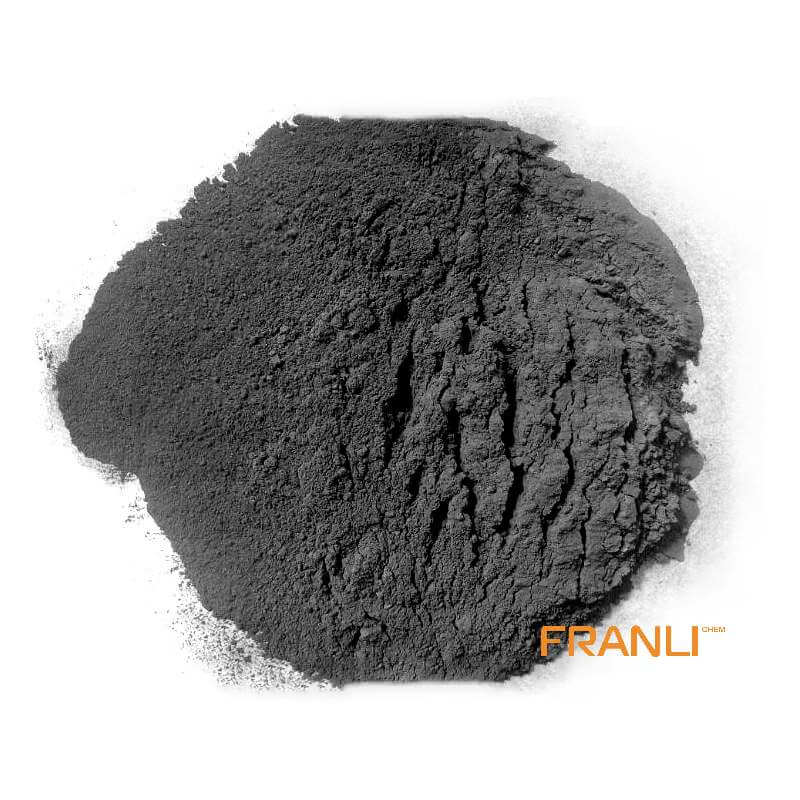
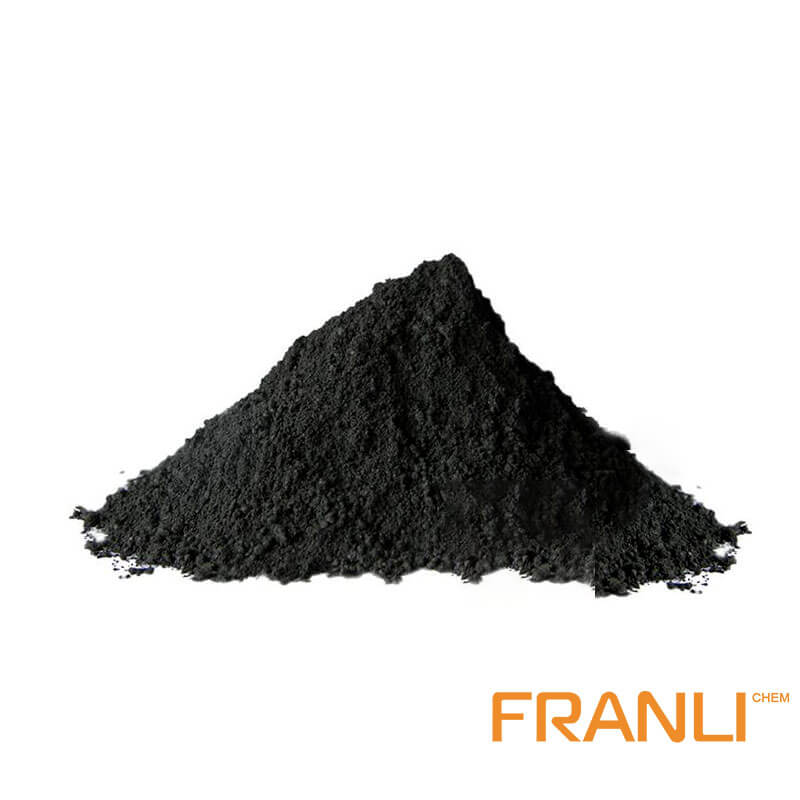
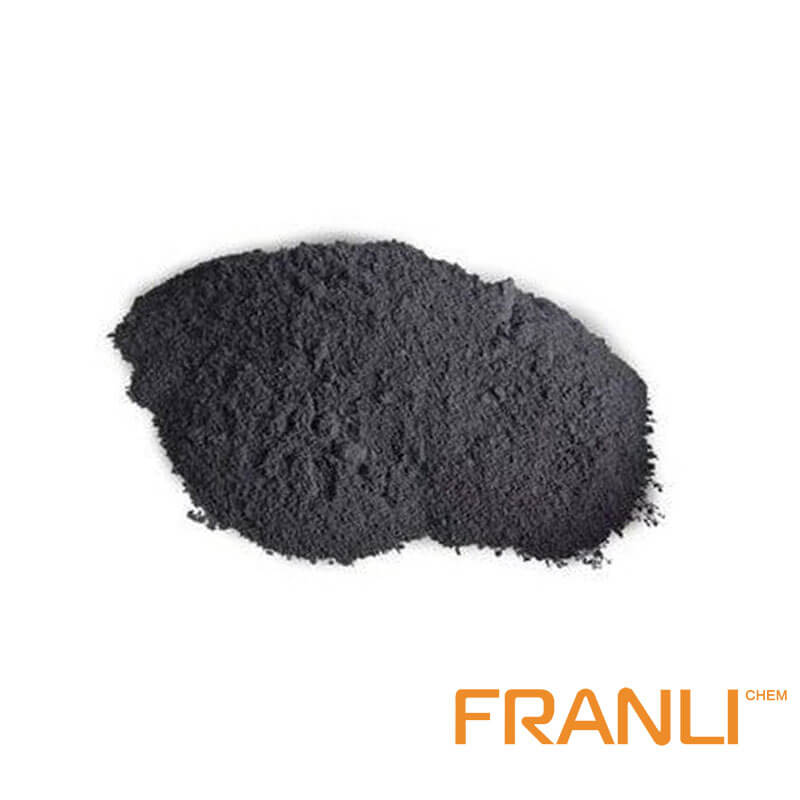
Artificial Graphite
Size
0.01mm or 0.07mm,etc
Package
25 kg small bags into ton bags or ton bags
Features
Good wear resistance, corrosion resistance, good thermal conductivity, etc.
Application
Can be used in making heat exchanger, reaction tank, absorption tower, etc.
There are many kinds of artificial graphite and different production processes. In a broad sense, all graphite materials obtained by carbonization of organic matters and treated by high temperature after being treated with graphite can be collectively referred to as artificial graphite.In the narrow sense, artificial graphite usually refers to the massive solid materials prepared by batching.
Request a quoteGraphite anode materials are divided into artificial graphite and natural graphite. From the perspective of the negative electrode market shipment structure, the market share of artificial graphite has gradually increased, accounting for the majority of the market share, while the share of natural graphite has shown a downward trend. The production process of artificial graphite is mainly divided into four parts: crushing, granulation, graphitization and screening. The production process of artificial graphite is complex, and graphitization is one of the key links.

Graphitization of artificial graphite
What is the graphitization? Graphitization refers to the transformation of non-graphitic carbon into graphitic carbon with a three-dimensional regular and ordered structure of graphite after high temperature heat treatment. Originally originated in the carbon product industry, it is an essential process for the production of graphite electrodes. Graphitization is to improve the thermal and electrical conductivity of carbon materials, improve the thermal shock resistance and chemical stability of carbon materials, make carbon materials have lubricity and wear resistance, and improve the purity of carbon materials.
Atomic rearrangements and structural transformations are energized using high-temperature heat treatment, a process that consumes large amounts of energy. Electricity is the main energy consumed in graphitization production. Usually, electric heating is used to heat semi-finished products to above 2800°C, which consumes a large amount of electricity and takes a long time. Electricity accounts for up to 60% of the cost of graphitization, and the cost of graphitization accounts for 55% of the manufacturing cost of artificial graphite negative electrodes.
The production process of artificial graphite
The preparation of artificial graphite needs to go through four major processes and more than ten small processes. The aggregates of artificial graphite are divided into three categories: coal series, petroleum series and coal and petroleum mixed series. It is made by crushing, granulating, graphitizing and sieving aggregates and binders.

(1) Pretreatment: According to different products, the graphite raw materials and asphalt are mixed in different proportions, and the mixing ratio is 100:(5~20). particle size material. The filter element is made of filter cloth with pores smaller than 0.2 microns, which can intercept all dust above 0.2 microns. The fan controls the whole system to be in a negative pressure state.
(2) Granulation: ①Pyrolysis process: put the material into the reaction kettle, under the pressure of 2.5Kg, carry out electric heating according to the temperature curve, stir to obtain the material with a particle size of 10-20mm, cool down and discharge, that is, the middle materials. The volatile gas in the reaction kettle is extracted by the fan, condensed by the condensation tank, and the gaseous waste gas is drawn out by the fan, filtered by activated carbon and then emptied.
②Ball milling and screening process: vacuum feeding, the intermediate material is transported to the ball mill for mechanical ball milling, the powder is transported to the screening machine through the pipeline for screening, and then returned to the ball mill to be ball-milled again by the pipeline vacuum transport. Ball milling and screening are all carried out in an airtight manner, the materials are conveyed by vacuum, the gas and material are shaken and separated, and the dusty waste gas after the gas and material separation is filtered by the filter element and discharged from the workshop.
(3) Outsourced graphitization: The graphitization process is processed in the form of outsourced processing, and the intermediate materials are subjected to graphitization processing.
(4) Ball Mill Screening: The graphitized artificial graphite material is transported to the ball mill by vacuum, and undergoes physical mixing, ball milling, screening, and inspection, measurement, packaging and storage of the material under the screen.
At present, artificial graphite, the anode material of the Franli factory, is gradually moving towards the field of new energy technology, which can reduce the consumption of metal materials and control costs more favorably. Negative companies have gradually explored new graphitization technologies. The Franli factory uses Acheson furnaces and continuous graphitization furnaces to manufacture artificial graphite, and carefully screen the quality and size of artificial graphite.