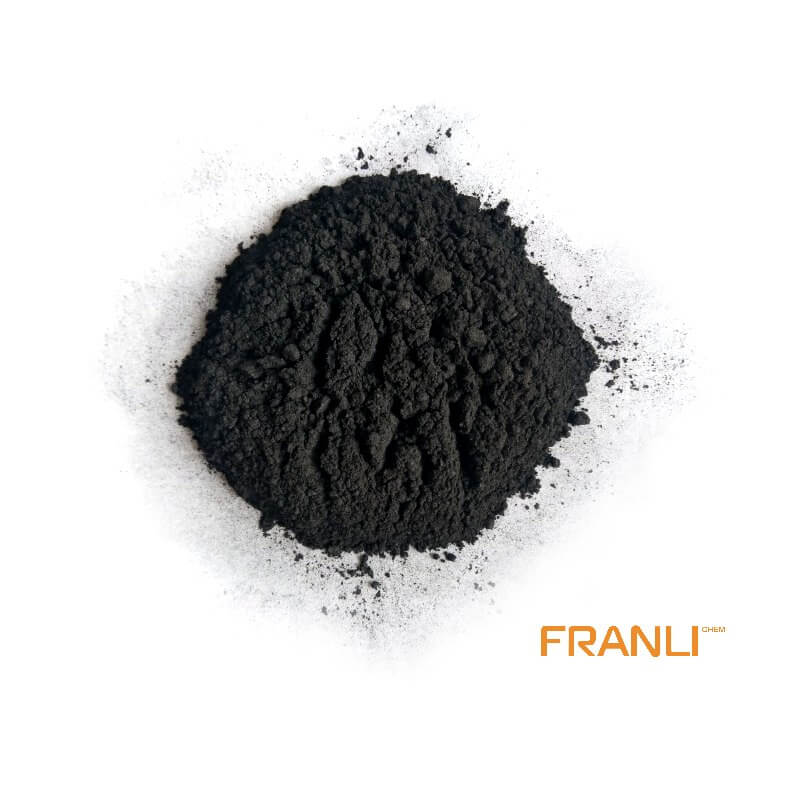
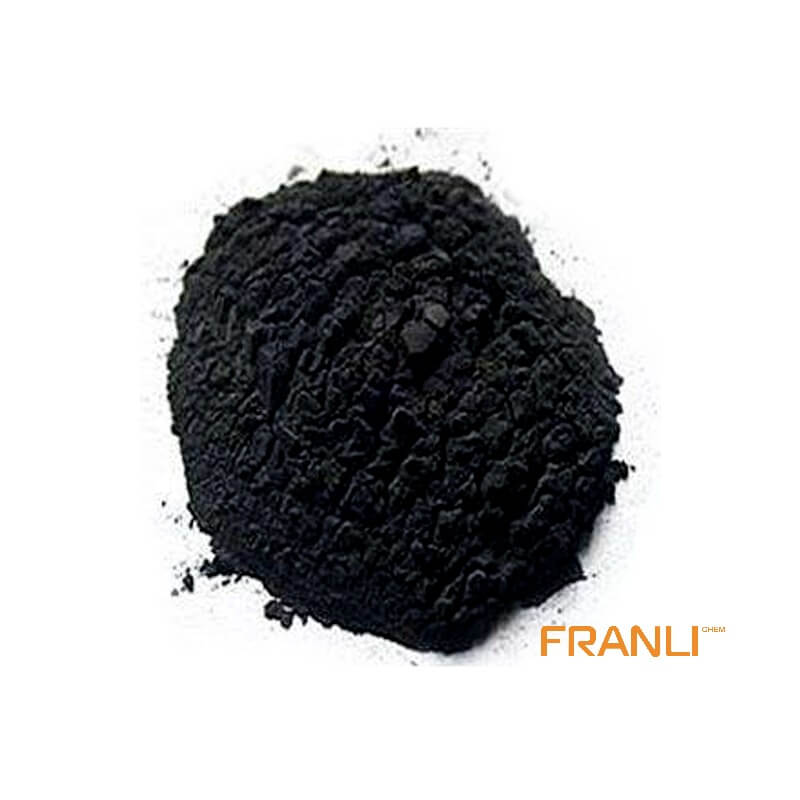
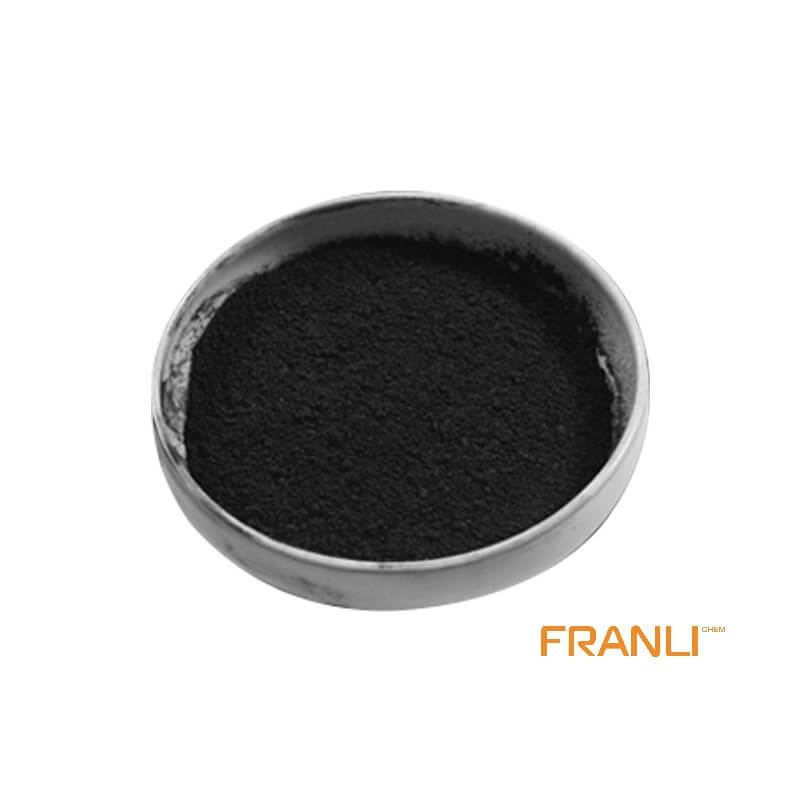
Purity Graphite
Size
According to your requirements
Package
25 kg small bags into ton bags or ton bags
Features
good temperature resistance, self lubrication, conductivity, etc.
Application
Can be used in machinery, metallurgy, chemical industry, military industry, etc.
High purity graphite is also called molded graphite, which means that the carbon content of graphite is more than 99.99%, which has good electrical conductivity, high temperature resistance, oxidation resistance, low resistance coefficient, corrosion resistance, high purity, self lubrication, thermal shock resistance, isotropy, easy to be machined and so on.
Request a quote
High purity graphite is more and more used in modern life. How to produce high purity graphite and what is the process of high purity graphite? I believe many people want to know. Let’s learn about high-purity graphite.
Graphite is an allotrope of carbon. It is a gray-black opaque solid formed at high temperatures. Because of its stable chemical properties, high-temperature resistance, and corrosion resistance, it is widely used as a refractory, conductive material, high-temperature metallurgical material, and so on in the industrial field.

Graphite in nature usually contains silicon oxide, alumina, and copper oxide impurities, so it needs to be purified and used. High purity graphite with carbon content higher than 99.99% has the advantages of better high-temperature resistance, corrosion resistance, thermal shock resistance, small thermal expansion coefficient, self-lubrication, low resistance coefficient, and easy machining, which is more conducive to industrial production and processing.
Raw material
The raw materials for producing high-purity graphite include aggregate, binder, and pregnancy. Needle petroleum coke and asphalt coke are commonly used as aggregate coke. Acicular petroleum coke is easy to graphitize at high temperature, has better conductivity and thermal conductivity, and has a lower linear expansion coefficient; Graphite obtained from pitch coke at the same graphitization temperature has higher resistivity but higher mechanical strength. In the production of rocky desertification products, petroleum coke is usually mixed with a certain proportion of asphalt coke to obtain higher mechanical strength.
Coal tar pitch is usually used as a binder. It is the product of coal tar distillation and processing. It is a black solid at room temperature and has no fixed melting point.
The properties of graphite impregnated determine the chemical stability, thermal stability, mechanical strength, and application temperature of graphite. At present, the commonly used impregnants are usually synthetic resin and metal.
Calcination
Purification and calcination are to heat various solid carbon raw materials at high temperatures under the condition of isolated air. Due to the different cooking temperatures of the aggregate or the geological year of the medium, the water impurities contained in the internal structure are also different. The use effect of the product will not be effected until the magazine is removed after calcination and purification.
Milling
The calcined and purified material still has a large particle size, large fluctuation, and uneven composition. The aggregate needs to be ground to meet the batching requirements.
Kneading
The ground powder shall be mixed with coal asphalt binder in a certain proportion and then put into the heated kneader for kneading to make the materials evenly distributed. After kneading, the material is pressed and formed. There are four common forming methods: extrusion forming, molding forming, vibration forming, and isostatic pressing forming.
Roasting
Roasting refers to the heat treatment of the pressed green body at about 1000 ℃ under the condition of isolated air. The formed carbon products are calcined to carbonize the binder into binder coke.
Dipping
During the roasting process, micropores will be formed in the carbon products, and there are also open pores in the original aggregate coke particles, which will affect the conductivity and chemical corrosion resistance of the final graphite products. The purpose of impregnation is to fill the pores of carbon products with impregnating agents such as molten asphalt to improve the performance of finished products.
Graphitization
Graphitization is a high-temperature heat treatment process that converts thermodynamically unstable non-graphitic carbon into graphitic carbon through thermal activation. It is also the last step in the purification of high-purity graphite.
High purity graphite is an ideal inorganic non-metallic material, which can be used in advanced refractory materials and coatings, stabilizers for initiating explosive materials in military industry, pencil lead in light industry, carbon brush in the electrical industry, electrode in the battery industry, catalyst additives in the chemical fertilizer industry, etc.

High purity graphite has the characteristics of high strength, high density, high purity, high chemical stability, dense and uniform structure, high-temperature resistance, high conductivity, good wear resistance, self-lubrication, and easy processing. It is widely used in metallurgy, chemical industry, aerospace, electronics, machinery, nuclear energy, and other industrial fields. In particular, high-purity graphite with large specification and high quality, as an alternative material, has broad application space and broad application prospects in the field of high technology and new technology.
The above is the manufacturing process of high-purity graphite. Understanding the manufacturing process and characteristics of high-purity graphite can enable us to make better use of high-purity graphite and create a better life with high-purity graphite.