistance, lubricity, conductivity and plasticity…
Application
Lead battery plates positive and negative conductive agent, lithium batteries nickel hydrogen etc
Natural flake graphite has superior physical and chemical properties and is widely used in metallurgy, coatings and refractory industries. It is an important non-metallic raw material that is indispensable for today’s high-tech. Flake graphite is divided into large flake graphite and fine flake graphite according to the size of its scales. Usually, large flakes refer to +32 mesh, +50 mesh, +80 mesh, and +100 mesh flake graphite.
Request a quoteFlake graphite is widely used in high-grade refractory materials and coatings in the metallurgical industry. The surface tension of flake graphite is small, there is no defect in a large area, and there are about 0.45% volatile organic compounds on the surface, which deteriorates the wettability of graphite, the strong hydrophobicity of the surface of flake graphite, and deteriorates the fluidity of the castable. In addition, graphite is easy to aggregate and cannot be uniformly dispersed in the refractory material, so it is difficult to prepare a uniform and dense unshaped refractory material.

The microstructure and properties after high-temperature sintering depend to a large extent on the wettability of high-temperature silicate liquid to graphite. When wetted, the silicate liquid phase flows into the particle gap under the action of capillary force. The graphite particles are bonded together by the adhesion between them, forming a thin film around the flake graphite, which forms a continuum after cooling and forms a higher bonding interface with the graphite.
If the two do not wet, the flake graphite particles form aggregates. The silicate liquid phase is confined in the particle gap to form an isolated body, and it is difficult to sinter to form a dense composite at high temperatures.
Coated sand refers to molding sand or core sand covered with a layer of the solid resin film, and flake graphite for coated sand is used to prevent shelling during the use of coated sand.

The flake graphite for coated sand is used as a lubricant in the coated sand. The flake graphite for the coated sand can play the role of lubrication and high-temperature resistance in the coated sand. The requirements for the flake graphite for the coated sand are As a lubricant, it is required to have good lubricating performance and a high melting point. The flake graphite for coated sand is made of natural flake graphite with good lubricity, and it is processed by a purification process to increase its carbon content. The flake graphite itself has a high melting point. The high-temperature resistance of flake graphite will be higher, and the lubrication effect will be better.
The function of flake graphite for coated sand is to prevent agglomeration and improve the fluidity and mold release of the coated sand. Flake graphite for coated sand can not only improve the lubricity and wear resistance of coated sand but also improve its high-temperature resistance. The coated sand produced by the process can be used to produce various complex castings such as automobile cylinder blocks, cylinder heads, intake manifolds, various pipe fittings, and pump bodies.
Coated sand is made of natural quartz sand as raw sand, thermoplastic phenolic resin, urotropine, flake graphite for coated sand, reinforcing agent, and other raw materials. The function of flake graphite for coated sand is to prevent coating. The sand produces a shelling phenomenon during use.