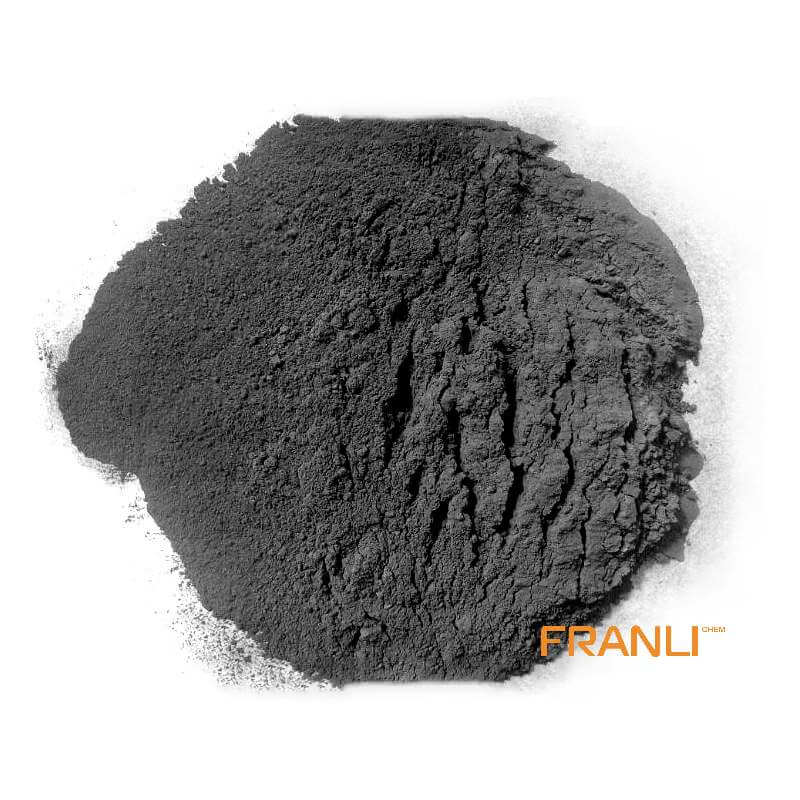
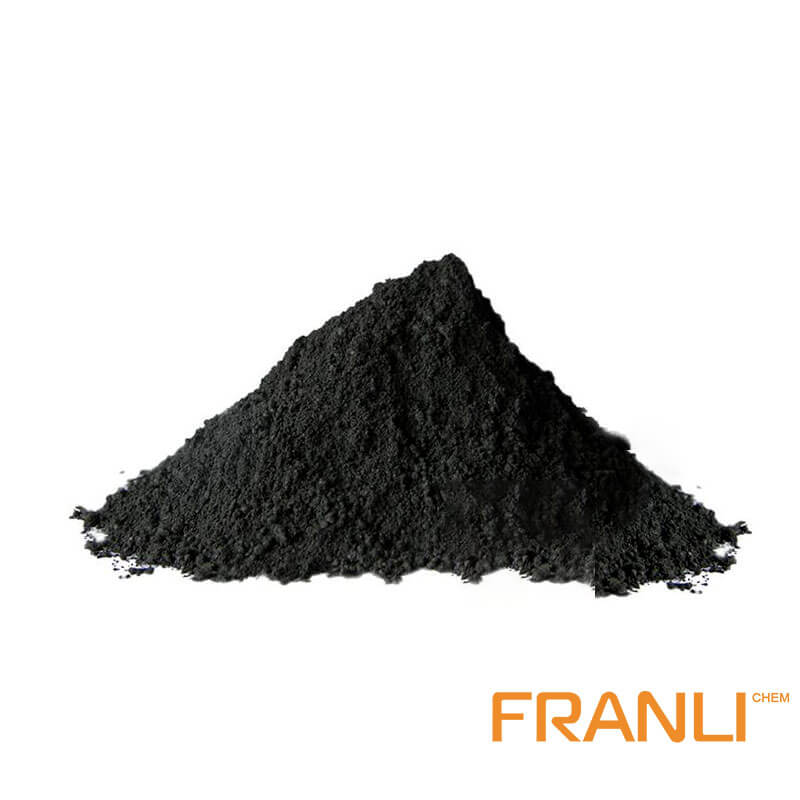
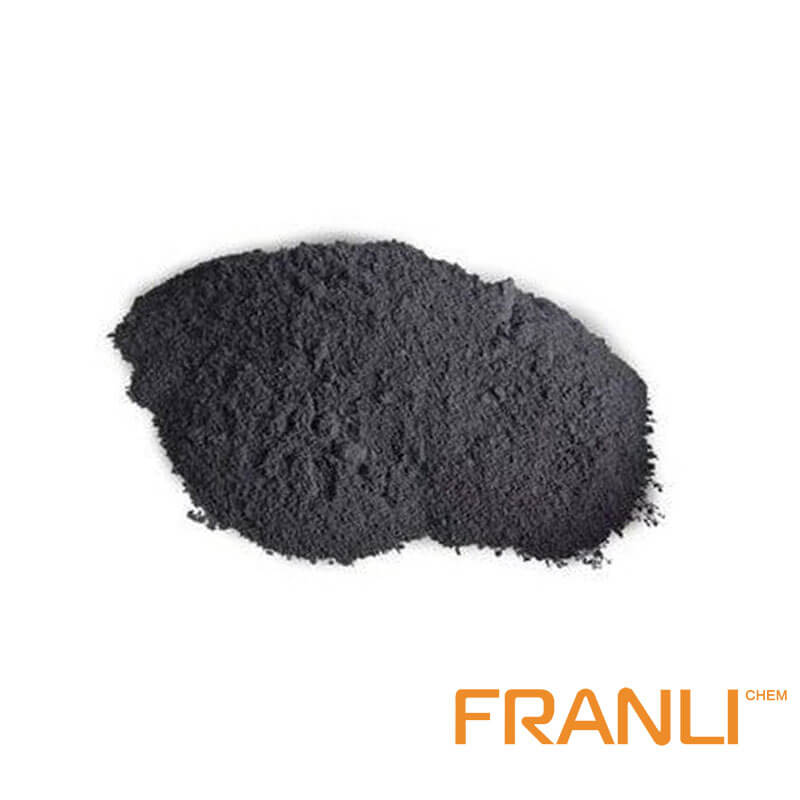
Artificial Graphite
Size
0.01mm or 0.07mm,etc
Package
25 kg small bags into ton bags or ton bags
Features
Good wear resistance, corrosion resistance, good thermal conductivity, etc.
Application
Can be used in making heat exchanger, reaction tank, absorption tower, etc.
There are many kinds of artificial graphite and different production processes. In a broad sense, all graphite materials obtained by carbonization of organic matters and treated by high temperature after being treated with graphite can be collectively referred to as artificial graphite.In the narrow sense, artificial graphite usually refers to the massive solid materials prepared by batching.
Request a quote
Artificial graphite is used more and more now, in fact, the development of new graphite products based on the preparation process of artificial graphite is not a new topic in the artificial graphite industry. With natural graphite as the main raw material or auxiliary raw material, many carbon graphite products have been prepared according to the production process of artificial graphite, and some have even formed a large industry.
Zinc manganese battery carbon rod: the carbon rod of zinc manganese battery (commonly known as a dry battery) produced by kneading, extrusion, roasting, machining, wax dipping, and other processes with natural microcrystalline graphite and coal asphalt as the main raw materials.
It mainly uses the characteristics of high conductivity and low price of natural microcrystalline graphite and has low requirements for ash content, but strict requirements for iron, sulfur, and other impurities.

Natural graphite brush: motor brush produced by kneading, rolling, grinding, molding, roasting (graphitization treatment if necessary), machining, and other processes with natural flake graphite and coal asphalt as the main raw materials.
The characteristics of high conductivity and high orientation of natural flake graphite are mainly used. It is required that the content of impurities such as iron and sulfur is low and the ash content is not higher than 2%. Pay attention to the orientation of flake graphite during machining.
Carbon graphite materials for machinery: block materials produced by kneading, rolling, grinding, molding, roasting, and other processes with natural graphite and coal tar pitch as the main raw materials need to be precision machined according to the user requirements.
It mainly uses the lubricity, high-temperature resistance, and corrosion resistance of natural graphite, and has high requirements for ash and impurity content.
As can be seen from the above examples, compared with the narrow artificial graphite, the carbon graphite products prepared according to the artificial graphite production process with natural graphite as the main raw material or auxiliary raw material have the following differences in the production process and product performance:
(1) The former usually needs graphitization treatment above 2500 ℃ to obtain the required physical and chemical properties, while the latter can be graphitized or not.
In order to reduce the production cost, graphitization treatment is usually not carried out, so there is a “carbon” phase transformed from binder asphalt in its microstructure.
This kind of carbon, which is located around the graphite particles and combines the graphite particles together, has high hardness and far lower conductivity than natural graphite, so it has a great impact on the service performance of the product.
(2) Natural graphite usually exists in powder form and has poor adhesion with coal tar pitch. Carbon graphite products prepared from natural graphite usually have disadvantages such as large porosity, low mechanical strength, poor oxidation resistance, and thermal shock resistance. Therefore, the product specification can not be too large, and the application field is also greatly limited.
Based on the above analysis and discussion, the author believes that the following technical problems should be paid attention to when developing artificial graphite with natural graphite as raw material:
Surface modification of natural graphite. Compared with carbonaceous raw materials such as petroleum coke and asphalt coke, natural graphite has fewer oxygen-containing functional groups on the surface, lower activity, and poor adhesion with coal tar pitch,
Therefore, with natural graphite, especially natural flake graphite as the main raw material, the carbon graphite products prepared according to the artificial graphite production process inevitably have the problem of poor mechanical properties. Proper surface treatment of natural graphite is needed to increase the content of oxygen-containing functional groups on its surface.

Purification of natural graphite. The purity of carbonaceous raw materials such as petroleum coke and asphalt coke is high, and the ash content is usually less than 0.5%, while the purity of natural graphite treated by flotation is low, and the carbon content is usually less than 90%,
Therefore, the application field of carbon graphite products prepared from natural graphite is often limited due to its low purity and poor comprehensive performance. High purification of natural graphite is one of the ways to solve this problem.
The cost of chemical purification is low, but the water consumption in the washing process is large and the pollution is large, while the cost of high-temperature purification is high. Others believe that block graphite can be prepared according to the production process of artificial graphite, and then through high-temperature heat treatment above 2500 ℃,
While graphitizing the “carbon” phase, the impurities in the natural graphite phase are removed, but first, the production cost is increased, and second, the defects formed after impurity gasification often lead to the decline of product performance.
The particle size of natural graphite. In order to improve the process performance and product performance, except for fine structure carbon graphite products, most carbon graphite products need to use carbon raw materials with different particle sizes in the batching process. For some large-scale products, the particle size of carbon raw materials even reaches 16mm, while the natural graphite treated by flotation is often fine powder, and the particle size is only tens to hundreds of microns, Therefore, the use of natural graphite as raw material is limited to the preparation of fine structure carbon graphite products.
Although natural microcrystalline graphite with different particle sizes can be obtained, there is no report on the preparation of coarse structure carbon graphite products from natural microcrystalline graphite because of its low purity and high cost of high-temperature purification. In order to solve the problem of lack of large particle natural graphite, it is suggested to adopt the “secondary coke” process in the treatment of carbon black raw materials in the artificial graphite industry.
Volume shrinkage during preparation. In the preparation of artificial graphite, especially in the graphitization process, the volume shrinkage of the product is large because the arrangement of carbon atoms gradually changes to the regular graphite structure.
The advantage of this volume shrinkage is that it can improve the density of the product, but when the shrinkage is uneven, it is easy to cause the product to crack. When natural graphite is used as raw material, the density and mechanical properties of the products are low due to the small volume shrinkage in the process of carbonization and graphitization.
In addition, when developing artificial graphite with natural graphite as raw material, it is also necessary to consider the problem of comprehensive production cost.

Since the price of natural graphite after flotation is similar to that of calcined petroleum coke and asphalt coke, and when the carbon content reaches 98%, the price of natural graphite is nearly twice that of calcined petroleum coke and asphalt coke. Therefore, in addition to the above-mentioned carbon graphite products that have formed a large industry, The proposal of most technical routes and measures will greatly increase the production cost.
Conclusion
To sum up, the development of artificial graphite products with natural graphite as raw material is one of the important ways to expand the application field of natural graphite.
As an auxiliary raw material, natural graphite has long been used in the production of some artificial graphite, but there are still many problems to be solved in the development of artificial graphite products with natural graphite as the main raw material.
A better way to achieve this goal should be to fully understand and make use of the structure and characteristics of natural graphite and adopt appropriate process routes and methods to produce artificial graphite products with special structure, performance, and purpose.