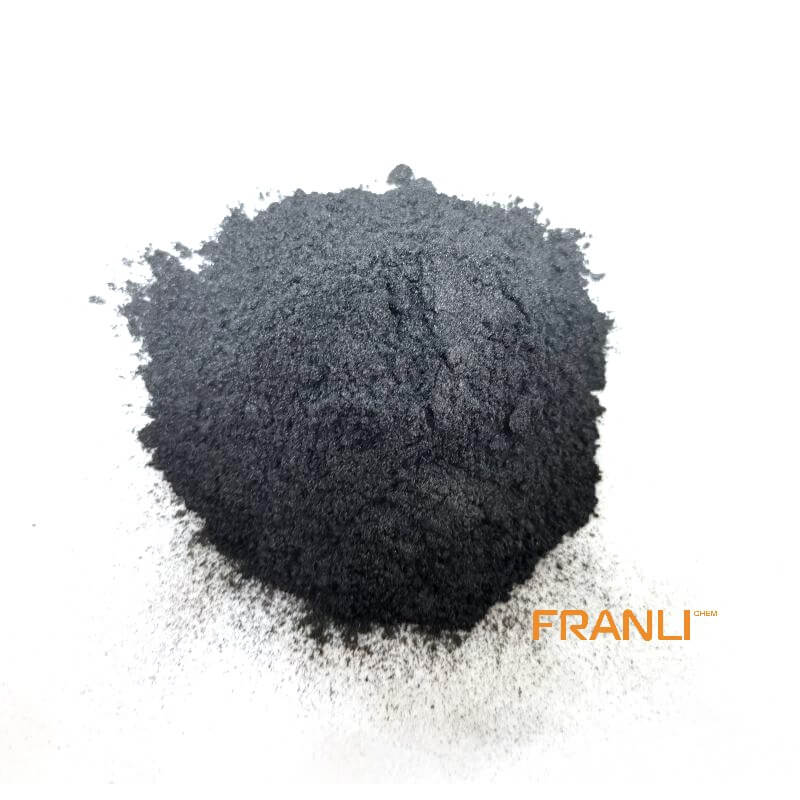
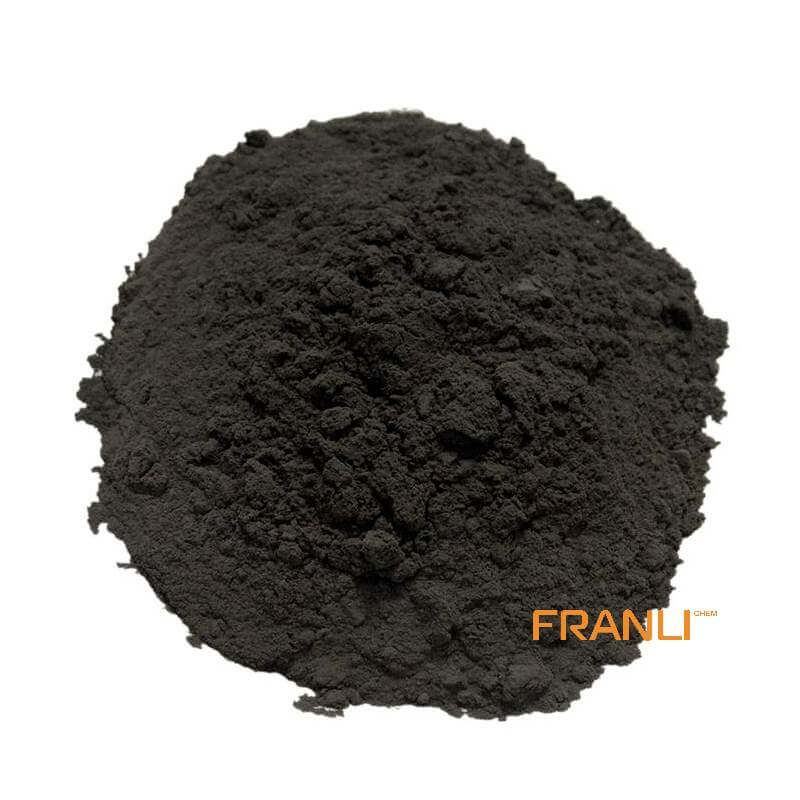
Amorphous Graphite
Size
45μm, 75μm, 150μm, etc
Package
25kg small bags into ton bags or ton bags
Origin
China
Features
Under high temperature conditions, it has special oxidation resistance, etc
Application
Casting coatings, oil field drilling, battery carbon rods, steel, casting materials, refractories, dyes
It is an aggregate of amorphous graphite. The crystal form can be seen only under the electron microscope. Amorphous graphite ore is gray black and steel gray, generally dull, with dense massive, earthy, layered, and lamellar structures. This kind of graphite lacks luster, its lubricity is lower than that of flake graphite, and its selectivity is poor. However, the grade is high, the carbon content is generally 60% ~ 80%, a few are up to more than 90%, the ash content is 15% ~ 22%, the volatile content is 1% ~ 2%, and the moisture content is 2% ~ 7%.
Request a quoteAbstract: natural amorphous graphite crystals are tiny, and each graphite particle is disorderly stacked by many microcrystalline, showing isotropy, which has important potential application value in the field of anode materials for lithium-ion power batteries. In recent years, the strategic position of natural amorphous graphite is increasing, and it has become a hot spot in scientific research, industry, and finance. In this paper, the processing and application status of natural amorphous graphite were summarized, and its development trend has prospected.
The natural graphite is mainly divided into flake graphite and amorphous graphite according to the crystal morphology. Among them, amorphous graphite is very small, and each particle is disorderly stacked by many microcrystalline, showing isotropy to a certain extent. It has important potential application value in high-tech fields such as anode materials for lithium-ion batteries (especially power batteries).
China is rich in natural amorphous graphite resources, and its reserves, output, and export volume rank first in the world, with high grade and good quality, which directly affects the international price of amorphous graphite. However, for a long time, there is little research on amorphous graphite at home and abroad, which leads to the backward industrial technology level. The main products are raw ore and primary processing products, and the added value of products is low, resulting in the waste of a large number of valuable natural amorphous graphite resources. In recent years, with the attention of national management departments and related industries, the strategic position of natural amorphous graphite is increasing, and it has become the frontier of scientific and technological research, and the investment hotspot of industry and finance.
In this paper, the processing and application status of natural amorphous graphite were summarized, and its development trend has prospected.

1. Status of processing technology
The processing technology of natural amorphous graphite can be divided into two types: initial processing and deep processing.
1.1 Current status of initial processing technology
The natural amorphous graphite has a high grade, and the fixed carbon content is generally 50% – 80%, or even more than 90%, so it can be used only after simple processing. At present, the processing of amorphous graphite is mainly composed of grinding powder, sieve particles, and ball pressing. Grinding powder is to crush the amorphous graphite into graphite powder through a certain number of meshes by Raymond machine, mainly used for casting demoulding, grounding resistance reduction, and so on. The sieve particles are used as carbon additives in steel making and casting. The ball pressing is to mix the amorphous graphite raw ore with starch, caustic soda, and water in a certain proportion and mix it evenly, and then process the near-spherical product with certain strength through extrusion molding and drying process. The products have the largest output, mainly used as heating agents, protection slag, and carbon additive for steel making.
1.2 Current situation of deep processing technology
The deep processing of natural amorphous graphite mainly focuses on Purification and particle shaping modification.
1.2.1 Purification technology
1.2.1.1 Flotation purification technology
Graphite has good natural hydrophobicity. In the slurry system, the gas-liquid interface can be gathered by bubble buoyancy, to separate from impurities minerals and achieve the purpose of purification. However, the natural amorphous graphite has a small crystal, and impurities are dispersed and embedded in graphite particles, which makes it float poorly. However, through multi-stage grinding, the graphite crystal can be separated gradually, and the floatability is better. Therefore, the flotation of amorphous graphite generally adopts the process of multi-stage grinding, multiple separations, and coarse concentrate regrinding and re-dressing. Many units and researchers have studied the flotation purification technology of natural amorphous graphite
The existing research results show that the pure flotation method has certain limitations for the purification effect of amorphous graphite, it is difficult to obtain high purity products, and it is not economical, so it can only be used as the first step of amorphous graphite purification. At present, only China Building Materials Group Nanfang graphite Co., Ltd. has set up an amorphous graphite flotation purification production line with an annual capacity of about 100000 tons, which purifies 65% – 70% of the fixed carbon amorphous graphite to about 80% of the fixed carbon.
1.2.1.2 Acid-base purification technology
The acid-base method is to make use of the acid-base resistance of graphite, and the main impurities (silicate, etc.) in graphite react with sodium hydroxide above 600 ℃ to form water-soluble products. Other impurities (such as iron oxide, etc.) are neutralized with hydrochloric acid after alkali fusion to form water-soluble ferric chloride, etc., which is removed by washing. This method is not only the main method of chemical purification but also a mature technology at present.

Liu Huaiqing et al. Studied the purification process of amorphous graphite by acid-base method, which can purify the amorphous graphite to more than 96% of fixed carbon content. The amorphous graphite with 85.60% fixed carbon was purified to 97.86% by an acid-base method. The amorphous graphite with 62.43% fixed carbon was purified to 98.60% by the acid-base method. Li Xiaobo et al. Purified amorphous graphite with the fixed carbon content of 79.82% to 97.65% by an acid-base method. Under the optimum conditions, the amorphous graphite with a fixed carbon content of 85% and particle size of 0-0.048 mm was purified to 98.79%. Liu Changqing et al. Purified amorphous graphite with the fixed carbon content of 82.67% to 93.42% by the acid-base method. The amorphous graphite with a fixed carbon content of 86.0% was purified to 99.898% by the acid-base method. Jiang Yingping et al. Purified amorphous graphite from 80.04% of fixed carbon to more than 96% by pressure alkali leaching atmospheric pressure acid leaching process.
The acid-base process has strong adaptability, but it has some problems, such as large water consumption, low efficiency, large equipment investment, high production cost, and serious environmental pollution. Compared with the flotation method, the purity of the product obtained by the acid-base method is higher, up to 99%. It should be noted that the formation of silicic acid should be prevented during acid leaching after alkali fusion, because sodium metasilicate produced by sodium silicate in acid solution will be gradually condensed to form silica sol or silica gel when placed or changed, so it is difficult to remove it. Therefore, the acid-base method is more suitable for the treatment of graphite with less mica. The alkali acid method has been applied to the further purification of flake graphite flotation concentrate in Shandong, Heilongjiang, and other parts of China. At present, there is no industrial production line to purify amorphous graphite by this method.
1.2.1.3 Mixed acid purification technology
According to the characteristics of acid corrosion resistance of graphite, impurities in graphite can react with hydrofluoric acid or soluble fluoride to form water-soluble compounds or volatiles, amorphous graphite can be soaked in a certain concentration of mixed acid containing hydrofluoric acid or acid solution of soluble fluoride such as ammonium fluoride, and then washed with water to remove impurities, and then dehydrated and dried to obtain high purity products.
Kuang Jiacai et al. Used an ammonium fluoride hydrochloric acid system to purify the amorphous graphite. Under the optimum conditions, the fixed carbon content increased from 83.08% to 99.47%. Hongquan et al. Used hf-HCL mixed acid to purify amorphous graphite, and the fixed carbon content before and after purification was 87.8% and 99.1% respectively. Jiang Fang et al. Used HCl HF mixed acid to purify the amorphous graphite, and the fixed carbon content increased to 99.36%. Xie Wei et al. Used the mixed system of hydrochloric acid and sodium fluoride to purify the natural amorphous graphite, and the fixed carbon content increased from 83.08% to 98.37%. Duan Jiaqi et al. Purified amorphous graphite by ultrasonic mixed acid method and the fixed carbon content increased from 81.54% to 99.97%.
The advantages of the mixed acid method are high purification efficiency, high product purity, and low energy consumption. However, the hydrofluoric acid in the mixed acid is volatile, highly toxic, and highly corrosive. The production process must have strict safety protection and a wastewater treatment system. The equipment is demanding and the cost is high, so it is not suitable for large-scale industrial production. At present, there is no industrial production line to purify amorphous graphite by this method.
1.2.1.4 Purification technology by high-temperature method
There are two kinds of high-temperature purification technologies, chlorination roasting, and pure high-temperature method.
The principle of chlorination roasting is to make use of the high boiling point of SiO2, Al2O3, Fe2O3, Cao, and other impurities in graphite, while the melting boiling point of chloride is relatively low. Chlorine gas is injected into the chloride at a certain high temperature and atmosphere so that the impurities can generate chloride and escape at a low temperature, to achieve the purpose of purification of graphite. The factors influencing the purification effect are reaction temperature, reaction time, reductant dosage, Cl2 pressure and flow rate, grade, and particle size composition of graphite raw materials.

The chlorination roasting method has the advantages of high purification efficiency, high purity, and high recovery rate, but the process is not controllable, and it has the disadvantages of high purification cost, serious equipment corrosion, and serious environmental pollution, which limits the application of the method. At present, the chlorination roasting method is still in the exploration and development stage, and there is no industrial production line for purifying amorphous graphite by this method.
The pure high-temperature method is to uses the high-temperature resistance of graphite and the difference of boiling point between graphite and impurities. Under the condition of inert gas protection, graphite is heated to 2700 ℃ by a specific purification furnace, to make impurities gasified and escape, to achieve the purpose of impurity removal. Compared with other purification methods, the purity of purified products can be increased to over 99.99%. The disadvantage is those specific high-temperature furnaces are needed, which have high energy consumption, high investment and production cost, and high requirements for raw material purity.
The application field of the pure high-temperature method is relatively limited. Generally, only graphite products with strict purity (such as spectral pure graphite, nuclear graphite, biomedical graphite, etc.) with strict purity are produced in small quantities. In recent years, enterprises such as Hunan Dingli Technology Co., Ltd. and Zhuzhou Vlad Technology Co., Ltd. have developed industrial-grade high-temperature continuous purification equipment, which can produce high purity amorphous graphite with the fixed carbon content of 99.99%, and the energy consumption is relatively low and the production cycle is short. After further improving the service life and production stability of the furnace, it has a good market promotion and application prospect.
1.2.2 Particle shaping and modification technology
To improve the application value of natural amorphous graphite, it is necessary to improve the particle morphology and other properties by proper technology in addition to purification.
He Ming and others studied the influence of powder-making technology on the structure and electrical properties of amorphous graphite. The smooth and smooth particles were obtained by high-energy ball milling and special grinding classification technology. The irreversible capacity of the modified amorphous graphite was only 12%, and the reversible capacity was 350 MAH / g. Haoxiangyang and others studied the high-speed dynamic impact composite particle system of amorphous graphite particles. After shaping, the amorphous graphite particles were oval and spherical, with a ratio of 1.18 in length to diameter.
The particle size of Shitao is less than l by stirring grinding μ The process of the ultrafine powder with uniform particle size distribution is simple and efficient. The micro-ceramic graphite particles were modified by the wet stirring method and then separated into small particle groups by gravity settlement and hydrocyclone.
The natural amorphous graphite with a high spherical degree and narrow particle size distribution was prepared. Dengchengcai et al. Adopted wet mixing grinding technology, and obtained a ratio of 1.32, -74 μ The yield of M-particle is 42.22% of spherical amorphous graphite. Wang Jing and others studied the processing technology of microcrystalline spheroidization by QWJ airflow vortex pulverizer. Wang Cong et al. First crushed the untreated amorphous graphite, then made the surface of the particles nearly spherical by a particle shaping system. Finally, the particle size distribution was reduced by a centrifugal rotor grading system, and the average particle size was about 9,10,15,20 μ M products with uniform hemispherical and narrow particle size distribution.