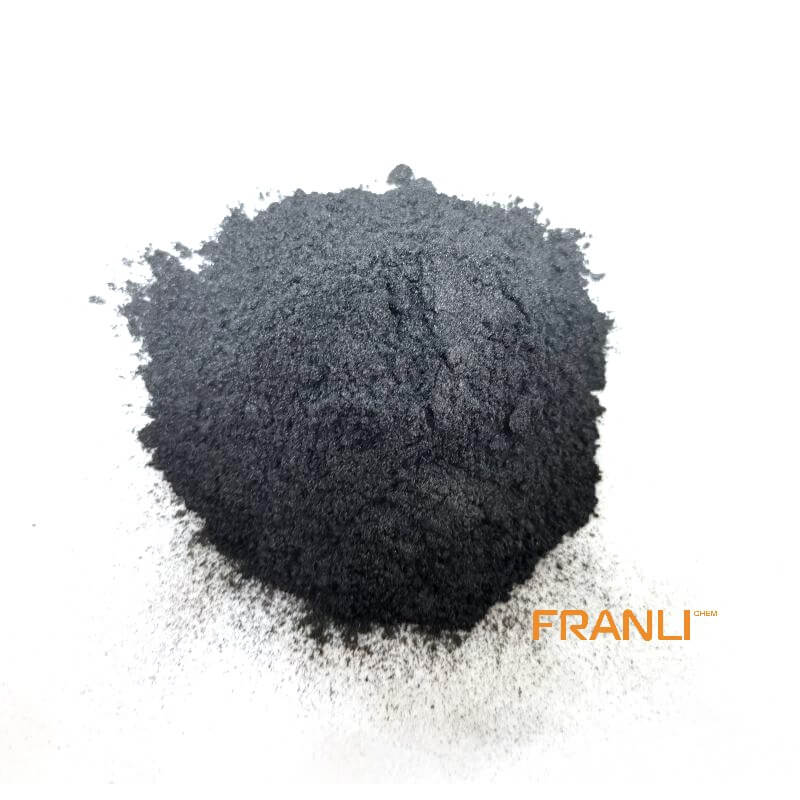
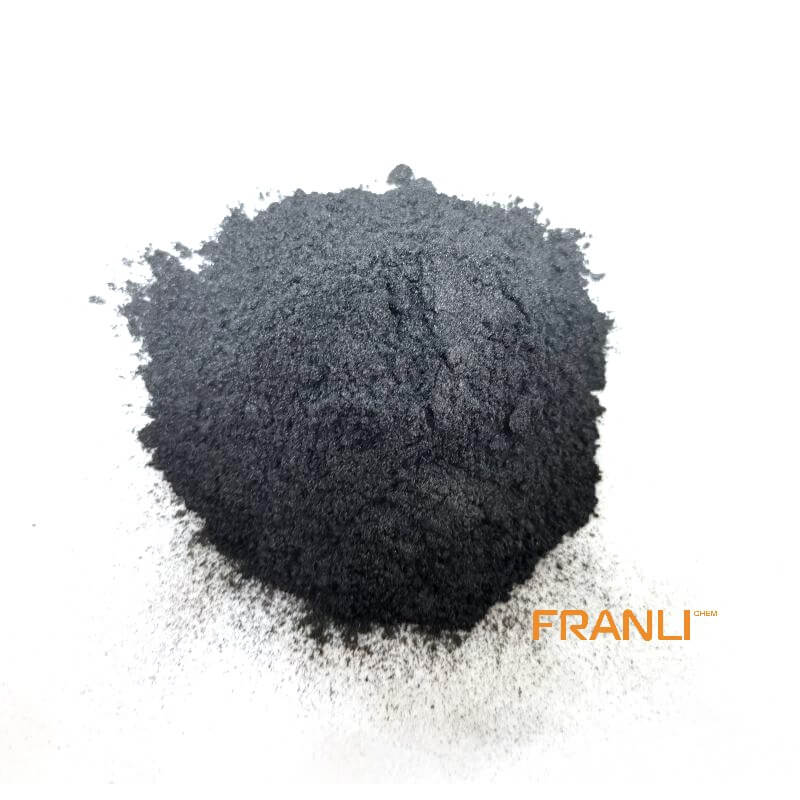
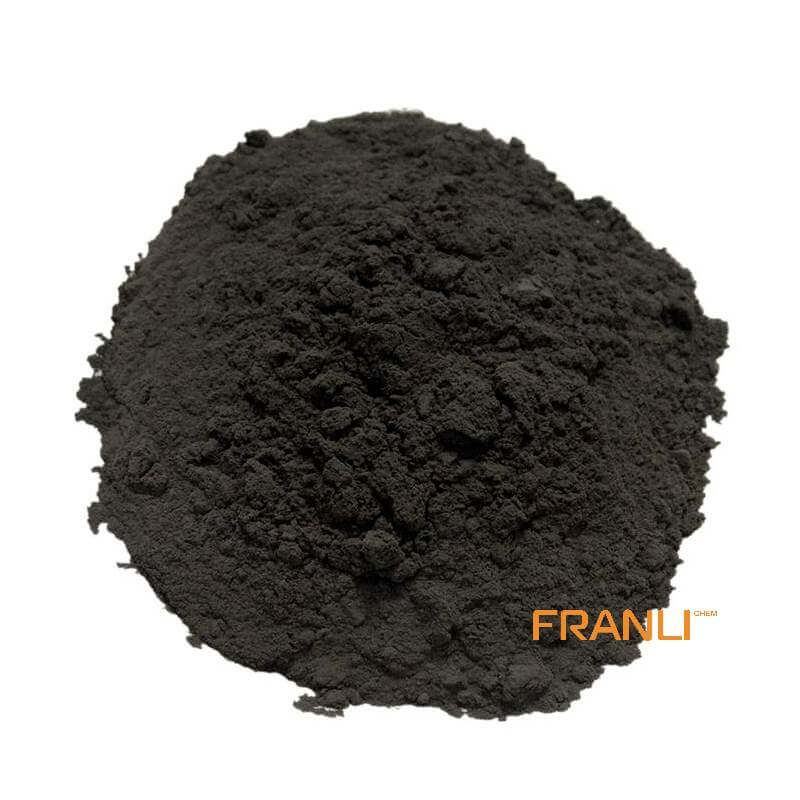
Amorphous Graphite
Size
45μm, 75μm, 150μm, etc
Package
25kg small bags into ton bags or ton bags
Origin
China
Features
Under high temperature conditions, it has special oxidation resistance, etc
Application
Casting coatings, oil field drilling, battery carbon rods, steel, casting materials, refractories, dyes
It is an aggregate of amorphous graphite. The crystal form can be seen only under the electron microscope. Amorphous graphite ore is gray black and steel gray, generally dull, with dense massive, earthy, layered, and lamellar structures. This kind of graphite lacks luster, its lubricity is lower than that of flake graphite, and its selectivity is poor. However, the grade is high, the carbon content is generally 60% ~ 80%, a few are up to more than 90%, the ash content is 15% ~ 22%, the volatile content is 1% ~ 2%, and the moisture content is 2% ~ 7%.
Request a quote
Natural amorphous graphite is widely used in metallurgy, electricity, refractories, battery materials, and other fields because of its high-temperature resistance, chemical corrosion resistance, electrical conductivity, thermal conductivity, and self-lubrication.
1.1 Application in the metallurgical field
Natural amorphous graphite is widely used in metallurgy as a carburizing agent, heating agent, and release agent. The mold flux for iron and steel casting was prepared by using industrial waste and amorphous graphite. The application of amorphous graphite instead of pig iron in 5T and 25t EAF is popularized in Jiangxi steelworks. amorphous graphite is used as a carburizing agent in Lianyuan Iron and Steel Co. Lu Xixing et al. Used amorphous graphite instead of anthracite as desulfurized in alumina production, and the sulfur emission from red mud increased by 40%. Yan Hongyan et al. Studied the carburizing effect of amorphous graphite raw ore at 1600 ℃ and its influence on the mass fraction of S, N, O, and other elements in steel. The results show that the carburizing effect of amorphous graphite is equivalent to that of other carburizes, but has no effect on S, N, O in steel. In the electrolytic aluminum industry, before the anode carbon block and steel claw are assembled, graphite should be sprayed or dipped at a certain height of the steel claw to prevent excessive erosion of the steel claw by high-temperature phosphorus pig iron so that the phosphorus pig iron ring can easily separate from the surface of the steel claw. In China, kerosene and amorphous graphite mixture or water and amorphous graphite mixture are commonly used to dip the anode steel claw.

1.2 Application in grounding field
To prevent damage caused by the lightning attack and ensure personal and property safety, some parts of transmission line towers, substations, high-rise buildings, etc. need to be connected with the ground, which is called grounding. Graphite is an ideal grounding material because of its good conductivity, thermal conductivity, and chemical stability. Wu Shaopeng et al. Prepared conductive concrete by adding the appropriate amount of amorphous graphite into asphalt concrete. Some domestic enterprises press amorphous graphite into grounding resistance reduction modules. Liu Dezhou et al. Used an amorphous graphite resistance reducer to improve the grounding resistance. The practice has proved that in the desert and dry mountain areas with high resistivity, the method of spraying amorphous graphite to reduce the soil resistivity has a significant effect on reducing the grounding resistance of the grounding grid.
1.3 Application of refractory
To improve the thermal shock resistance and slag erosion resistance of refractory, a certain amount of large-scale graphite is usually added to the traditional production ingredients. In recent years, with the need for special steel smelting, the development and application of low carbon refractory has been widely concerned. To ensure the uniform distribution of a small amount of graphite in the products, the particle size of the graphite used should be reduced. amorphous graphite has fine crystal and is more easily ultrafine powder. It is a trend to use amorphous graphite to replace flake graphite to prepare low carbon refractory.
The paper reports the sheet alumina α- Al2O3-C refractories were prepared in a coke oven at 800-1400 ℃ from Al2O3, aluminum, silica powder, silica fume, and ultrafine amorphous graphite. The results showed that the mechanical properties of Al2O3-C refractories with ultrafine amorphous graphite were improved compared with Al2O3-C refractories without superfine amorphous graphite. The results of Wang Heng et al. [41] show that when the ultrafine amorphous graphite composite powder loaded with nickel nitrate is introduced into the aluminum carbon refractories, the formation of multi-wall carbon nanotubes and SiC whiskers can be observed in the materials treated at 1000-1400 ℃, the strength of the materials is greatly improved after heat treatment and the displacement increases at fracture. The results show that the addition of amorphous graphite promotes the formation of SiC whiskers in the materials, obviously improves the compressive strength and heat conduction coefficient of carbon bricks, and increases the 1 in the materials μ The volume ratio of microporous under M. Liang Xiong et al. Introduced amorphous graphite as an active carbon source to the preparation of aluminum carbon refractories containing aluminum powder, silicon powder, and silica micro powder. The results show that the natural amorphous graphite has higher reactivity than flake graphite. The introduction of amorphous graphite can promote the formation of Al and SiC whiskers in the matrix, and improve the mechanical properties of the aluminum carbon materials.
1.4 Application of battery materials
Using natural amorphous graphite as aggregate and coal tar pitch as binder, carbon rods for dry cell were prepared by kneading extrusion roasting polishing wax impregnation process, which has a long production history. Hunan Changning Carbon Co., Ltd., Chenzhou Yongfa graphite products Co., Ltd. and other enterprises have an annual output of more than 20000 tons of carbon rods for various amorphous graphite-based dry batteries, accounting for more than 60% of the global output, which has improved the application value of natural amorphous graphite to a certain extent.
Natural amorphous graphite has fine grains and different orientations, which is beneficial to absorb the deformation energy caused by lithium-ion insertion and removal. It has good structural stability and rate performance and has a good application prospect in the field of lithium-ion power battery anode materials. In recent years, there are more and more researches on natural amorphous graphite-based anode materials for lithium-ion batteries. He Ming et al. [prepared amorphous graphite with a core-shell structure by coating amorphous graphite with resin carbon, which reduced the first irreversible capacity of amorphous graphite. He yuede et al. Used the liquid-phase impregnation process to coat the surface of spherical amorphous graphite particles with resin carbon to improve their electrochemical performance. For the first time, the coulomb efficiency increased from 81.0% to 92.7%.

By optimizing the carbon coating process of amorphous graphite, Shi Yingying et al. Obtained the first modified amorphous graphite with coulomb efficiency of 90.4%, a reversible capacity of 356 MAH / g, and a capacity of 348.1 MAH / G after 25 cycles. Xiao Haihe et al. Coated amorphous graphite with carbon by vacuum impregnation carbonization process. The tap density and coulomb efficiency of the coated amorphous graphite were significantly improved, and the reversible capacity increased from 300 MAH / g to 320 MAH / g.
Using amorphous graphite as raw material, X-8 asphalt as coating agent and binder, Qiao Yongmin et al. Prepared a kind of composite amorphous graphite through integrated grinding shaping and secondary granulation. The first reversible capacity and coulomb efficiency reached 354.4 Ma · H / g and 92.2% respectively. In LiFePO4 / C battery system, the capacity retention rate of the battery reached 91% after 1200 cycles. Kyung Jin Kim et al. Prepared hard carbon and amorphous graphite core-shell composites, which have high reversible capacity, first-coulomb efficiency, high charge-discharge rate, and good cycle stability.
Using amorphous graphite as conductive aggregate and thermosetting resin as binder, Lin Zhengyu prepared amorphous graphite/resin composite bipolar plate for proton exchange membrane fuel cell by the molding process. The results show that the properties of bipolar plate are as follows: bending strength > 25 MPa, electrical conductivity > 100 s / cm, gas permeability < 3.5 MPa, curing temperature 140 ~ 145 ℃, molding pressure 15 ~ 20 MPa, and molding time 18 ~ 22 min, using 18% ~ 20% bisphenol a vinyl resin as binder, amorphous graphite powder with the particle size of 200 ~ 250 mesh as conductive aggregate × 10-5 mL/(s·cm2)。
Conclusion
A thorough understanding of the basic structure and characteristics of natural amorphous graphite is the key to guiding the development of the amorphous graphite industry. At the same time, we should further strengthen the development of high-efficiency, environmental protection, low-cost purification technology, particle shaping, surface modification, and other technologies, encourage independent innovation and product development, and promote the industrialization of relevant scientific research achievements. With the continuous development of new theories, new technologies, and new equipment, natural amorphous graphite will be widely used in new refractories, new energy materials, advanced composites, and other fields, and have a profound impact.