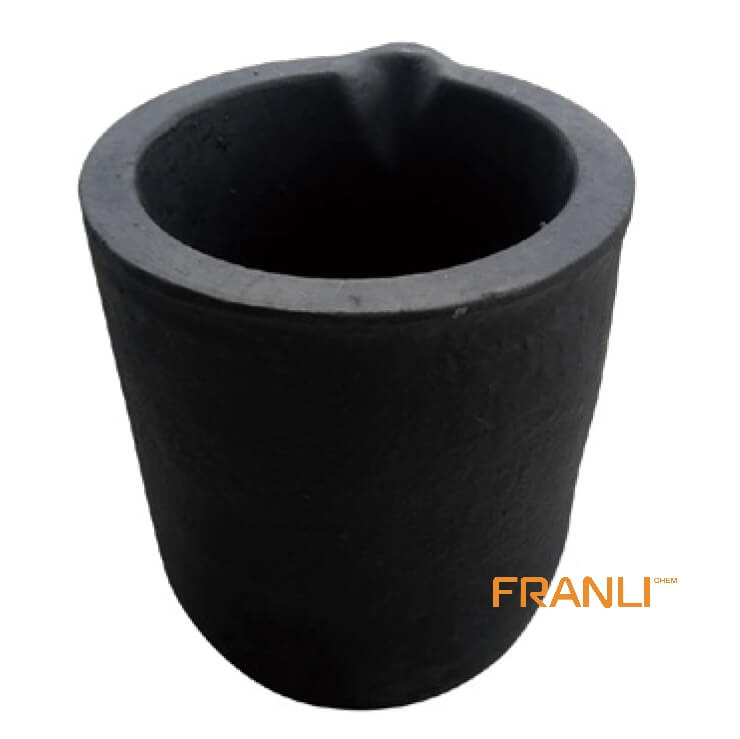
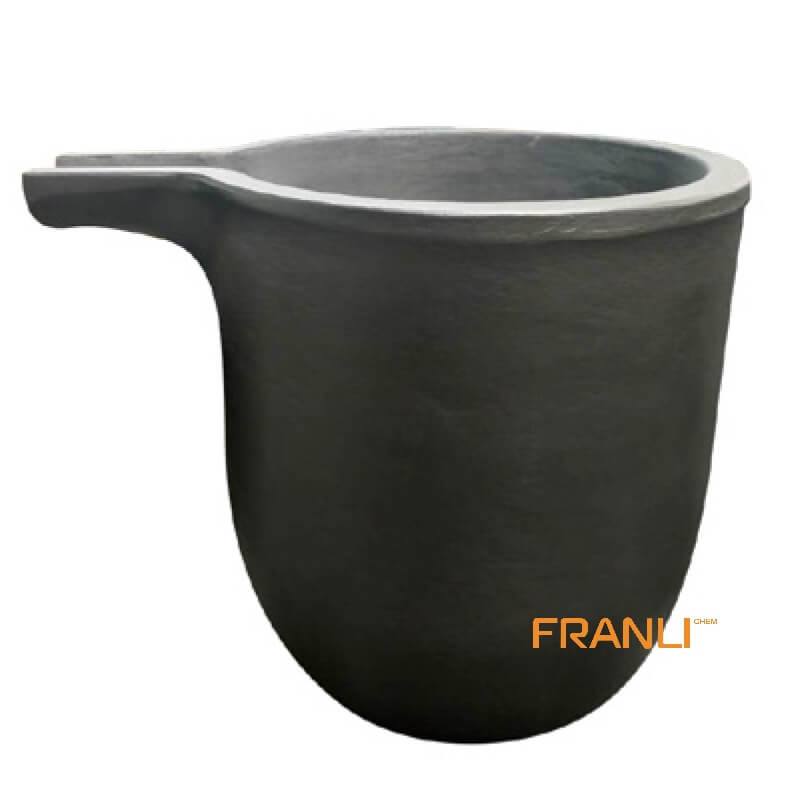
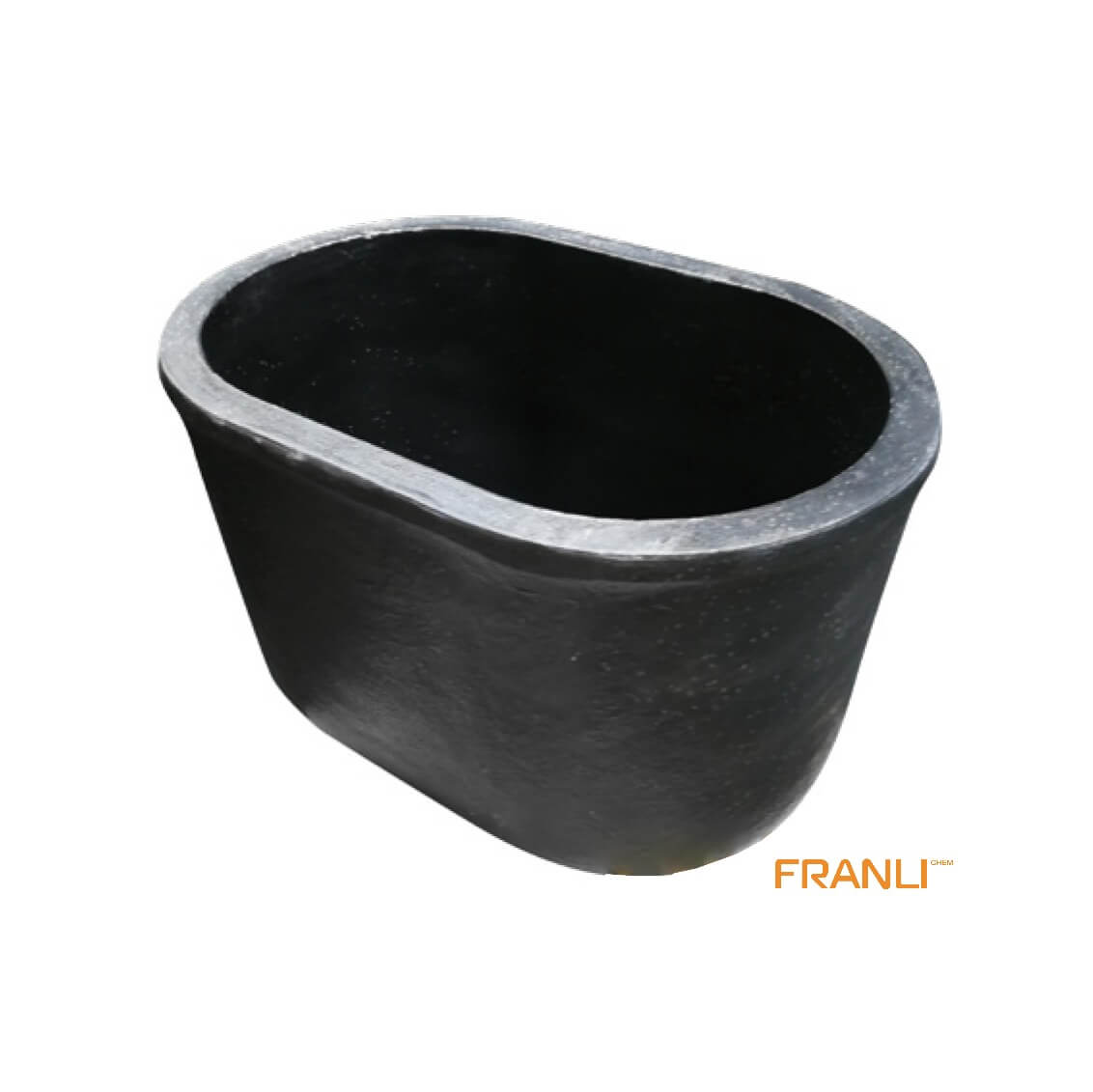
Graphite Crucible
Size
Different size is available, can be customized
Carbon Content
SiC graphite crucible, Spouted crucible, Inductor crucible, Elliptical crucible(U-shaped Crucible)
Material
Graphite and Silicon carbide
Working temperature
400-1600℃
Melting Metal
Aluminum, Copper, Brass, Bronze, Silver, Tin, Zinc, etc
Features
High density, high strength, dense uniform and defect-free.
Package
Wooden box
Graphite crucible is made of natural flake graphite as the main raw material and plastic refractory clay or carbon as binder. It has the characteristics of high temperature resistance, strong thermal conductivity, good corrosion resistance and long service life. It has strong corrosion resistance on acidic and alkaline solutions, has excellent chemical stability, and does not participate in any chemical reactions during the smelting process. The inner wall of the graphite crucible is smooth, and the melted metal liquid is not easy to leak and adhere to the inner wall of the crucible, so that the metal liquid has good fluidity and is suitable for various mold casting.
Request a quote
Graphite crucibles are an important tool used in metallurgy and materials processing to melt and hold metals and other materials at high temperatures. The ability of graphite to withstand extreme heat makes it well-suited for applications involving melting, casting, and heat treatment. There are several different types of graphite crucibles that are designed for different purposes and temperature ranges.
One of the most common types of graphite crucible is the isotropic graphite crucible. Isotropic graphite refers to graphite that has been manufactured through a process that gives it an even grain structure and properties that are consistent in all directions. Isotropic graphite crucibles can withstand temperatures up to around 3000°C (5432°F). They are suitable for general melting and holding of metals like aluminum, copper, zinc, tin, and lead. Isotropic graphite crucibles are relatively inexpensive and easy to machine, making them a good choice for basic melting and casting applications that do not require the highest temperatures. However, their thermal shock resistance is not as high as some other crucible types.
For applications requiring higher temperatures or better thermal shock resistance, anisotropic graphite crucibles are commonly used. Anisotropic graphite has a grain structure that runs parallel to the surface of the crucible, giving it different properties along different axes. It can withstand temperatures up to around 3300°C (5972°F). The directional grain structure provides anisotropic graphite crucibles with better thermal shock resistance compared to isotropic graphite. This makes them well-suited for melting and holding refractory metals like titanium, niobium, and tantalum that have high melting points. Anisotropic graphite crucibles are also used for melting superalloys and other advanced metal alloys. However, they are more expensive than isotropic graphite crucibles due to the specialized manufacturing process required.
Isostatic graphite crucibles represent an intermediate option between isotropic and anisotropic graphite. They are manufactured through a process that orients the graphite grains at an angle between 0 and 90 degrees to the surface. This provides better thermal shock resistance than isotropic graphite while maintaining more consistent properties in all directions compared to anisotropic graphite. Isostatic graphite crucibles can operate at temperatures up to around 3100°C (5608°F). They offer improved thermal shock resistance over isotropic graphite at a lower cost than fully anisotropic graphite. Common applications include melting specialty steels, superalloys, and reactive metals like titanium.
For the highest temperature applications, semi-graphitic crucibles are often used. Semi-graphitic crucibles contain a graphite-carbon composite microstructure rather than pure graphite. This allows them to withstand temperatures as high as 3600°C (6512°F), exceeding the capabilities of even anisotropic graphite crucibles. However, their thermal shock resistance is lower. Semi-graphitic crucibles are well-suited for processes like plasma melting where extremely high temperatures are required. Examples include remelting refractory metal scraps and melting advanced ceramics. Due to their specialized microstructure, semi-graphitic crucibles require even more advanced manufacturing techniques and are the most expensive crucible type.
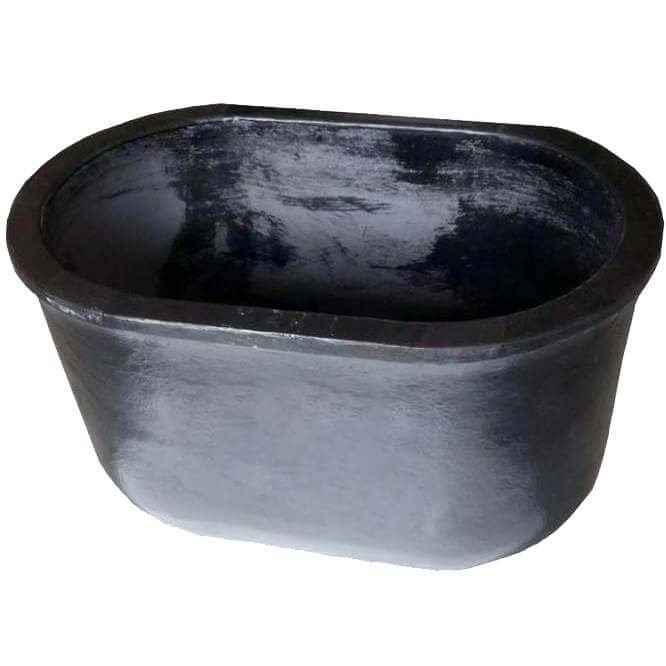
In addition to differences in their graphite microstructure, crucibles can also be classified based on their geometry and construction. Some common crucible geometries include:
– Cylindrical crucibles – The classic cylindrical shape is suitable for general melting and holding applications. It provides a large internal volume.
– Conical crucibles – Conical crucibles taper inward from the bottom to facilitate pouring. They are commonly used for investment casting of metals and alloys.
– Rectangular/square crucibles – Rectangular or square crucibles provide flat surfaces that are useful when melting or casting materials into ingots or slabs.
– Nozzle crucibles – Nozzle crucibles have a pouring spout or nozzle attached to carefully direct and control the flow of molten material when pouring.
In terms of construction, graphite crucibles are either machined from a solid block of graphite material or constructed by stacking and bonding together graphite or graphite composite plates or rings. Machined crucibles provide the highest density and strength but are more expensive to produce. Plate-type or ring-type assembled crucibles can be made in larger sizes at lower cost for some applications. Reinforced graphite crucibles may also contain a rigid metal or ceramic inner core material to provide added strength for handling and pouring molten metals at very high temperatures.
The selection of the proper graphite crucible type depends on factors like the material to be melted, required process temperature, thermal cycling conditions, crucible size requirements, and budget. Working closely with graphite crucible suppliers is important to determine the optimal crucible properties for each specific application. Proper crucible selection and handling techniques are also critical to maximize crucible lifetime and process efficiency. With the various graphite crucible options available, there is usually a type that can meet the needs of nearly any high-temperature melting or casting application.
Isotropic, anisotropic, isostatic, and semi-graphitic graphite crucibles each have different temperature capabilities and properties related to their graphite microstructure. Additional variations include geometry, construction method, and reinforcement. Choosing the right crucible type involves consideration of factors like the material to be processed, temperatures, thermal cycling conditions, size needs, and cost. With their ability to withstand extreme heat, graphite crucibles remain an indispensable tool for high-temperature melting, holding, and casting applications across many industries.