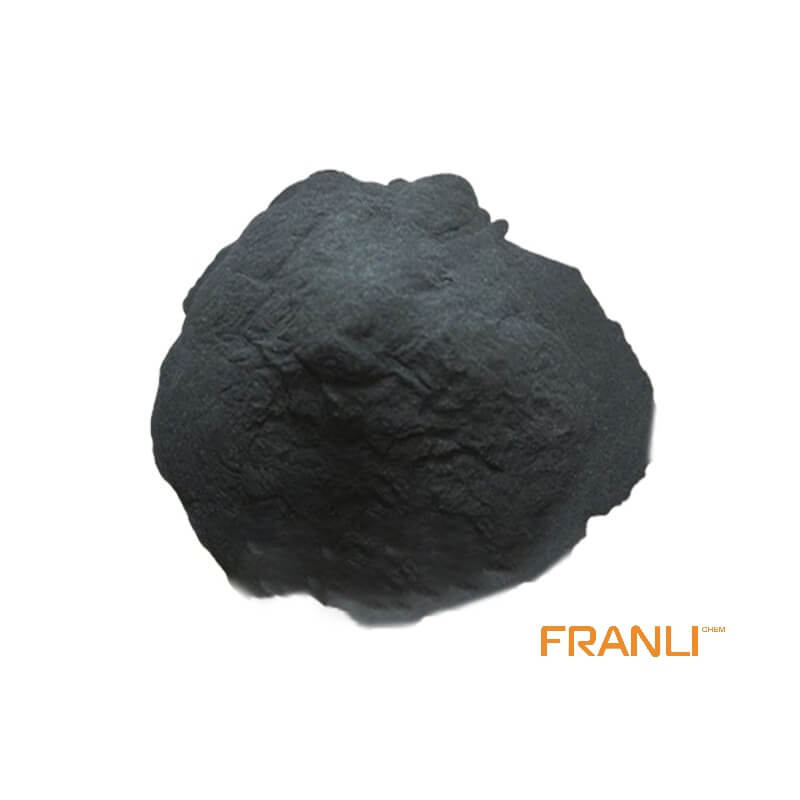
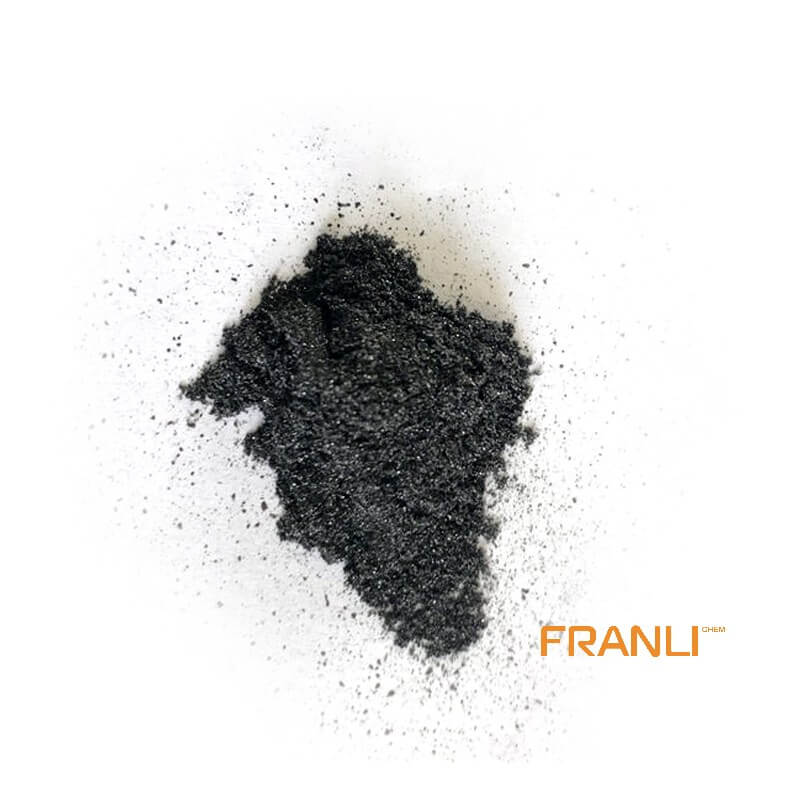
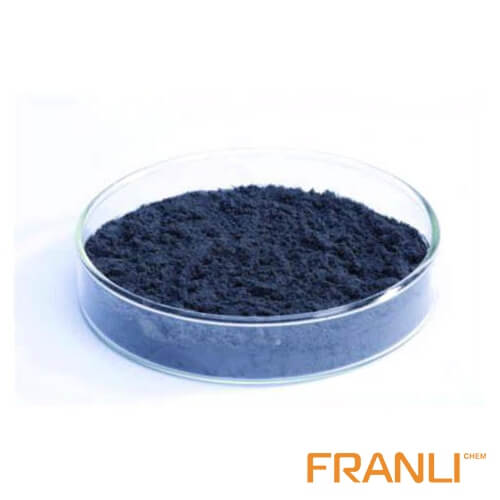
Expandable Graphite
Size
0.50mm or 0.106mm, etc
Package
25 kg small bags into ton bags
Origin
China
Features
Preservative/Electrical and thermal conductivity, etc.
Application
Fireproof sealing element, flame retardant, refractory brick, etc.
Expandable graphite crystal is a typical layered carbon material. Other heterogeneous particles such as atoms, molecules, ions, and even atomic clusters are inserted into the interlayer of crystalline graphite by physical or chemical methods to form a new layered compound, which is called graphite interlayer compound, namely expandable graphite.
Request a quote
Expandable graphite performs very well in flame retardants. A large number of studies and experiments show that expandable graphite (EG) on
RPUF flame retardant effect is obvious
Expandable graphite is a new type of flame retardant used by halogen-free flame retardant technology at present. The flame retardants are crystalline compounds formed by the chemical and physical insertion of intercalators into planar structures with hexagonal networks of carbon between graphite layers. In practical use, the principle of this flame retardant is as follows: When heated crystal compounds, layer between the insert material because of heat decomposition or gasification, resulting in a large amount of heat expansion, because inflation hot far greater than the graphite van der Waals force of the space, so the lamella is airflow heaving liter so that the distance between graphite has further expanded, thus has formed the expansion of the “vermicular graphite. The large specific surface area and low-density characteristics of expanded graphite make it have strong pressure resistance, flexibility and plasticity, corrosion resistance and oxidation resistance and resistance to high and low-temperature ability are also strong, so the effect of flame retardant is better.

Polyurethane (PUR) foam components used in automotive and industrial applications around the world are subject to increased fire protection requirements, which are also based on regulatory requirements.
Kraussmaffei will present a complete system for high-pressure machining of expandable graphite at K 2019.
“Expandable graphite is an economical filler that offers distinct advantages for many automated processes.” “Unfortunately, this material is very sensitive to mechanical stress during processing,” said Nicolas Beyl, general manager of Kraussmaffei’s reaction Molding technology division.
A new development of high pressure with low-pressure bypass mixing head and special premix used in the measurement of expandable graphite, which can be expanded graphite as a flame retardant and become a very effective alternative to liquid mixture, or additives, fully automated process chain to ensure that the components of the production cycle time are short, to make the system more efficient.
High-pressure countercurrent injection mixing has advantages in precision machining of highly active PUR foam systems, so it can be used in applications where expandable graphite is used as filler, which is the basis for achieving short cycle times and thus improving production efficiency.
Unlike processing in the low-pressure range, the self-cleaning mixing head eliminates the flushing process after each injection, saving material, reducing production time, and ensuring consistent product quality, while eliminating the expense of supplying and handling the flushing material.

Higher mixing energy is also obtained during high-pressure mixing, which helps reduce cycle times.
A special expandable graphite mixing head is at the heart of this technology, based on Kraussmaffei’s efficient high-pressure mixing head.
The system is equipped with a low-pressure bypass with an enlarged cross-section and is specially designed for the processing of expandable graphite.
Thus, the polyols are added in a continuous cycle, in the process minimizing the mechanical stress applied to the expandable graphite particles between cycles.
As the material circulates through the nozzle, the pressure increases only before pouring begins, so the mechanical stress of the packing is minimal.
It is possible to achieve high filling levels using this technology, and depending on the raw material system, the percentage of expandable graphite in the polymer by weight can be up to 30% or more, thus achieving the high flame retardant rating of UL94-V0.
The polyalcohol-expandable graphite mixture is prepared in a dedicated premix station, where a special stirrer evenly mixes the filler and liquid components in a gentle manner that “preserves both the structure and size of the expandable graphite particles”.
Metering is automated and can be increased up to 80% (by weight) in polyols, thus ensuring consistent quality throughout.
In addition, the production is cleaner and more efficient due to the elimination of manual handling, weighing, and adding steps.
In addition, the weight and volume of components can be optimized by adjusting the mixing ratio of expandable graphite with other components during premixing, without affecting the flame retardant performance.