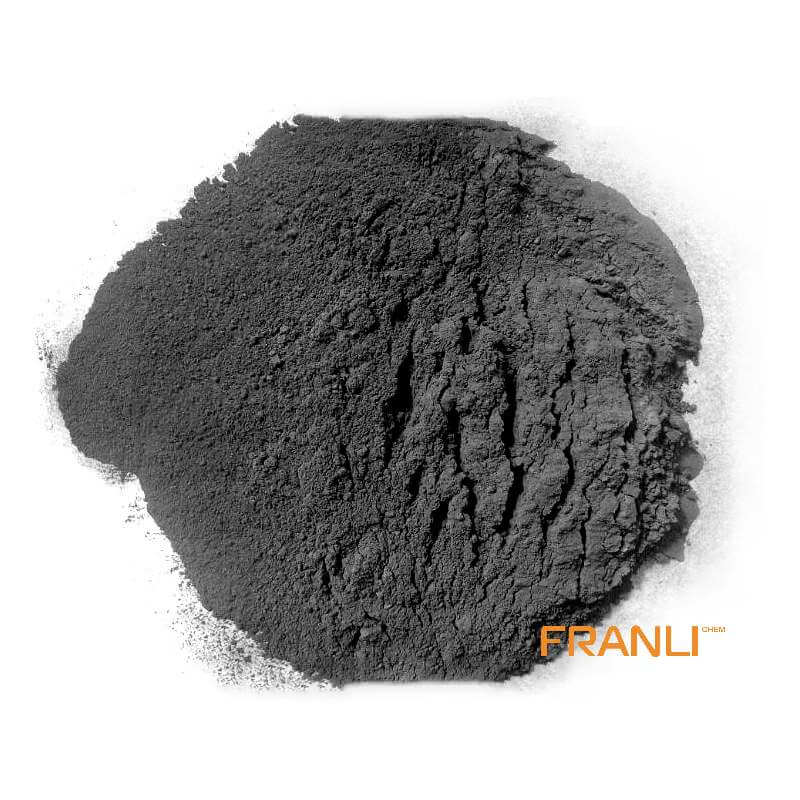
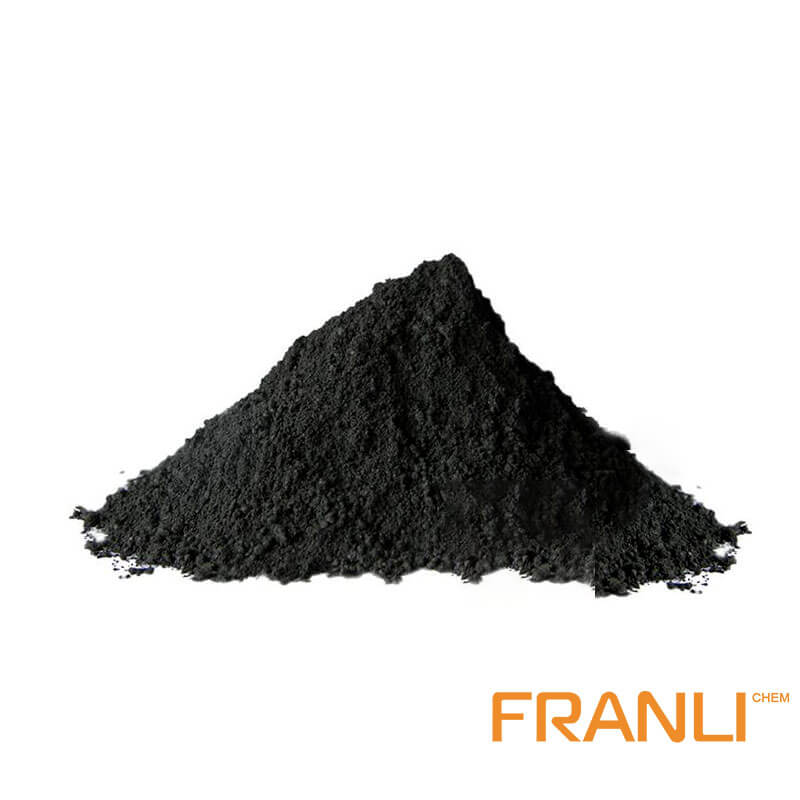
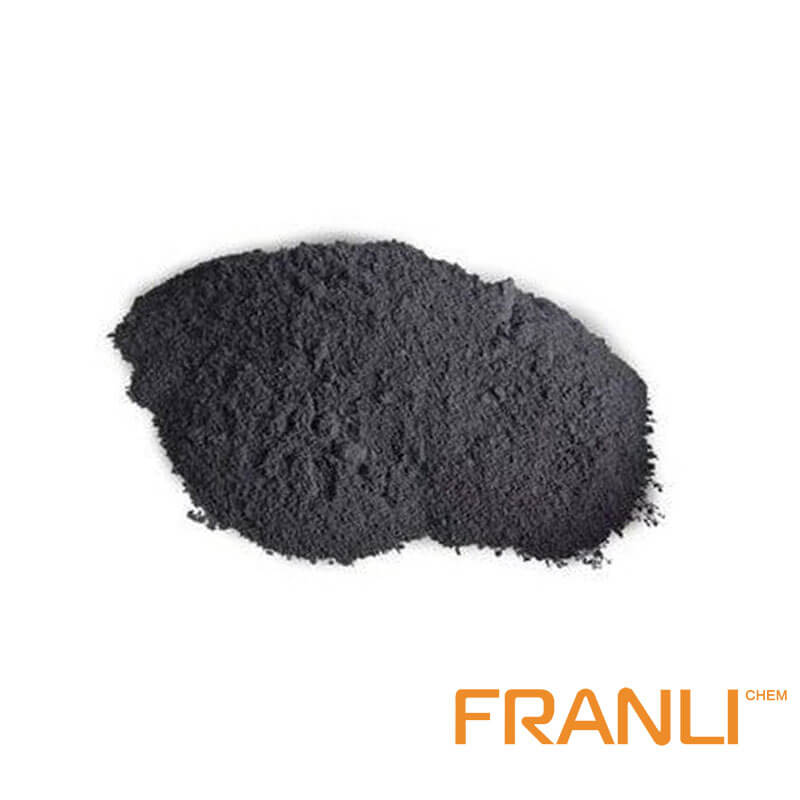
Artificial Graphite
Size
0.01mm or 0.07mm,etc
Package
25 kg small bags into ton bags or ton bags
Features
Good wear resistance, corrosion resistance, good thermal conductivity, etc.
Application
Can be used in making heat exchanger, reaction tank, absorption tower, etc.
There are many kinds of artificial graphite and different production processes. In a broad sense, all graphite materials obtained by carbonization of organic matters and treated by high temperature after being treated with graphite can be collectively referred to as artificial graphite.In the narrow sense, artificial graphite usually refers to the massive solid materials prepared by batching.
Request a quote
Most of the negative electrodes of lithium-ion power batteries for electric vehicles are artificial graphite, which has outstanding advantages over natural graphite in rate performance, electrolyte compatibility, and cycle life, accounting for a high proportion of the shipment of the whole negative electrode materials.
In terms of morphology and structure, natural graphite is quite different from man-made graphite, and its gram capacity is high, which can be seen in its SEM and powder data.
The main raw materials for the production of artificial graphite are petroleum coke and asphalt coke, and their characteristics are compared as follows.

Oil series needle coke is a high-quality petroleum coke prepared by coking thermal cracking residue or catalytic residue with high aromatic hydrocarbon content (coal series needle coke produced by coal tar and its fractions). Its coke block has uniform pore size distribution, smooth surface, shiny long fiber structure, slender or oval shape, and high directivity. After crushing, The particles are slender and acicular. During graphitization, it is easy to form a layered structure of graphite, with a small linear expansion coefficient and low resistivity.
The common indexes characterizing the characteristics of acicular petroleum coke are volatile, ash, and sulfur. Volatile matter can characterize the coking degree of petroleum coke. The volatile matter of delayed coking petroleum coke is generally 7% – 18%; Sulfur mainly comes from crude oil and is a harmful component. In petroleum coke, it is mostly organic sulfur, such as mercaptan, sulfide, etc. Petroleum coke with high sulfur content will burst and expand abnormally during graphitization. In order to suppress this phenomenon, Fe2O3 can be added to the powder as an inhibitor to react with sulfide to produce FES, which will decompose slowly in the subsequent graphitization process to inhibit the sudden escape of sulfur. The true density can characterize the difficulty of graphitization of petroleum coke. The ash content is related to the salts of petroleum residue and coking conditions. For petroleum coke used in the production of general graphite materials, the ash content shall be less than 0.5%.
The preparation process of artificial graphite can be roughly divided into four steps: raw material pretreatment, granulation, graphitization, and ball milling screening.
Step 1: determine the formula of aggregate. That is various coke types, adhesives, and their respective proportions used in the precursor. By compiling several kinds of coke with different properties and particle sizes with a binder in a certain proportion into a batching list. The reason for formula design is that the artificial graphite structure belongs to powder structure. Through certain process operations, the carbon particles, powder, and binder form a uniform whole with a certain shape and function through the comprehensive action of chemical bond force, intermolecular force, mechanical adhesion force, and mechanical inlay bite force. The structure and properties of the powder depending on the proportion of various powder particles. Therefore, if these materials with different structures and properties are mixed in a certain proportion to make a uniform whole. A core material with comprehensive properties completely different from the raw material can be obtained.
The ingredient list mainly includes the following contents:
1.Type, quality index, and percentage of raw materials;
2.Particle size composition of dry materials;
3.Type, quality index, and percentage of the binder.
Step 2: crushing and shaping. The required petroleum coke or asphalt coke is shaped into particles with D50 of 2-20um. In this step, mechanical methods are often used for crushing. The reason for crushing is that although the particle size of the incoming petroleum coke or asphalt coke is reduced after pre-crushing, it is still about 10-50mm, fluctuates greatly, and is far from the particle size required by the formula. It can not be directly used in the production of artificial graphite. The process of crushing is the process that the solid overcome the cohesion and decomposes from large blocks into small blocks or fine powders. The characteristics of this process are: the particle size of materials becomes smaller, the total surface area per unit mass increases and more energy needs to be consumed.
Step 3: mix and knead. Mix the oil series or coal series dry materials with different particle sizes treated in the second step, then add liquid asphalt binder and use mechanical mixing to make the materials evenly distributed. The reason why the binder should be added is that due to different types of oil or coal coke, there is no binding capacity between the powder particles, and it is necessary to add binders such as asphalt so that the dispersed particles can be bonded together to form a whole. By heating and kneading, the binder is thinly and evenly wrapped on the surface of the particles and infiltrates and fills the open pores of the powder particles to form a paste with uniform quality, good plasticity, and certain compactness and fluidity. The wetting effect of asphalt and solid carbon raw material particles affects the kneading process. As coal tar pitch is a weakly polar substance, and water is a polar substance, if the water content on the surface of powder particles exceeds the standard, a strong adsorption layer will be generated on the surface of coke particles, which will reduce the infiltration effect of asphalt on carbon particles.

Step 4: graphitization. That is, in the graphitization furnace, heating to more than 3000 ℃ in the protective medium will change the planar network of hexagonal carbon atoms from the network structure in two-dimensional space to the ordered graphite structure in three-dimensional space. In the production of artificial graphite, the Acheson furnace is mostly used. This method belongs to the direct heating method. The power supply is in direct contact with the graphite products. The products themselves are conductors. The products reach the graphitization temperature through resistance heating. The graphitization process can be divided into the following steps
1、 500-1000 ℃, in this process, most of the aliphatic chain hydrocarbons and oxygen-containing functional groups in the graphite microcrystals are cracked to escape small molecular gases such as CO, CO2, and H2O. At the same time, the graphite microcrystals are driven by surface energy and close to each other radially and axially;
2、 1000-1500 ℃, in this process, some prominent lamellar molecules in the graphite-like microcrystals further undergo high-temperature cracking, leaving a certain amount of electrons in the edge carbon of the graphite layer, and the activity is particularly high. At the same time, due to the existence of some oxygen-containing functional groups, the graphite microcrystals have a certain polarity in the radial direction, making the graphite microcrystals self-assembly in the radial direction, Cause the parallel arrangement of graphite microcrystals in the radial direction;
3、 In the process of graphitization at 1500-2250 ℃, the system obtains more energy. Under the action of surface energy and large π bond, the graphite microcrystals are arranged in parallel along the axis. At the same time, the thermal vibration frequency of carbon atoms in the system increases, and the amplitude parallel to the plane grid increases, resulting in the gradual reduction of dislocation lines and grain boundaries on the crystal plane;
4、 2250-3000 ℃, in this process, the evaporation rate of carbon increases exponentially. At this time, the system is filled with various carbon atoms or their bulk molecules, and the radial spacing of graphite crystallites is close to the molecular level. Under the driving force of carbon autocatalysis and interface energy at the edge of the graphite layer, various free carbon atoms react with the edge of adjacent graphite crystallites to form a C-C six-membered ring, Under the action of van der Waals force, the folds of the graphite layer disappear and tend to plane structure, and finally form a three-dimensional ordered graphite material.
Step 5: coating carbonization. In this step, the artificial graphite is fully mixed with asphalt and resin polymers in a certain proportion, then carbonized at 1000-1300 ℃, and finally, a layer of amorphous carbon is coated on the surface of the artificial graphite, which can optimize the lithium-ion transmission rate of the graphite in the process of charge and discharge and improve the fast-charging capacity of the cell.
Step 6: ball milling and screening. The graphitized materials are transported to the ball mill through a vacuum for physical mixing, ball milling, screening, inspection, measurement, packaging, and warehousing.
With the vigorous development of the electric vehicle market, the proportion of shipments of artificial graphite in the whole negative electrode material market is increasing. At present, the main negative electrode suppliers in China are better, Shanshan, putilai and Kaijin, with a total market share of more than 70% of China’s lithium battery negative electrode material market, of which beiteri is the leading enterprise of natural graphite materials, The market accounts for more than 70%, and the artificial graphite materials are mainly composed of Shanshan, putailai and Kaijin. The total artificial graphite market accounts for nearly 60%.