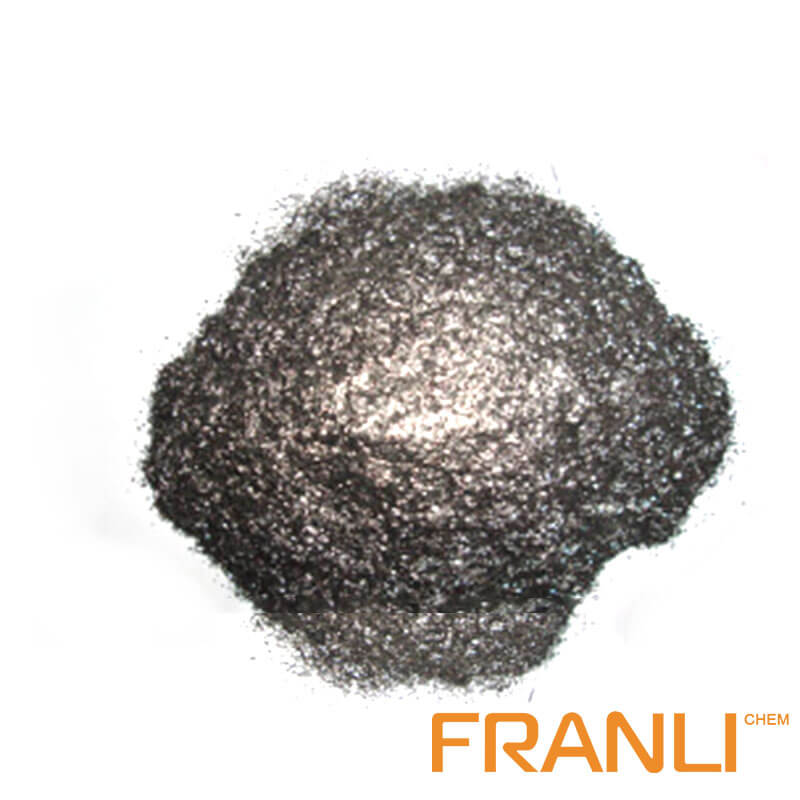
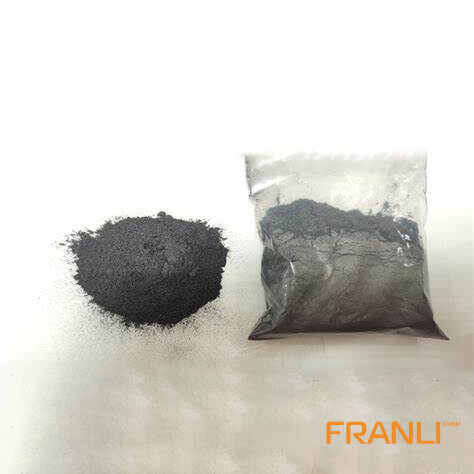
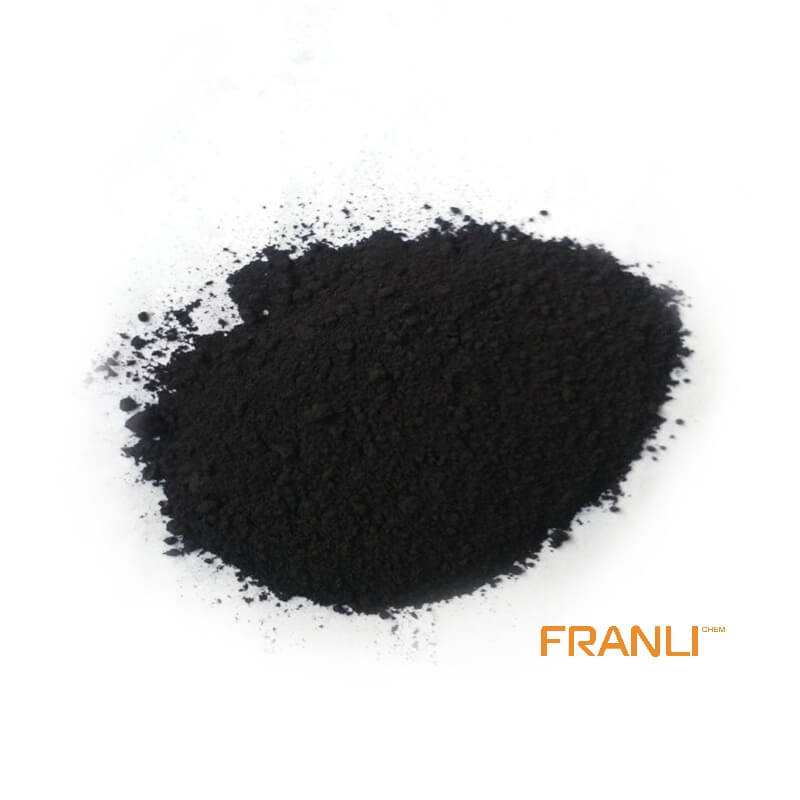
Flake Graphite
Size
0.01mm
Carbon Content
99%min
Package
25kg small bags into ton bags
Origin
China
Features
thermal shock resistance, lubricity, conductivity and plasticity…
Application
Lead battery plates positive and negative conductive agent, lithium batteries nickel hydrogen etc
Natural flake graphite has superior physical and chemical properties and is widely used in metallurgy, coatings and refractory industries. It is an important non-metallic raw material that is indispensable for today’s high-tech. Flake graphite is divided into large flake graphite and fine flake graphite according to the size of its scales. Usually, large flakes refer to +32 mesh, +50 mesh, +80 mesh, and +100 mesh flake graphite.
Request a quote
As a strategic non-metallic mineral resource, flake graphite has a unique structure, which makes it have good conductivity (resistivity 8 × 10−6 ~13 × 10−6 Ω· m) The physical and chemical properties such as strong plasticity, small friction coefficient (0.08-0.16), high-temperature resistance, stable chemical properties, and good flake floatability are the key raw materials for many industries. At the same time, flake graphite has the characteristics of wide use, the high added value of deep processing products, long industrial chain, etc. besides being widely used in traditional industries such as refractory, sealing, casting, and conductive materials, it has a great application prospect in new energy, new generation electronic information technology, new energy vehicles, high-end assembly, and manufacturing industries, and is known as “industrial black gold”. China has rich graphite resources but has not yet become a powerful country of graphite resources.
This paper discusses the flake graphite separation process, purification method, preparation of deep processing products, and its application in the emerging strategic industry. The comprehensive utilization progress of graphite resources is systematically introduced, including the graphite interlayer compounds Spherical graphite and graphene are three important graphite deep processing products. Finally, based on the development trend of the graphite industry, the development direction of strengthening the development and utilization of graphite resources is given.

Graphite is a multi bond crystal with a layered crystal structure. The carbon atoms in the layer and the surrounding 3 carbon atoms form covalent bonds through the hybridization of SP 2, which forms a ring-like honeycomb structure; The interlayer is connected by intermolecular force (van der Waals force), and the binding force is weak; The remaining p-electrons of each carbon atom in the layer form a large range of dissociation similar to the free electron model of metal bond π Bond, therefore, there are covalent bonds, molecular bonds and metal bonds in the crystal structure of graphite. The unique structure determines the physical and chemical properties of graphite.
Because of the chemical bond in its structure, graphite has strong thermal conductivity, heat resistance, and chemical stability; The excellent conductivity of graphite is due to its large range π Key; The special layered structure is easy to slide between the layers under the action of external force, which makes graphite have good lubricity; At the same time, graphite has good flake floatability and its contact angle θ 85 in general °~ eighty-six °, The graphite with the fixed carbon content of more than 90% can be obtained by flotation separation. Graphite is an indispensable non-metallic material for the development of high and new technology in the world. It has the characteristics of non-duplication and is irreplaceable. Many developed countries have listed graphite as their strategic mineral resource for protection. Graphite has always been an important non-metallic mineral resource in China. It was written by graphite in Shang Dynasty more than 3000 years ago. To keep the national economy developing and efficiently exploit and utilize graphite resources, China also listed crystalline graphite as strategic mineral resources for protection.
Flake graphite is often accompanied by various impurities, which are difficult to be directly used. To meet the requirements of industrial production, it is necessary to enrich and purify flake graphite, and the higher the purity of graphite, the higher its value. At present, there are three purification methods for graphite: flotation, chemistry, and high temperature, among which chemical methods include alkali melting acid leaching, hydrofluoric acid, acid mixing, and chlorination roasting.
Flotation method
Flake graphite has good floatability. Flotation is usually used as the first step in the separation and purification of flake graphite. At present, all flake graphite in industrial production is sorted by flotation. The beneficiation technology adopts multi-stage grinding and multi-stage separation process. On this basis, more effective and reasonable equipment and process are studied for different ores, to maximize the fixed carbon content and protect the graphite scale structure.
At present, the experiments of crushing and separating the crystalline graphite ore in Heilongjiang Province have been carried out. The concentrate with the fixed carbon content of 94.50% is obtained, and the distribution rate of large scale with the particle size of +0.147mm is 31.24%. The high carbon concentrate with a fixed carbon content of 94.52% was obtained by the experiments of lamination crushing and separation of graphite in Inner Mongolia. Both proved that replacing the fine crushing and coarse grinding equipment in traditional technology with a high-pressure roller mill can better protect the crystal structure of flake graphite in the rough grinding stage, improve crushing efficiency, shorten process flow, and reduce process flow energy consumption.
At the same time, it is verified that the separation process of regrinding and re separation is made by using the characteristics of different products, which can protect the large scale in graphite more effectively and improve the flotation efficiency. Ass the first step of graphite purification, the flotation method has the advantages of the mature process, simple equipment, less energy consumption, and low production cost, which makes it have obvious cost advantages. However, the flotation method has limited purification capacity for graphite, which can not remove the inclusions partially immersed in graphite flakes. The fixed carbon content of the purified graphite is difficult to exceed 95%. Therefore, to obtain high purity graphite, the flotation method has the advantages of low energy consumption and low production cost. Chemical and high-temperature methods must be adopted to further purify graphite.

Chemical method
Chemical purification is based on the stability of graphite chemical properties. Under certain conditions, the flotation graphite concentrate is treated by strong acid, strong alkali, or other compounds. The impurities in the concentrate are dissolved, impurities are removed and graphite is purified. The chemical method mainly includes the following:
Alkali melting acid leaching
Alkali melting acid leaching is to react with NaOH at a high temperature above 500 ℃ by using impurities in graphite, and some impurities (silicate, etc.) are produced to dissolve in water, which is removed by water leaching and washing; Another part of impurities (Al2O3, Fe2O3, MgO, Cao, and other metal oxides) are formed after alkali melting to form water-insoluble precipitates, which are neutralized by hydrochloric acid to form chloride soluble in water, which is removed by washing with clean water. The process flow of the alkali melt acid leaching method for the purification of graphite is shown in Figure 5. This process is widely used in the industrial production of graphite purification in China. With the continuous development of the graphite purification industry, more reasonable and effective equipment and processes have also appeared.
When Liu Yuhai et al. [4] used alkali melting and acid leaching to purify fine flake graphite in a place in Heilongjiang Province, by discussing the appropriate process parameters, the fixed carbon content of graphite was increased from 95.89% to 99.94% by alkali melting roasting water leaching acid leaching process. Liu Changqing et al. [5] took the raw material of cryptocrystalline graphite with a fine particle size as the research object, through studying the purification effect of cryptocrystalline graphite under different alkali melting conditions and acid leaching conditions, finally increased the raw material with the fixed carbon content of 82.67% too high purity graphite with the fixed carbon content of 93.42%, which proved that alkali melting acid leaching method can effectively improve the grade of cryptocrystalline graphite. Alkali melt acid leaching is the most widely used method in the graphite purification industry in China. It has the characteristics of a less one-time investment and high carbon content of graphite. The fixed carbon content of graphite purified by alkali melt acid leaching can reach more than 99%, but it is difficult to get 99.9% fixed carbon content. At the same time, the method uses a lot of acid-base solution, which is easy to corrode the equipment and causes serious wastewater pollution.
Hydrofluoric acid method
The Hydrofluoric acid method is to use impurities in graphite to react with hydrofluoric acid, and some impurities (Na2O, K2O, Al2O3, etc.) form water-soluble compounds, which are removed with the solution; Another part of impurities (CaSiO3, Cao, MgO, Fe2O3, etc.) react with HF to form water-insoluble compounds. By adding H2SiF6 to form water-soluble fluorosilicates, the impurity solution is separated from solid-liquid graphite by washing with clean water to purify graphite. The process flow of graphite purification by a hydrofluoric acid method is shown in Fig. 6. This method has the advantages of a simple process, high impurity removal efficiency, and little effect of HF acid on the performance of high-purity graphite. Graphite products with high carbon content and excellent performance can be obtained. However, hydrofluoric acid or HF gas is highly toxic, corrosive to the equipment, and seriously pollutes the environment, limitings its application. There are not many enterprises using this method in China.
Robert Lloyd et al. [6] used HF + H2SiF6 fluoro acid solution to purify graphite so that the metal oxide in the solution became fluorosilicate and fluoride soluble in the solution, and dried the washed graphite at 70 ~ 140 ℃ (preferably 130 ℃), The treated graphite was heated to 250 ~ 400 ℃ (preferably 300 ℃) to remove HF and SiF4 from graphite, and good experimental results were obtained.

Mixed acid process
The hydrofluoric acid method has great pollution to the environment. To reduce the use of hydrofluoric acid in the process of graphite purification, it is often used together with other acids to form a mixed acid system. The mixed acid system’s purifying graphite is called the mixed acid method, and its basic principle is similar to the hydrofluoric acid method. In industrial production, HF / HCl, HF / H2SO4, HF / HCl / H2SO4, and other mixed acid systems are mainly used. In the production, HF, H2SO4, and HCl are successively added into the graphite. After each acid is added, it should be fully stirred to make it mix evenly and react completely.
After the reaction, wash it repeatedly with industrial clean water until it is neutral; Then clean with pure water 2 ~ 5 times; Finally, dehydrate, dry, and package. The mixed acid method can be used to produce high purity graphite with a carbon content of more than 99.9%. Compared with a hydrofluoric acid method, the mixed acid method reduces the consumption of HF, reduces environmental pollution, and saves the production cost. The system of purifying graphite by HF / H2SO4 mixed acid method was introduced into thermal activation. When the acid solid ratio was 3:1700 ℃ and activated for 1h, the fixed carbon content of raw material was increased from 86.42% to 99.98%, and the amount of hydrofluoric acid was reduced by 2 / 3. Wang Guangming [8] used HF / HCl / H2SO4 mixed acid method to treat graphite with the fixed carbon content of 98% ~ 99% in the industrial production process, and prepared high-purity graphite with the fixed carbon content of 99.96% under the conditions of HF, HCl and H2SO4 dosage of 0.5 ~ 0.8 kg, 0.4 ~ 0.9 kg and 0.4 ~ 0.7 kg respectively, and reaction at room temperature for 24 h.
Chlorination roasting
The chlorination roasting method is to add a certain amount of reducing agent (such as coke) into the graphite, at a certain temperature (above 1000 ℃) and under specific atmosphere conditions, put in chlorine gas for chlorination roasting, so that the valuable metal impurities in the graphite can be transformed into chlorides or complexes with low melting boiling point and escape, to achieve the purpose of purifying graphite.
The method has the advantages of low energy consumption and high purification efficiency. But at the same time, the equipment is complex, the process stability is not good, the chlorine gas used is toxic, the environmental pollution is serious, the fixed carbon content of the product is limited (about 98%), and many other adverse factors limit the application and promotion of the chlorination roasting process. The method still needs further improvement and improvement. Fig. 7 Schematic diagram of the principal device of chlorination roasting: Li Jiye et al. [9] when purifying nature flake graphite, the carbon content of graphite was increased from 86.09% to 98.76% by chlorination roasting method under the conditions of 1200 ℃ and 2.5 h reaction time. Based on the laboratory research, Xia Yunkai (10) purified graphite by chlorination roasting method. The carbon content of raw materials was purified from 88.75% to 99.54% under the condition of reaction temperature 1100 ℃, reaction time 2.5 h, and Cl2 pressure of 0.05 MPa.
High-temperature method
According to the different heating sources, the high-temperature method can be divided into six methods: resistance heating purification, induction heating purification, plasma heating purification, RF heating purification, light energy heating purification, and microwave heating purification. The basic principle is to purify graphite by separating graphite from impurities under high-temperature conditions, Finally, the high-purity graphite with a carbon content of 99.99% can be obtained. Zhang Xiangjun et al. Obtained high purity graphite with fixed carbon content higher than 99.99% after a preliminary discussion on experimental conditions when the carbon content reached 99% or more by high- temperature method. If the heating process conditions were further improved and the quality of the crucible was improved, the content of graphite carbon could be increased to over 99.995%.
In industrial application, jixihao new energy materials Co., Ltd. purified graphite by a high-temperature method in 2015 and heated it to 3100 ℃ by using Acheson electric furnace, the largest monomer in China, to obtain high-purity graphite with a carbon content of 99.99952%, reaching the international advanced level. Compared with other purification methods, the high-temperature method can obtain high purity graphite with carbon content higher than 99.99%, even more than 99.995%. However, the method also requires high requirements for raw material purity, material fineness and equipment technology, high energy consumption, and huge investment. Therefore, the current application field of this method is limited, It is mainly used in aerospace, national defense, and nuclear industry, which requires high graphite quality.