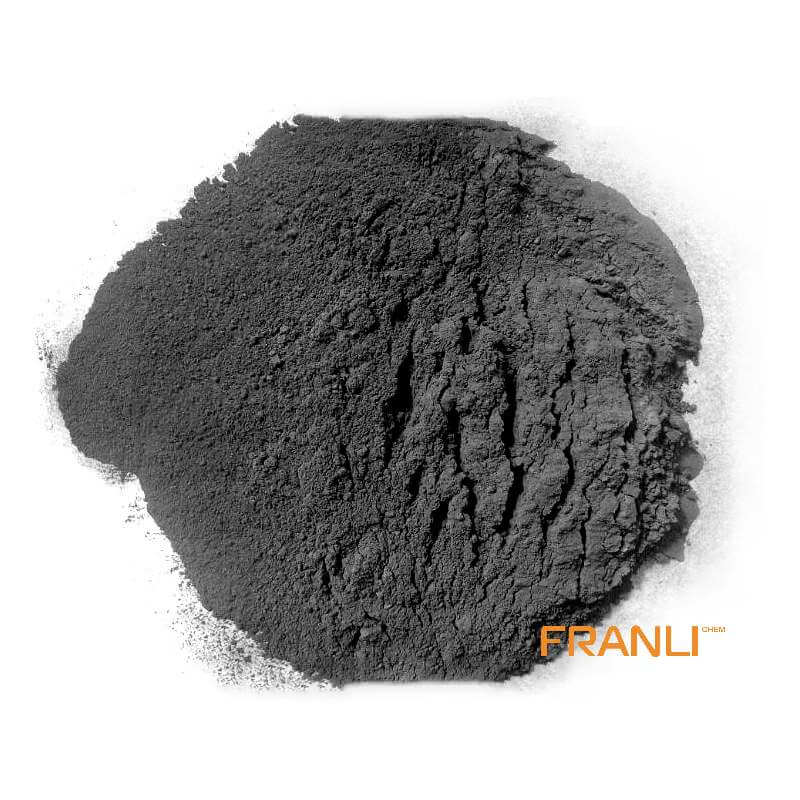
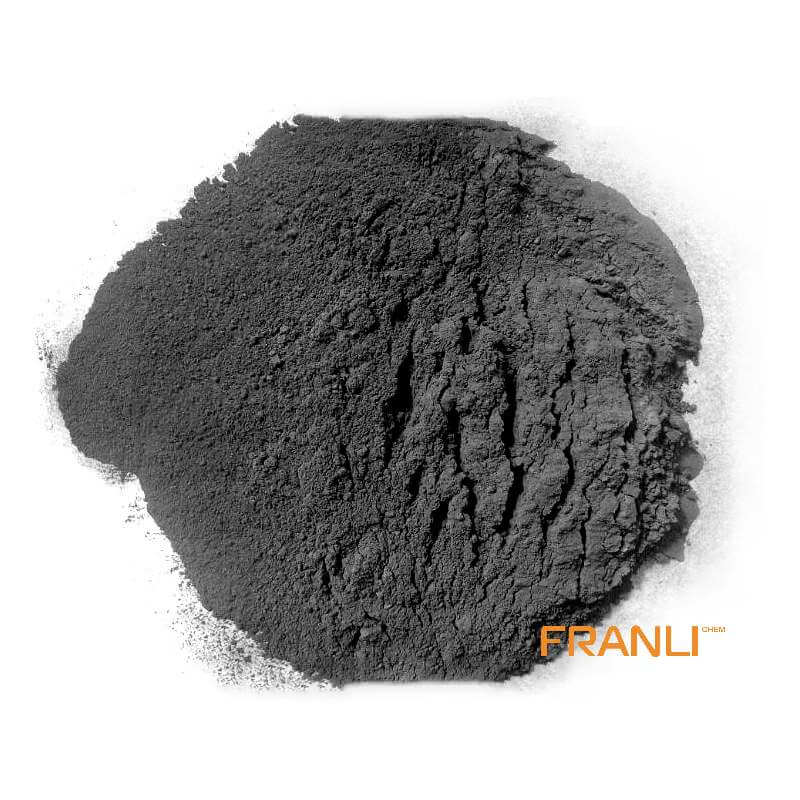
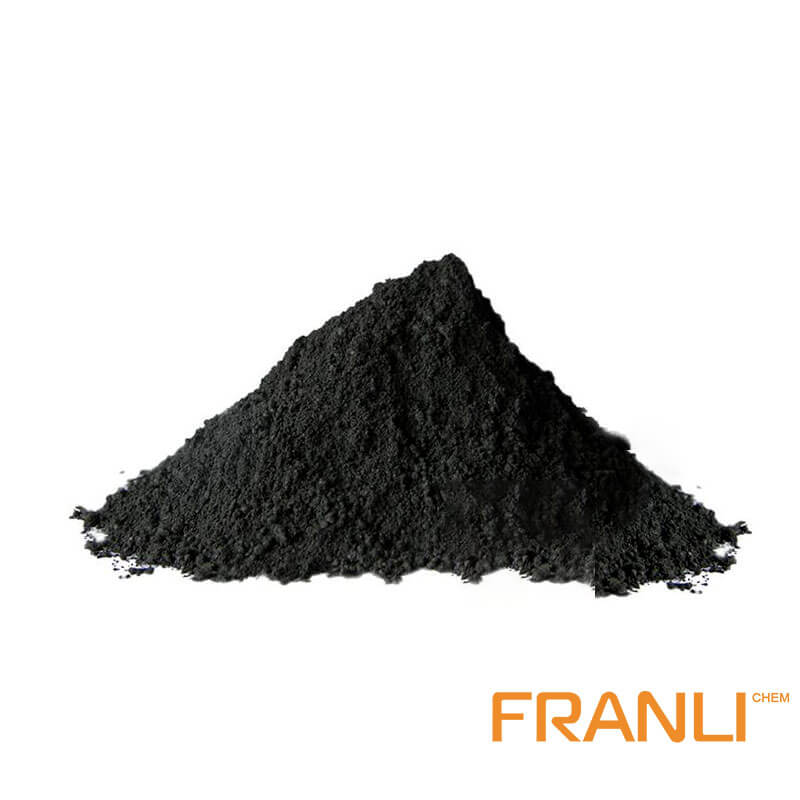
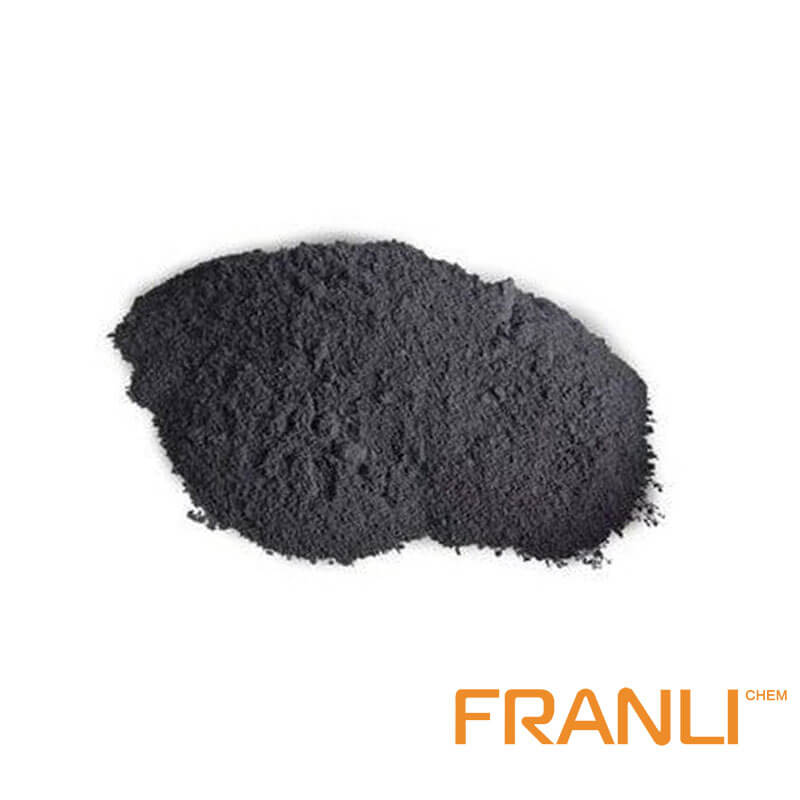
Artificial Graphite
Size
0.01mm or 0.07mm,etc
Package
25 kg small bags into ton bags or ton bags
Features
Good wear resistance, corrosion resistance, good thermal conductivity, etc.
Application
Can be used in making heat exchanger, reaction tank, absorption tower, etc.
There are many kinds of artificial graphite and different production processes. In a broad sense, all graphite materials obtained by carbonization of organic matters and treated by high temperature after being treated with graphite can be collectively referred to as artificial graphite.In the narrow sense, artificial graphite usually refers to the massive solid materials prepared by batching.
Request a quote
Artificial graphite is an industrial application as a sealing material. Graphite blocks are made from artificial graphite, which is produced by heating carbonaceous materials at high temperatures and pressures. Graphite has a low coefficient of friction, which improves its sealing capacity. This makes the material highly heat, corrosion and abrasion resistant, making it ideal for use in harsh environments.


The sealing ability of graphite blocks in cement rotary kilns is related to the performance of artificial graphite. These include heat, corrosion and wear resistance, as well as low coefficient of friction and thermal expansion. As the industrial sector continues to grow, the use of graphite blocks is likely to become more common. Franli graphite factory can provide high-quality graphite for manufacturing graphite blocks, you can contact us if you need it.