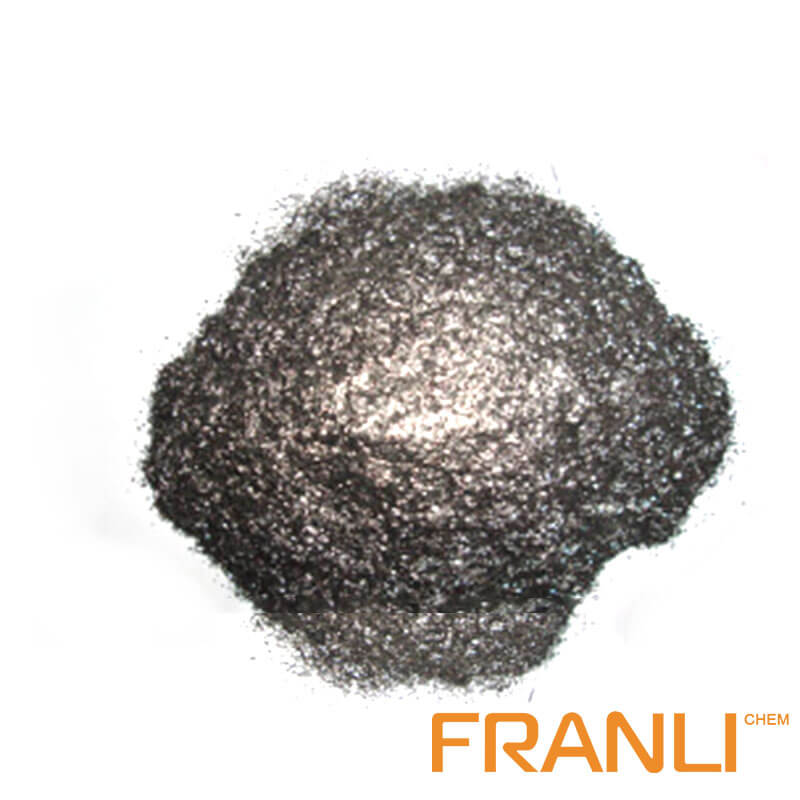
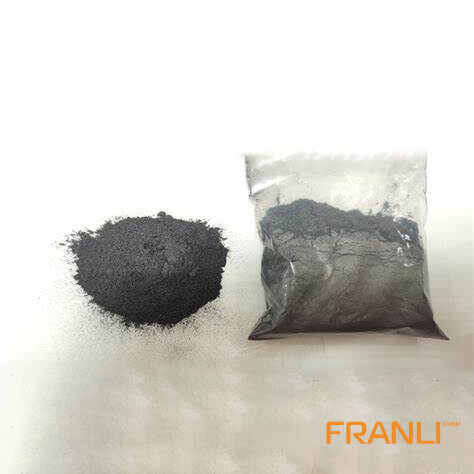
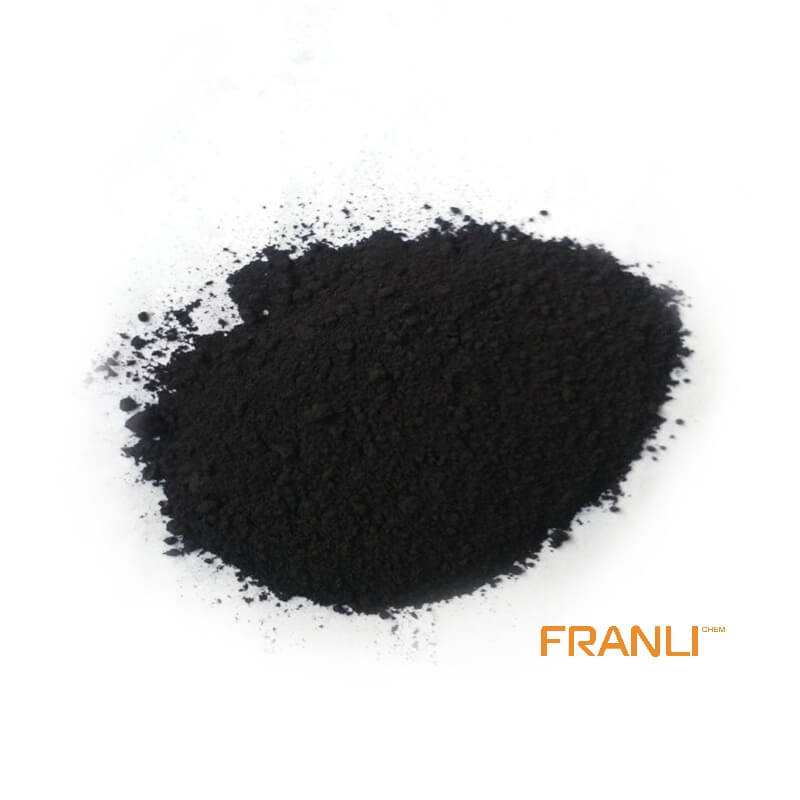
Flake Graphite
Size
0.01mm
Carbon Content
99%min
Package
25kg small bags into ton bags
Origin
China
Features
thermal shock resistance, lubricity, conductivity and plasticity…
Application
Lead battery plates positive and negative conductive agent, lithium batteries nickel hydrogen etc
Natural flake graphite has superior physical and chemical properties and is widely used in metallurgy, coatings and refractory industries. It is an important non-metallic raw material that is indispensable for today’s high-tech. Flake graphite is divided into large flake graphite and fine flake graphite according to the size of its scales. Usually, large flakes refer to +32 mesh, +50 mesh, +80 mesh, and +100 mesh flake graphite.
Request a quoteFlake graphite has strong thermal shock resistance and good corrosion resistance. It is the main carbon raw material used in carbon bonded refractories. It has an important influence on the corrosion resistance and high-temperature strength of carbon bonded refractories such as magnesia carbon brick. In the actual production process, carbon bonded refractories have strict requirements on the purity, ash content, particle size, shape, and an additional amount of flake graphite.
1. Purity of flake graphite
A large number of studies show that the purity of graphite is directly related to the high-temperature flexural strength and melting loss rate of MgO-C brick.
The high-temperature flexural strength of magnesia carbon brick increases with the increase of the purity of graphite. This is due to the different microstructure of magnesia carbon brick. The magnesia carbon brick made of low purity graphite has coarse pores (diameter 20) after carbonization at 1000 ℃ μ m) The porosity is also higher than that of products made of high-purity graphite. This may be related to the high flexibility of high-purity graphite and easy compression during the brick making. Another point is that the structure of magnesia carbon brick made of graphite with low purity is partially weakened. After the magnesia carbon brick is treated at a sufficiently high temperature (such as 1600 ℃), the silicate minerals associated with graphite melt into the glass phase and react with magnesia or carbon, so that the original minerals are eroded, the volume is reduced, the contact area is reduced, and a pore zone is formed around the graphite, As a result, the high-temperature strength of magnesia carbon brick decreases with the decrease of graphite purity.

The melting loss rate of MgO-C brick decreases with the increase of graphite purity, especially for graphite with purity greater than 95%. The research on its mechanism shows that when the temperature is above 1300 ℃, the impurities in magnesia and graphite (SiO2, Cao, Al2O3, Fe2O3, etc.) gather at the junction of them to form low melting matter, which makes magnesia particles easy to be eroded by slag and flow into slag, thus reducing the corrosion resistance. The practical application results show that the slag resistance of magnesia carbon brick made of graphite containing more than 95% carbon is 0.5 ~ 1 times higher than that of ordinary magnesia carbon brick.
Using high carbon flake graphite with a carbon content greater than 95% ~ 96% is an effective technical measure to improve the quality of magnesia carbon brick and reduce the cost of brick making. If the performance of bricks made from the same grade graphite and magnesia raw materials is taken as the benchmark, the performance of bricks will be improved much more by using high-grade graphite than by improving the grade of magnesia. Under the same process conditions, the properties of bricks made of high-grade graphite and low-grade magnesia are better than those made of high-grade magnesia and low-grade graphite. However, it must be noted that when graphite with high purity is used, the amount of liquid phase generated in the brick is small, and oxygen is easy to penetrate into the brick to oxidize and decarbonize the graphite. Therefore, antioxidants such as metal Al, Si, Al-Mg alloy, SiC, BN, etc. must be added.
2. Ash content of flake graphite
Obviously, the greater the ash content of graphite, the lower the purity of graphite. The ash content of graphite is mainly composed of SiO2-Al2O3-Fe2O3 — Cao, etc. Generally speaking, if the content of Al2O3 is high and other impurities are low, the fire resistance of ash is high (about 1500 ~ 1600 ℃); If the content of Al2O3 is low and there are many other impurities, the fire resistance is low (about 1250 ℃).
The high content of SiO2 in ash is very harmful. Firstly, the introduction of a large amount of SiO2 will inevitably change the CaO / SiO2 ratio of high-quality magnesia and change the original high-temperature binding phase C2S or C3S (melting points 2130 ℃ and 1900 ℃) of magnesia into CMS and c3ms2 (melting points 1490 ℃ and 1575 ℃) with a low melting point, so as to significantly reduce the high-temperature performance of brick. Secondly, SiO2 can also reduce the stability of magnesia and carbon and promote the volatilization of MgO. This is because SiO2 will react with MgO during heating to form a thin layer of forsterite (M2S) on the surface of periclase; With the increase of temperature, SiO2 in M2S can easily react with C and volatilize (SiO2 + C → SiO + CO). The surface of periclase after SiO2 volatilization is activated, which promotes the MgO-C redox reaction. At the same time, M2S itself is prone to redox reaction with C at high temperatures. The result is that the heat loss of MgO-C brick is significant and the microstructure is loose.
The content of SiO2 in flake graphite is high, and the corrosion index of MgO-C brick increases significantly. Generally, SiO2 content in graphite shall be limited to less than 3%. If SiO2 accounts for 50% of ash, the purity of graphite shall be more than 95%.

3. Particle size and shape of flake graphite
As mentioned earlier, there is a direct relationship between the particle size of graphite and the oxidation temperature. Large-scale graphite usually has high purity and good oxidation resistance. At the same time, large-scale graphite can significantly improve the thermal shock stability of magnesia carbon brick. Large-scale graphite can also optimize the mixing and molding properties of the mixture. However, the price of large flake graphite is high.
In the shape of graphite, the thinner the scale, the better. Firstly, flake graphite can obviously improve the thermal shock stability of MgO-C brick. This is because the elastic modulus of products made of thin graphite after heating is lower than that of magnesia carbon brick made of ordinary graphite; At the same time, when the amount of graphite is the same, the dispersion of flake graphite is better, which improves the matrix of the product, and the number of obstacles to crack propagation increases during thermal shock. Secondly, the oxidation resistance of MgO-C brick made of flake graphite is also high, because the oxidation resistance of MgO-C brick made of thin flake graphite is also high because the effective area of oxidation at the end of flake graphite is small. In the batching system, the smaller the size of the refractory aggregate, the better the effect of using flake graphite.
In general, carbon bonded refractories, the particle size of flake graphite shall be ≥ 0.105mm, preferably ≥ 0.21mm; The scale thickness should be < 0.02M, preferably < 0.01mm. At the same time, the components meeting this requirement account for more than 30% of the total graphite.

4. Addition amount of flake graphite
Adding a certain amount of flake graphite into magnesia refractories is beneficial to improve the corrosion resistance and slag penetration resistance of products. According to the calculation, the refractory containing 3% ~ 4% carbon can effectively prevent the penetration of slag into the brick. However, carbon is easy to be oxidized, and its actual amount should be more.
Generally speaking, the additional amount of flake graphite in MgO-C brick should be between 15% ~ 20%. When the addition amount is high, the dissolution of MgO-C brick tends to increase, because when the graphite content increases, the brick structure after decarburization coarsens, resulting in an increase in the erosion of slag per unit volume of a brick, accelerating the loss of MgO to slag; At the same time, with the increase of graphite content, the ash content also increases, which reduces the corrosion resistance of brick. In addition, if too much graphite is added, it is difficult to form during production, and the products are easy to oxidize during use. In carbon bonded refractories, if the carbon content is less than 10%, a continuous carbon net cannot be formed in the products, and the advantage of carbon cannot be effectively brought play; From the point of view of thermal shock stability, the addition of graphite is less than 10% ~ 15%, and the thermal shock resistance of brick is obviously reduced.
When determining the amount of graphite in actual production, it shall be determined according to the service conditions of carbon bonded refractories, such as the type of smelting equipment, oxygen partial pressure in molten steel and slag, slag characteristics, smelting temperature, and tapping temperature; The addition amount of graphite can also be determined according to whether the produced products emphasize corrosion resistance or thermal shock stability, or require high strength or oxidation resistance.