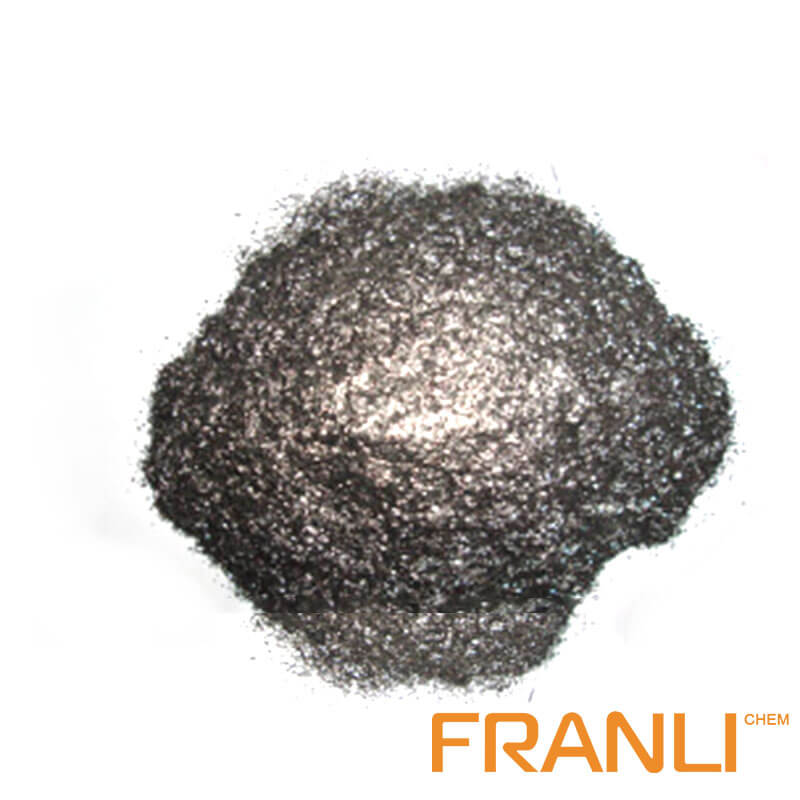
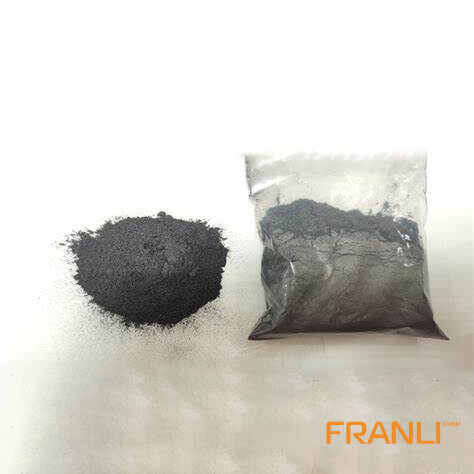
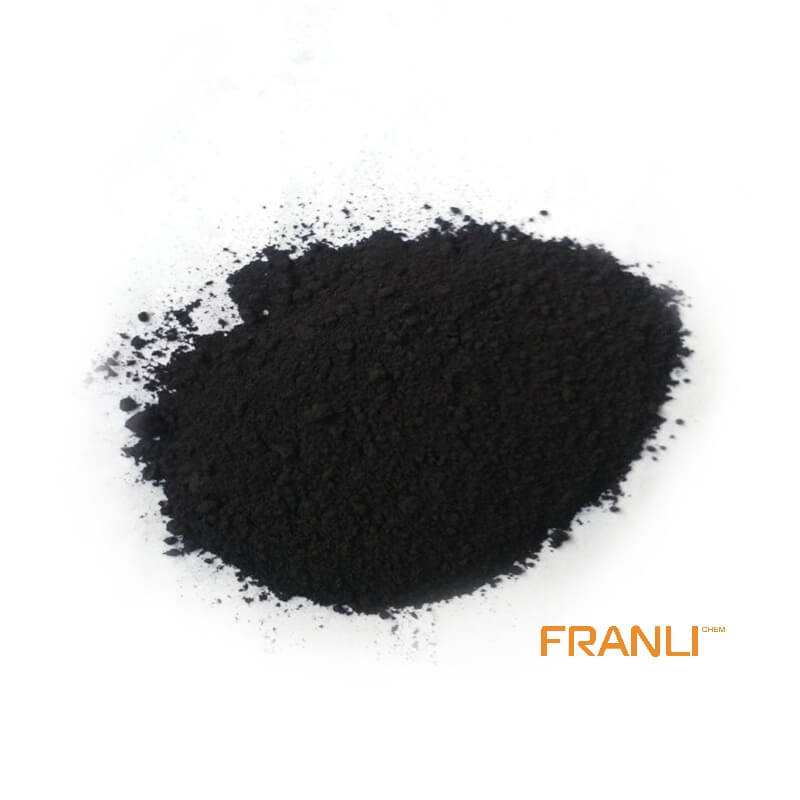
Flake Graphite
Size
0.01mm
Carbon Content
99%min
Package
25kg small bags into ton bags
Origin
China
Features
thermal shock resistance, lubricity, conductivity and plasticity…
Application
Lead battery plates positive and negative conductive agent, lithium batteries nickel hydrogen etc
Natural flake graphite has superior physical and chemical properties and is widely used in metallurgy, coatings and refractory industries. It is an important non-metallic raw material that is indispensable for today’s high-tech. Flake graphite is divided into large flake graphite and fine flake graphite according to the size of its scales. Usually, large flakes refer to +32 mesh, +50 mesh, +80 mesh, and +100 mesh flake graphite.
Request a quote1. Introduction
Flake graphite has been widely used in machinery, chemical industry, refractory, conductive material, and other industries because of its unique structure, which has excellent properties such as high-temperature resistance, lubrication, conductivity, and heat conduction. According to the degree of crystallization of graphite, graphite is generally divided into crystalline graphite and cryptocrystalline graphite. Crystalline graphite is also called flake graphite, with high crystallinity and sheet shape. China has abundant graphite resources. In 2016, the national mineral resources plan (2016-2020) lists crystalline graphite in the strategic mineral catalog. Crystalline graphite is a strategic resource in China. To obtain high-grade and high recovery concentrate, graphite ores need to be broken, separated, and purified. Flotation is usually used for separation. Since flake graphite can only be obtained from ore, it cannot be synthesized manually and cannot be recovered once damaged, so the protection of flake graphite should be paid attention to in flotation. Besides the suitable flotation process, the choice of flotation agent is also very important. The addition of reagents in flotation can improve the hydrophobicity of graphite, improve the floatability of graphite and improve the separation efficiency of graphite from impurities. Graphite flotation agents can be divided into collector, foaming agent, and regulator. This paper analyzes the research and application status of flotation reagents in recent years and prospects the development of flotation reagents.

2. Collector
Natural graphite has certain floatability and can float out graphite concentrate when no collector is used. However, the flotation effect is not ideal and the recovery rate is not high. Adding a collector can greatly improve the recovery of graphite. The conventional collectors in flotation are kerosene, diesel oil, liquid paraffin, heavy oil, and other hydrocarbon oil, most of which are by-products of the petroleum industry. Hefuchao and others used kerosene as a collector in the experimental study of large flake graphite beneficiation, with a dosage of 176 g / T. after one rough grinding and coarse selection, two times of selection were carried out to obtain the high-quality graphite with a grade of 96.13%. In the discussion of using new drugs to improve the recovery of graphite, the liquid paraffin was used as the collector, and the main component of liquid paraffin was composed of high molecular alkanes. Because the dispersion of the direct paraffin was greater than that of branched alkanes with the same C atom number, it was easier to separate water between liquid paraffin and graphite than kerosene, The macroscopical performance of the liquid paraffin is better than kerosene in the collection and selectivity of graphite. The results show that the recovery and carbon content of liquid paraffin to graphite is 8.22% and 5.37% higher than kerosene respectively.
In order to improve the flotation efficiency and reduce the consumption of the reagents, scholars have been committed to the development of new collectors, such as DF, MB25, MF, mb125, GB, etc. In the paper on the synthesis of DF graphite flotation agent, Liang Guozhi introduced the method of preparing DF collectors. The industrial test was carried out. The flotation speed of the DF reagent is fast, non-toxic, and harmless, the odor is small, the dosage is small, and it has two functions of foaming and collecting. Wang Baoxian has developed a kind of nonpolar compound medicine MB-25, which has both collecting and bubbling properties. The thinner the attachment layer of the agent on the mineral surface, the wider the coverage, the better the improvement of hydrophobicity. Mb-25 can reduce the adsorption thickness, increase the adsorption surface and increase the hydrophobicity. The amount of MB-25 is only 1/4 of 2 # oil. Ma Chengcai and others have prepared a new collector MF by using cycloalkanes acid, cracked diesel, mixed fuel, and a small amount of diesel oil. It is proved that MF is better than the commercial flotation oil in terms of its collection and selectivity, less consumption, and lower price. Jinchan and others have prepared a compound agent containing aromatic, saturated, and unsaturated hydrocarbons by using mixed hydrocarbon. The agent is cheap and has better trapping and foaming properties than kerosene and 2 # oil.
In addition to the research of new agents, scholars also improve the effect of collectors by efficient treatment, such as shear flocculation, ultrasonic emulsification, adding a surfactant, etc. Shear flocculation is to add a certain amount of collector and surfactant to the pulp. The sheer force produced by high-speed stirring makes the particles gather, and increases the apparent diameter of particles. The flocculates are selected by the flotation method. The high-speed stirring shear changed the effect of collector and surfactant and ore particle, and improved the selectivity of flotation of target minerals, especially for improving the flotation of fine and fine particles. Ultrasonic wave is a kind of mechanical wave with high frequency, which is in the range of 20khz-10mhz[21]. The energy concentration of ultrasonic with large low-frequency amplitude can produce shock waves and micro jet, which can cause strong vibration of the medium. Shock wave and micro jet can break through the boundary layer limit, that is, it breaks through the oil-water interface, and makes the collector which is not soluble in water can be dissolved in water through the emulsification of ultrasonic waves. The research proves that the consumption of agents of the collector after ultrasonic emulsification is reduced, The selectivity of flotation is improved. The flotation effect of the collector can be improved by adding appropriate surfactant into the collector. The research of Fangping shows that the recovery of flake graphite is significantly improved by adding anionic surfactant in the flotation of graphite in neutral oil. The results show that zeta potential can be reduced, hydrophobicity of graphite surface can be improved and recovery rate of graphite flotation can be improved when the proper amount of active agent is added to the collector.
The application effect of high-efficiency treatment of conventional collectors, new collectors, and collectors in mineral flotation is introduced. The conventional collectors can meet the demand of production, but the dosage is large. The high efficiency of the new collector and collector in the flotation process shows that the amount of new collector is small, selectivity is good and the flotation effect is good. Especially, the new composite collector also has two functions of collecting and bubbling. It can simplify the dosing process and become one of the research hotspots of flotation reagents in the future.

3. Foaming agent
The foaming agent molecule is composed of polar and nonpolar groups, in which the polar group is hydrophilic and the nonpolar group is hydrophobic. The function of the foaming agent increases the mechanical strength of bubbles, prevents bubbles from merging, controls the floating speed of bubbles, and changes the distribution of bubbles. In the graphite flotation process, 2% oil, cresol acid, and camphor oil are often used as frother. Among them, 2 # oil is the most commonly used frother in mineral processing plants, and its main component is terpineol (c9h17oh), with a general content of 40-60%. Du Yingdong used kerosene as a collector, oil as a frother, and water glass as inhibitors in the flotation test of a flake graphite ore in Inner Mongolia. After one roughing, two scavengings, one-stage regrinding, and five cleanings, the graphite with the particle size of – 200 mesh and 85% can obtain concentrate with grade and recovery of 90.59% and 90.05% respectively.
In addition to 2-octanol, 4-octanol, MIBC, and so on. The raw material of 4-naphtha (1,1,3-triethoxybutane) is easy to obtain, low in price, high in purity, strong in foaming ability, and good in bubble stability. 4-naphtha was used as a foaming agent in the Shandong Nansha graphite concentrator, but 4-naphtha has a strong pungent smell and has not been widely used in actual production [27]. Fang Heping [28] compared the foaming effect of SEC octanol and terpineol oil (i.e. 2-oil) in the flotation experiment of flake graphite. The experimental results show that SEC octanol has a strong foaming ability and large bubble brittleness, and the recovery and flotation effect of graphite is significantly higher than that of terpineol oil (i.e. 2-oil). In the research of Wu Baijun [29], flotation tests were carried out with three common frothers, MIBC, 2# oil, and Ding Ji ether alcohol. It was found that when MIBC was used as a foaming agent, the mineralized foam had better stability and selectivity, and the recovery rate of graphite was higher than that of other agents.
Among the above foaming agents, 2-octanol, 4-octanol, and 2-octanol are by-products of the petroleum industry, while MIBC is a synthetic product. The source of foaming agents obtained from by-products of the petroleum industry is limited. In graphite flotation practice, the foaming performance and flotation effect of synthetic frother is better. Therefore, it is necessary to expand the sources of reagents and try to synthesize non-toxic and efficient foaming agents with other chemical products as raw materials.
4. Regulator
In graphite flotation, in order to improve the grade and recovery of graphite, a certain amount of regulator should be added according to the properties of pulp, the pH value and ionic composition of pulp should be adjusted, the interaction between collector and minerals should be adjusted, and the hydrophobicity of minerals should be inhibited or strengthened. It can be divided into pH regulator, inhibitor, dispersant, etc. The commonly used pH regulators are lime, NaCO3, and Na (OH) 2; The inhibitors are sodium silicate, sodium carboxymethyl cellulose, EDTA, tartaric acid, citric acid, and oxalic acid; Dispersants include sodium silicate, sodium hexametaphosphate, and sodium polyacrylate.
4.1 PH regulator
CAO is a kind of commonly used pH regulator. The lime reacts with water to form Ca (OH) 2, which is insoluble in water. During flotation, it can be directly added into the ball mill or stirred tank, or it can be mixed into lime milk and then added into the flotation machine. Lime is the cheapest pH regulator. When the graphite ore contains impurities such as pyrite, lime can improve the pH value of pulp and inhibit the flotation of pyrite. Therefore, lime can also be used as an inhibitor. NaCO3, also known as soda, is a kind of weak acid and strong alkali salt, which is easily soluble in water. Sodium carbonate solution is weak alkaline, with a pH value between 8-10. Zheng Renji et al. Used kerosene and oil as collector and frother respectively, lime as pH regulator, the lime dosage of 2500g / T, and pulp pH value of 9. After one roughing, five grindings, and six cleaning tests, graphite concentrate with a grade of 95.7% and recovery of 71.78% was obtained, It provides technical reference for concentrator production in Gansu Province. Linux used lime and NaCO3 as pH regulators respectively in the flotation experiment of Hegang graphite ore in Heilongjiang Province. The experimental results show that the effect of lime on fine flake graphite ore in Hegang is better than that of NaCO3.

4.2 Inhibitor
Water glass is often used as an inhibitor in graphite flotation. The composition of water glass is complex, which mainly contains silicate ions (hsio3 -) and silicate molecules (H2SiO3). These two components have strong hydration and hydrophilicity. They are easy to adsorb silicate minerals with the same acid radical and form a hydrophilic film on the surface of minerals to increase their hydrophilicity, so as to inhibit the floatability of minerals. Therefore, water glass can inhibit quartz, mica, feldspar, and silicate minerals, and is widely used as a gangue inhibitor. Sodium carboxymethylcellulose is also a commonly used inhibitor. The – oh and – COOH generated by itself form hydrogen bonds with anions on the gangue surface. Other molecules such as hydroxyl and carboxyl groups associate with water to increase the hydrophilicity of minerals and inhibit nontarget substances. Ren Ruichen et al. Selected sodium carboxymethyl cellulose and sodium carboxymethyl cellulose as inhibitors after analyzing the composition of graphite vein stone and explored the place and dosage of the reagent. The experimental results showed that when the inhibitor was added to the cleaning section, the recovery rate and grade of the concentrate were higher. The optimal dosage of sodium carboxymethyl cellulose and sodium carboxymethyl cellulose was 500 g / T, and the grade of the concentrate was 83.84%, The recovery was 76.05%. Li Huimei selected EDTA, tartaric acid, citric acid, and oxalic acid as four inhibitors in the study of flake graphite flotation inhibitors. In order to know which inhibitor has the best inhibition effect on quartz and other gangues, a series of tests were carried out. The results show that tartaric acid has the best effect and graphite has the highest carbon content when the dosage is the same.
4.3 Dispersant
The main function of dispersant is to change the surface properties of mineral particles and enhance the suspension and stability of pulp. In the study of yangjianwen, it is found that the graphite ore contains sericite and chlorite. Considering that both are silicate minerals, sodium hexametaphosphate is chosen as a dispersant. When appropriate dispersant is added, the recovery and grade of graphite are greatly improved. Liu Fengchun carried out the experiment of graphite shearing flocculation flotation. The results showed that the best effect was obtained by comparing the effect of three dispersants, namely, water glass, sodium hexametaphosphate, and acidified water glass, under the same stirring time and speed, the same amount of kerosene and dispersant.
The regulator is an indispensable agent in the selection of minerals with complex compositions. However, the selection of the regulator should take into account the nature of the mineral and non-objective minerals, and select the agents with good effect, less dosage, cheap and easy to obtain, and environmentally friendly, so as to improve the grade and recovery rate of the target minerals.
5. Conclusion and Prospect
There are many kinds of collectors, and the amount of commonly used collectors is large. The composite collector has two functions of collecting and foaming, with less amount and good collecting and selectivity. The effect of synthetic foaming agents is better than that of petroleum industry by-product foaming agents with limited sources. The regulator can ensure the flotation environment and reduce the production cost as much as possible. In the future, the research of graphite flotation reagents should focus on the following aspects
(1) The key point is to study the reagents with high efficiency, low cost, and low drug consumption. Most of the collectors and frother are by-products of the petroleum industry, and the source of reagents is limited. We can explore the use of other industrial by-products to replace petroleum products, or use other industrial by-products as raw materials to synthesize flotation reagents, In order to improve the flotation effect and reduce the flotation cost.
(2) The automation of flotation systems is the development trend in the future. The use of flotation reagents should simplify the medication process. The composite flotation reagents have the functions of collecting and foaming at the same time. The medication steps can be reduced in actual production, and the flotation system is easy to realize automatic control.
(3) The choice of medicament should pay attention to environmental protection. Whether it is collector, frother, or regulator, we should not only pay attention to the effect of flotation operation but also take into account the characteristics of flotation follow-up operation. We should choose reagents with less dosage, non-toxic, favorable for follow-up operation, fast degradation, and environment-friendly, so as to ensure the drug safety of the concentrator.