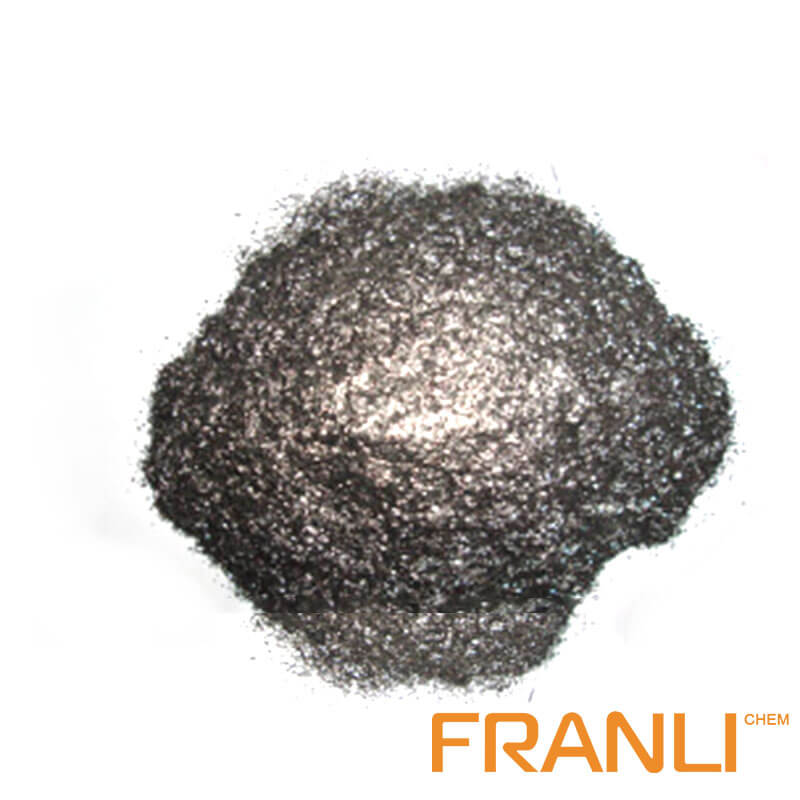
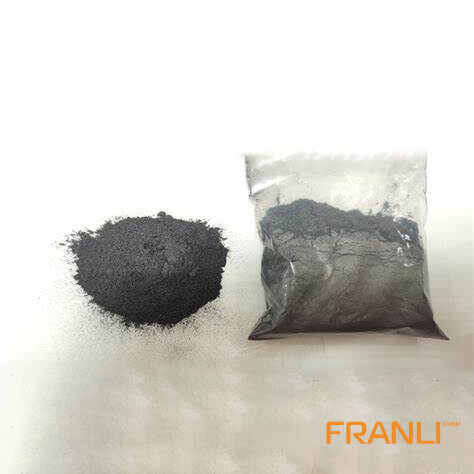
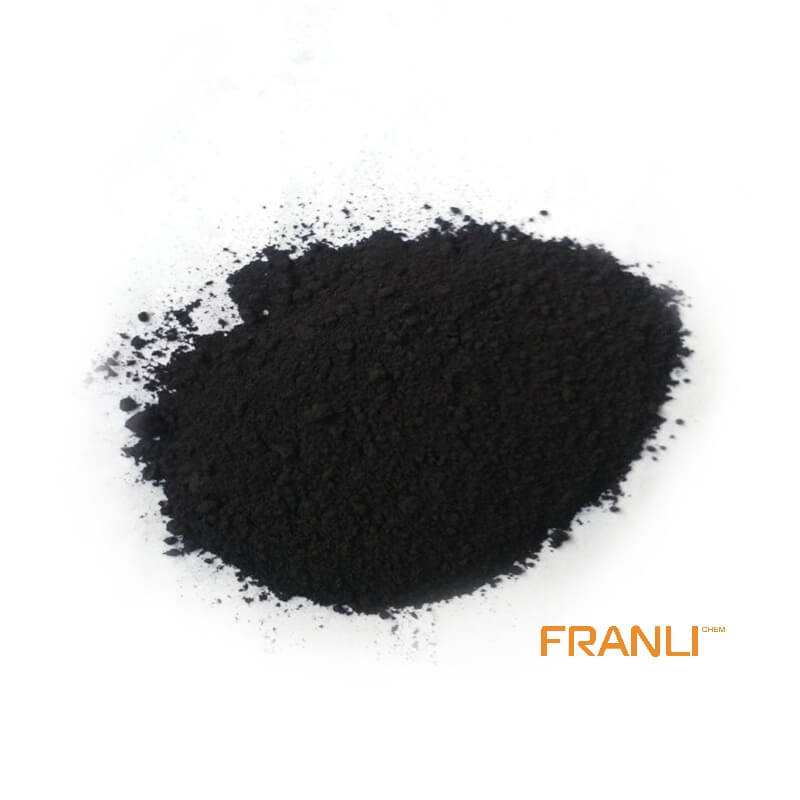
Flake Graphite
Size
0.01mm
Carbon Content
99%min
Package
25kg small bags into ton bags
Origin
China
Features
thermal shock resistance, lubricity, conductivity and plasticity…
Application
Lead battery plates positive and negative conductive agent, lithium batteries nickel hydrogen etc
Natural flake graphite has superior physical and chemical properties and is widely used in metallurgy, coatings and refractory industries. It is an important non-metallic raw material that is indispensable for today’s high-tech. Flake graphite is divided into large flake graphite and fine flake graphite according to the size of its scales. Usually, large flakes refer to +32 mesh, +50 mesh, +80 mesh, and +100 mesh flake graphite.
Request a quote
Flake graphite is natural crystalline graphite, which looks like fish phosphorus. It belongs to a hexagonal crystal system and has a layered structure. It has good properties such as high-temperature resistance, conductivity, heat conduction, lubrication, plasticity and acid, and alkali resistance. Flake graphite is a natural solid lubricant with rich resources and low prices. On December 2, 2015, the Department of land and resources of Inner Mongolia Autonomous Region said that geological explorers recently found a super large flake graphite mine in Alashan League, Inner Mongolia. At present, the total amount of proven graphite resources is 130 million tons, accounting for about 7.3% of the world’s recoverable reserves, with an average grade of 5.45%. Flake graphite, as the functional filler of coatings, is mainly used in anti-corrosion coatings, fire retardant coatings, and conductive coatings. As an anti-corrosion material, it is an antirust primer made of carbon black, talc powder, and oil, which has good corrosion resistance to chemicals and solvents; If zinc yellow and other chemical pigments are added to the formula, the antirust effect is better.

Expandable graphite is used as a fireproof filler. It is a graphite interlayer compound obtained by chemical or electrochemical treatment with natural graphite flakes as raw materials. Under heating conditions, the volume of expandable graphite expands rapidly (up to 300 times) to suffocate the flame and form expansions at the same time, so as to isolate the flame and delay or interrupt the flame spread. It is non-combustible, has good flexibility, high surface energy, and good strength of the carbonized layer. However, the volume and dosage of the expansion body should be selected appropriately. The test shows that 150um particle, 30% expansion multiple, and 5% dosage are the most suitable. Flake graphite can be directly used as carbon conductive filler, and can also be made into composite conductive filler for conductive coating. However, due to a large amount of graphite flake, the performance of the coating will become brittle, which limits its application. Therefore, measures should be taken to further improve the conductivity of graphite and effectively reduce the addition of graphite flakes.
How to avoid the corrosion of equipment by strong corrosive media, so as to reduce equipment investment and maintenance cost and improve production efficiency and profit is a difficult problem that every chemical enterprise always needs to solve. Many products have corrosion resistance but not high-temperature resistance, but flake graphite has both advantages. The following describes in detail how to flake graphite solves the problem of equipment corrosion:
1. Excellent thermal conductivity. Flake graphite also has good thermal conductivity. It is the only non-metallic material with thermal conductivity higher than that of metal. The thermal conductivity is twice that of carbon steel and seven times that of stainless steel. Therefore, it is suitable for heat transfer equipment.
2. Excellent corrosion resistance. Various types of carbon and graphite have excellent corrosion resistance to all concentrations of hydrochloric acid, phosphoric acid, and hydrofluoric acid, including fluorine-containing media. The service temperature is 350 ℃ – 400 ℃, which is the temperature at which carbon and graphite begin to oxidize.

3. Resistant to certain high temperatures. The service temperature of flake graphite depends on the type of impregnating material. For example, phenolic impregnated graphite can withstand 170-200 ℃. If an appropriate amount of silicone resin-impregnated graphite is added, it can withstand 350 ℃ at most; When phosphoric acid is deposited on carbon and graphite, the oxidation resistance of carbon and graphite can be improved, and the actual operating temperature can be further improved.
4. The surface is not easy to be structured. Flake graphite has very little “affinity” with most media, so it is not easy to adhere to dirt on the surface. It is especially suitable for condensing equipment and crystallization equipment.
It can be seen that the equipment added with flake graphite has excellent corrosion resistance and physical and mechanical properties, and can be widely used in the manufacturing of anti-corrosion equipment in the chemical industry.