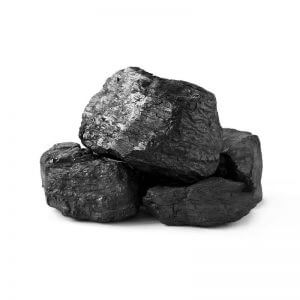
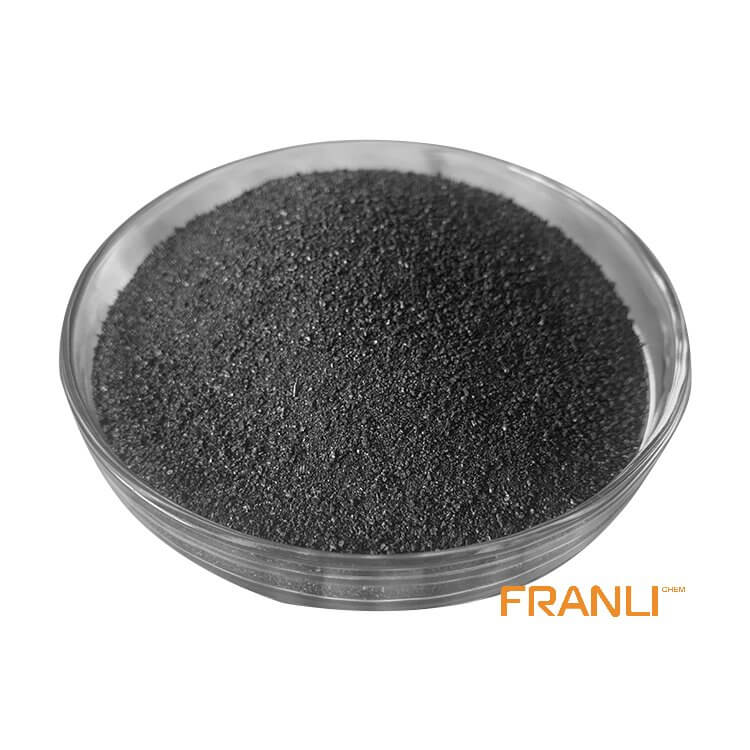
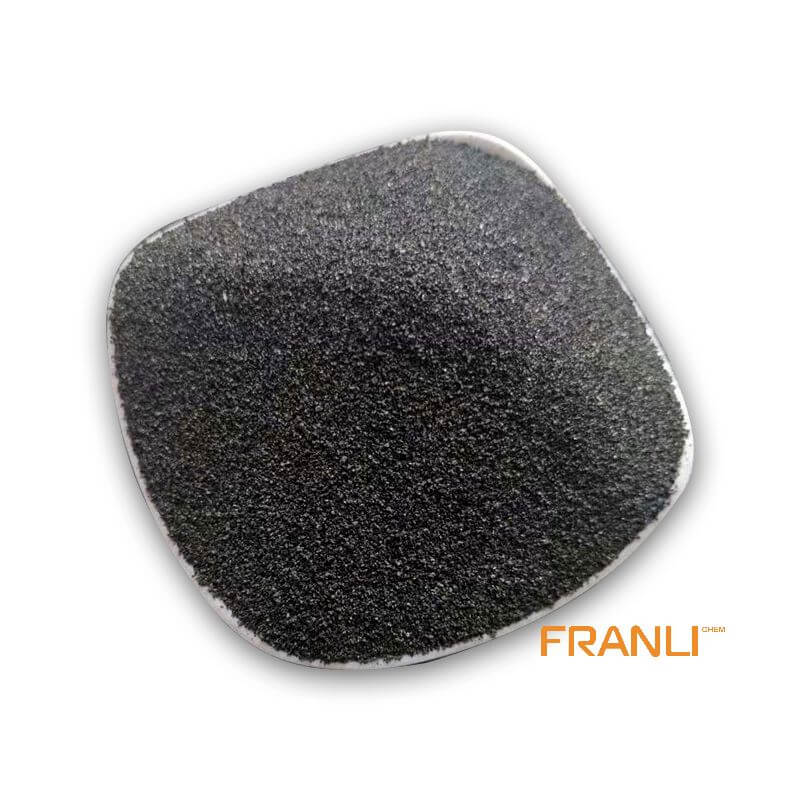
Petroleum Coke
Size
According to your requirements
Package
25 kg small bags into ton bags or ton bags
Features
Low ash content and low boiler ash discharge, etc.
Application
Depending on its quality, petroleum coke can be used in industries such as graphite, smelting and chemical industry, etc
Petroleum coke, as a byproduct of petroleum, is produced in the process of petroleum processing, that is, the crude oil is distilled to separate light and heavy oil, and the heavy oil is converted into petroleum coke by hot cracking. If petroleum coke can be obtained directly from petroleum processing, then the petroleum coke is raw coke or ordinary coke. Petroleum coke has irregular shape, dark gray or black, porous structure and metallic luster.
Request a quote
Calcination is the first process of petroleum coke heat treatment, which is usually carried out at about 1300 ℃. The purpose is to remove the impurities such as moisture, volatile matter, sulfur, and hydrogen from petroleum coke, and to realize the structural and physicochemical properties changes of various carbonaceous materials. In this way, the hydrogen content of petroleum coke can be reduced, the graphitization degree of petroleum coke can be improved, and the mechanical strength, density, electrical conductivity, and oxidation resistance of petroleum coke can be improved.
At present, domestic petroleum coke calcination mainly adopts four ways: rotary kiln calcination, pot calciner, rotary calciner, and electric calciner. Due to the different structures of several furnace types, the process is also very different. Most of the petroleum coke calcination of the domestic and foreign pre-baked anode and commercial pre-baked anode manufacturers are mainly in-tank calciner and rotary kilns. The heating type of tank calciner is indirect heating of raw materials by the heat from refractory bricks, and the rotary kiln is direct contact heating of combustion gas and materials.

1. Calcination in rotary kiln
The rotary kiln calcination system has the advantages of large output, strong adaptability to raw materials, good operation conditions, a high degree of automation, and easy environmental protection. It is mainly used in large calcination production enterprises such as refineries abroad. Disadvantages: 1) large burning loss, the production process is characterized by direct heating, the petroleum coke is in direct contact with the oxygen in the flue gas and flows reversely with the flue gas, so it is easy to be oxidized and burned; When the content of fine coke in petroleum coke is large, the burning loss increases and the temperature of calcination zone is difficult to control. A large number of fine coke and high-temperature flue gas enter into the settling chamber at the kiln tail, resulting in the reduction of the real yield of petroleum coke. The common real yield of petroleum coke calcined in a domestic rotary kiln is about 70-73%, which shows that it causes great waste and increases the cost of the anode; ② The product quality is poor. Because the petroleum coke calcined in a rotary kiln is directly heated, the contact area between petroleum coke and refractory is large during the rotary kiln rotation, which causes the lining refractory to fall off and enter the raw material, resulting in the increase of ash content; The calcination time is about 1-1.5 hours, the content of fine coke is high, the calcination temperature of petroleum coke is not controlled, it is difficult to fully contract, the density and strength are not high, the average density is less than 2.01g/cm3 and fluctuates greatly, while the industry index of calcined petroleum coke is 2.08%; The refractory materials of kiln make-up air pipe and discharge chute are easy to be damaged and fall off, resulting in poor quality of calcined coke. ③ The investment of downstream supporting equipment is large and the maintenance cost of equipment is high. When the rotary kiln is calcined in a centralized way, the waste heat utilization of kiln flue gas is an important break-even point. It is better to produce steam and sell it directly.
If a large amount of steam is lack customers, waste heat power generation must be used; A large amount of powder leads to the secondary combustion of the dust in the flue gas after entering the combustion chamber, and the temperature of the combustion chamber is too high, which shortens the life of the combustion chamber; The incompletely burned dust and sulfide in flue gas adhere to the waste heat boiler, which not only reduces the heat exchange efficiency of the boiler but also leads to corrosion damage of the calcined waste heat boiler system; A large amount of dust in flue gas seriously affects the absorption effect of desulfurized on SO2 in flue gas, causing environmental pressure to enterprises.
2. Calcination in pot furnace
With the development of domestic pot calciner technology, it has the advantages of low requirements for raw materials, stable quality, low oxidation loss of materials, high purity of calcined materials, full utilization of volatile matter, high-temperature waste gas preheating cold air through the regenerator, and high thermal efficiency of the whole furnace.
The requirements of true density, specific resistance, tap bulk density, air, and CO2 reactivity of calcined coke closely related to carbon anode consumption are lower than those of rotary kiln. It is especially suitable for the present situation of the petroleum coke market with large-quality fluctuation. The disadvantages are small production capacity, low level of automatic production, large furnace body, high technical requirements of masonry, and long construction period.
3. Comparison of economic indexes between tank furnace and rotary kiln
(1) In the heat treatment process of petroleum coke calcination, there are great differences in heating mode, heating time, cooling mode, and requirements for raw materials and fuels between the two furnace types.
(2) In the economic aspect of production and operation, there are also great differences between the two types of furnaces in the aspects of equipment operation rate, calcination yield, and carbon burning loss, raw fuel, and power consumption, maintenance costs, etc
(3) There are also great differences in operating conditions and working environment of tank furnace and rotary kilns, such as single system capacity, labor intensity, degree of mechanization and automation, and their supporting equipment and engineering are not the same.

4. The calcination quality of petroleum coke has a great influence on the quality of prebaked anode, which affects the true density, resistivity, CO2 reactivity, air reactivity, tap bulk density, and other key qualities indicators of calcined coke. In terms of these quality indexes, the calcined coke produced by the tank furnace is better than that produced by the rotary kiln,In terms of calcination quality and physicochemical properties, the calcined coke produced by the pot furnace is better.
Based on the factors of different cooking processes and cost control in domestic refineries, the physical and chemical indexes of petroleum coke are also different. The increasing content of coke and sulfur in petroleum coke makes the calcination process control more and more difficult, the burning loss is increasing, the end equipment corrosion is serious, which leads to the rising calcination cost and the increasing pressure of production cost. The advantages of calciner in energy saving, quality reduction, and consumption reduction are more and more obvious than the rotary kiln, which greatly improves the competitiveness of production enterprises. Therefore, the use of can calciner in China is increasing gradually, and it has been valued by production enterprises all over the world. At present, the newly built domestic production line of petroleum coke calcination is basically pot calciner. Many enterprises that used the rotary kiln to calcine petroleum coke have demolished the rotary kiln and converted it into pot calciner.
Explore and pay attention to the official account: ZSTSYJY grasps the aluminum and carbon industry knowledge and obtains the aluminum carbon industry service.