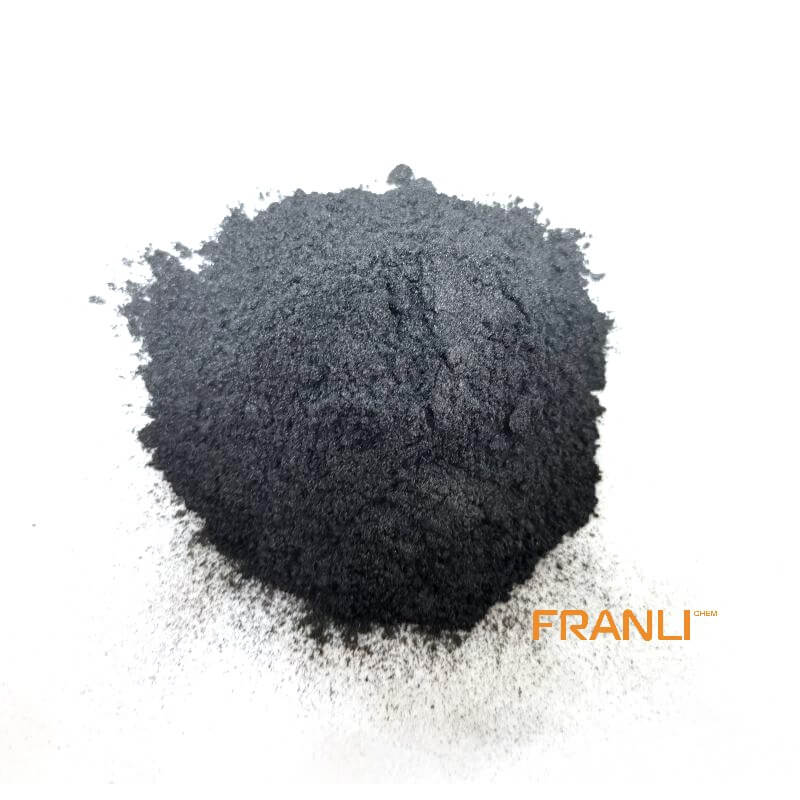
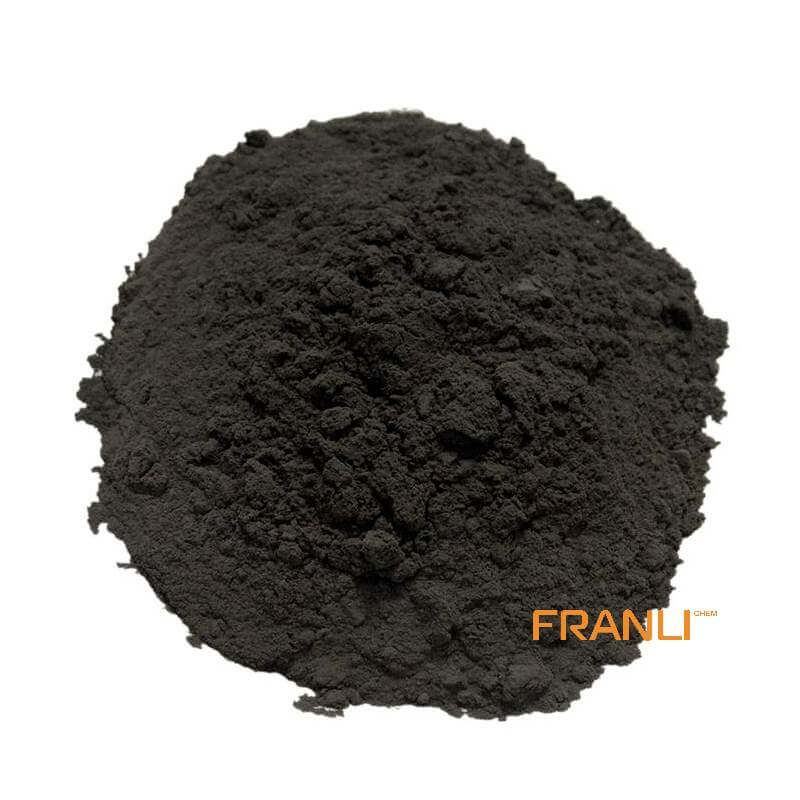
Amorphous Graphite
Size
45μm, 75μm, 150μm, etc
Package
25kg small bags into ton bags or ton bags
Origin
China
Features
Under high temperature conditions, it has special oxidation resistance, etc
Application
Casting coatings, oil field drilling, battery carbon rods, steel, casting materials, refractories, dyes
It is an aggregate of amorphous graphite. The crystal form can be seen only under the electron microscope. Amorphous graphite ore is gray black and steel gray, generally dull, with dense massive, earthy, layered, and lamellar structures. This kind of graphite lacks luster, its lubricity is lower than that of flake graphite, and its selectivity is poor. However, the grade is high, the carbon content is generally 60% ~ 80%, a few are up to more than 90%, the ash content is 15% ~ 22%, the volatile content is 1% ~ 2%, and the moisture content is 2% ~ 7%.
Request a quoteNatural amorphous graphite has the characteristics of high-temperature resistance, chemical corrosion resistance, conductivity, heat conduction, and self-lubrication. It is widely used in metallurgy, electrical, refractory, battery materials and other fields.

1 Application in the metallurgical field
Natural amorphous graphite is widely used in metallurgy as a carburizing agent, heating agent, and release agent.
Fujing pure uses industrial waste and amorphous graphite to prepare steel mold casting protective slag. amorphous graphite has been popularized to replace pig iron for carburization in 5 t and 25 t electric arc furnaces in the Jiangxi steel plant.
Yan Hongyan et al. Studied the carburizing effect of amorphous graphite raw ore at 1600 ℃ and its effect on the mass fraction of elements such as s, N, and O in steel. The results show that the carburizing effect of amorphous graphite is equivalent to that of other carburizing agents, and has little effect on S, N, and O in steel. In the electrolytic aluminum industry, before the anode carbon block and steel claw are assembled, it is necessary to spray or dip graphite at a certain height of the steel claw leg to prevent high-temperature phosphorus pig iron from excessively eroding the steel claw leg so that the phosphorus pig iron ring is easy to separate from the surface of the steel claw leg. In China, the mixture of kerosene and amorphous graphite or the mixture of water and amorphous graphite is widely used to dip the anode steel claw.
2 Application in grounding field
In order to prevent damage caused by lightning attacks and ensure personal and property safety, some parts of transmission line towers, substations, and high-rise buildings need to be connected to the ground, which is called grounding. Graphite is an ideal grounding material because of its conductivity, thermal conductivity, and good chemical stability.
Wu Shaopeng and others prepared conductive concrete by adding an appropriate amount of amorphous graphite to asphalt concrete. Some domestic enterprises press amorphous graphite into grounding resistance reduction modules.
Liu Dezhou and others used an amorphous graphite resistance reducer to improve the grounding resistance. The practice has proved that the method of spreading amorphous graphite to reduce the soil resistivity in high resistivity areas such as deserts and arid and rainless mountainous areas has a significant effect on reducing the grounding resistance of the grounding grid.
3 Applications in the refractory field
In order to improve the thermal shock resistance and slag erosion resistance of refractories, a certain amount of large flake graphite is usually added to traditional production ingredients. In recent years, with the need for special steel smelting, the development and application of low-carbon refractories have attracted extensive attention. In order to ensure the uniform distribution of a small amount of graphite in the products, it is necessary to reduce the particle size of the graphite used. amorphous graphite itself has fine crystals and is easier to make ultrafine powder. It has become a development trend to use amorphous graphite to gradually replace flake graphite to prepare low-carbon refractories.
Wang Tongsheng et al. Added ultra-fine amorphous graphite to the carbon brick. The results showed that the addition of amorphous graphite promoted the formation of silicon carbide whiskers in the material, significantly improved the compressive strength and thermal conductivity of the carbon brick, and increased 1 μ The volume ratio of ultra micropores below M.
Liang Xiong and others introduced amorphous graphite as an activated carbon source into the preparation of aluminum carbon refractories containing metal aluminum powder, silicon powder, and silica powder. The results show that natural amorphous graphite has higher reaction activity than flake graphite. The introduction of amorphous graphite can promote the formation of aluminum nitride and silicon carbide whiskers in the material matrix and improve the mechanical properties of aluminum carbon materials.

4 Applications in the field of battery materials
Using natural amorphous graphite as aggregate and coal tar pitch as binder, carbon rods for dry cells are prepared by kneading extrusion roasting grinding wax dipping process, which has a long production history. Hunan Changning Carbon Co., Ltd. and Chenzhou Yongfa graphite products Co., Ltd. have an annual output of more than 20000 tons of carbon rods for various amorphous graphite-based dry batteries, accounting for more than 60% of the global output, which improves the application value of natural amorphous graphite to a certain extent. Natural amorphous graphite has small grains and different orientations, which is conducive to absorbing the deformation energy caused by lithium-ion insertion and detachment. It has better structural stability and rate performance. It has a good application prospect in the field of cathode materials for lithium-ion power batteries. In recent years, natural amorphous graphite-based cathode materials for lithium-ion batteries have been studied more and more.
He Ming et al. Coated amorphous graphite with core-shell structure was prepared by coating a layer of resin carbon on the surface of amorphous graphite, which reduced the first irreversible capacity of amorphous graphite.
He yuede and others coated resin carbon on the surface of spherical amorphous graphite particles by liquid-phase impregnation process to improve their electrochemical properties. For the first time, the coulomb efficiency was increased from 81.0% to 92.7%.
Lin Zhengyu and others used amorphous graphite as conductive aggregate and thermosetting resin as a binder to prepare amorphous graphite/resin composite bipolar plates for proton exchange membrane fuel cells by the molding process. Using bisphenol a vinyl resin with a content of 18% ~ 20% as a binder and amorphous graphite powder with the particle size of 200 mesh ~ 250 mesh as conductive aggregate, the properties of bipolar plate prepared under the molding conditions of curing temperature 140 ~ 145 ℃, molding pressure 15 ~ 20 MPa and molding time 18 ~ 22 min are as follows: bending strength > 25 MPa, conductivity > 100 s / cm and gas permeability < 3 × 10-5 mL/(s·cm2).
5 Application of rubber filler and other fields
A large number of fillers with different functions are often added to the rubber formula to realize its use-value. At present, carbon black is the most important rubber reinforcing filler, and its dosage accounts for about 40% ~ 50% of the total mass. Although carbon black has excellent performance, it has some disadvantages, such as large processing pollution, high energy consumption, and ease to fly when adding. Therefore, the rubber industry has been looking for alternative materials of carbon black.
LV Jiaping and others studied the effect of amorphous graphite partially replacing carbon black N550 on the properties of ethylene acrylate rubber (AEM) compound. The results showed that after amorphous graphite partially replaced carbon black N550, the vulcanization time of the AEM compound was greatly shortened, and the heat generation and raw material cost were reduced before the heat aging resistance and oil resistance were maintained.
Wu Jiangtao et al. Studied the influence of natural amorphous graphite in different mining areas on the properties of natural rubber (NR). The results show that amorphous graphite improves the physical properties of NR compound to a certain extent, but the influence of amorphous graphite in different mining areas on the physical properties of NR compound is quite different. The particle size of amorphous graphite has a great influence on the physical properties of NR compound when the particle size is greater than 5 μ M, the amount of amorphous graphite in NR compound has a critical value and precipitation phenomenon. The above research shows that amorphous graphite has similar chemical composition and microstructure to carbon black, so it is possible to partially replace carbon black for rubber reinforcing filler. amorphous graphite has the characteristics of good chemical stability, heat conduction, and lubrication. It is easy to disperse in the rubber matrix after ultrafine grinding, which is conducive to improving the performance of rubber products. Therefore, natural amorphous graphite as a new rubber reinforcing filler has excellent potential application value.
6 Application in the field of electric carbon products
Natural amorphous graphite has the advantages of high graphitization degree, good conductivity, heat conduction and lubricity, and strong adhesion with asphalt, resin, and other adhesives. It has good application value in the field of electric carbon products. The final performance of carbon graphite products largely depends on the interaction between binder asphalt and aggregate particles in the kneading process.
Duan Shengzhi studied the preparation of copper/carbon composites by powder metallurgy with natural amorphous graphite and copper powder as the main raw materials. The effects of amorphous graphite purity and ratio on the microstructure, conductivity, flexural strength, hardness, and friction and wear properties of the composites were studied. The results show that with the increase of amorphous graphite purity, The main performance indexes of copper/carbon composites show an increasing trend. When the proportion of amorphous graphite is 7.5%, the conductivity, and friction, and wear properties of copper/carbon composites are relatively optimal. The lubricity of amorphous graphite to copper/carbon composites is slightly less than that of flake graphite, but it can reduce the wear rate of composites.
An in-depth and comprehensive understanding of the basic structure and characteristics of natural amorphous graphite is the key to guiding the development of the amorphous graphite industry. Therefore, the basic research of amorphous graphite should be further strengthened. At the same time, we should further strengthen the development of high-efficiency, environmental protection, and low-cost purification technologies, particle shaping, and surface modification technologies, encourage independent innovation and product R & D and promote the industrialization of relevant scientific research achievements. With the continuous development of relevant new theories, new technologies, and new equipment, natural amorphous graphite will be widely used in the fields of new refractories, new energy materials, and advanced composites.