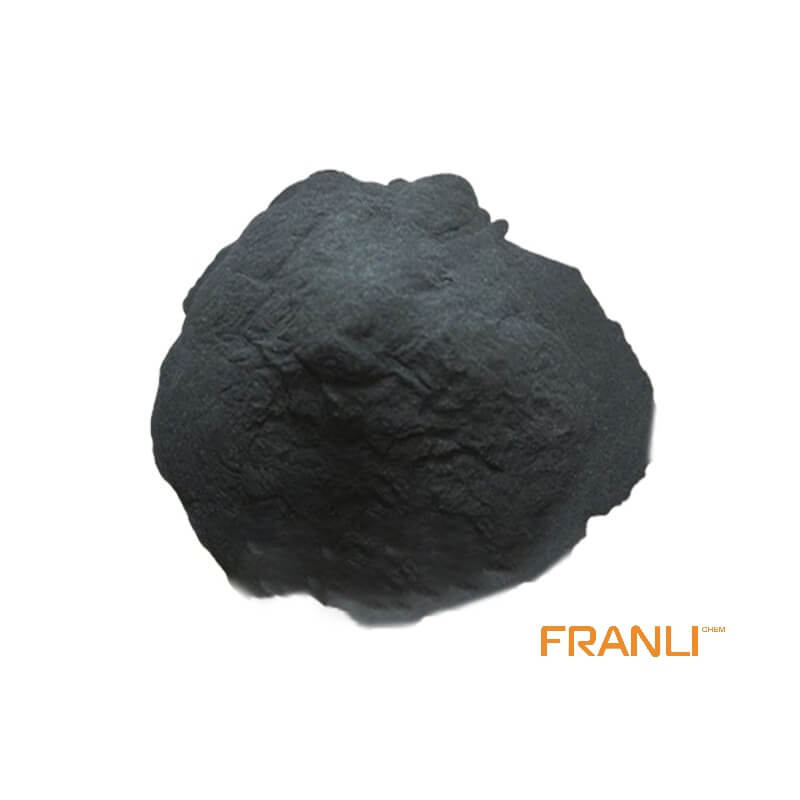
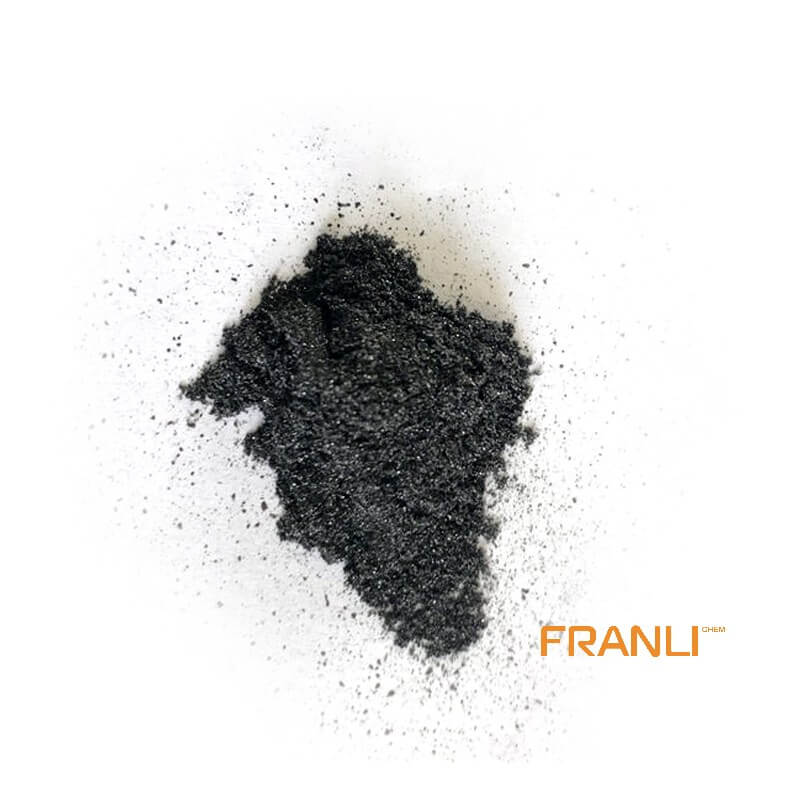
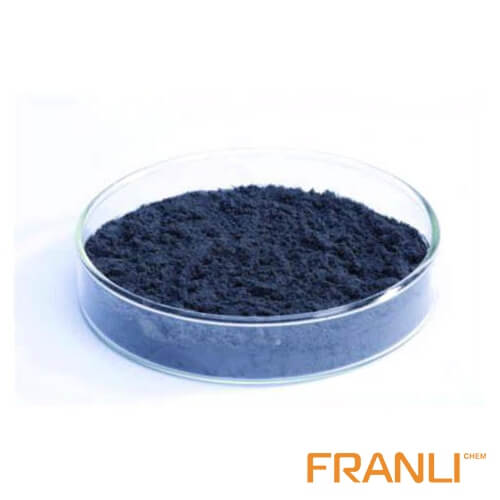
Expandable Graphite
Size
0.50mm or 0.106mm, etc
Package
25 kg small bags into ton bags
Origin
China
Features
Preservative/Electrical and thermal conductivity, etc.
Application
Fireproof sealing element, flame retardant, refractory brick, etc.
Expandable graphite crystal is a typical layered carbon material. Other heterogeneous particles such as atoms, molecules, ions, and even atomic clusters are inserted into the interlayer of crystalline graphite by physical or chemical methods to form a new layered compound, which is called graphite interlayer compound, namely expandable graphite.
Request a quote
Abstract: the expansion mechanism and pore structure of expandable graphite were briefly introduced. The effects of graphite purity and particle size, intercalation method, water washing degree, expansion method, and expansion temperature on the expansion volume in the process of chemical oxidation were mainly introduced. Combined with the related research results in the literature, the evolution process and the following ideas of graphite oxide in recent years was revealed, The future research direction was put forward, and the influence of technological conditions on the structure and properties of graphite was discussed, as well as the deep optimization, so as to lay the foundation for the preparation of graphite products with excellent properties.
Expandable graphite is a wormlike material made from natural flake graphite, which is washed to neutral after chemical treatment, and then filtered dried, expandable, and other processes. Its structure is loose and porous, with a high specific surface area, and its size is usually between a few millimeters to a few nanometers. It has the following advantages: stable chemical properties, high adsorption, high seismic resistance, high thermal stability, high thermal stability, high thermal stability, and so on High resilience and many other excellent properties are widely used in military, mechanical, environmental protection, medicine, and electric power fields. In addition to these fields, expandable graphite also has a good application prospect in thermal insulation materials, sound insulation materials, heat dissipation materials, and fire retardant materials.
The preparation process is the main factor affecting the expansion volume of graphite. Among the numerous preparation processes of graphite, chemical oxidation has become the most widely used and mature method for the preparation of expandable graphite because of its low requirements for equipment and simple operation. The chemical oxidation method is to open the edge of graphite by the reaction of natural flake graphite and oxidant, and the intercalation agent enters into the graphite interlayer to form GIC (graphite intercalation compounds).

Some strong oxidants and intercalation agents need to be used in the preparation process. These substances are difficult to be thoroughly cleaned in the water washing process so that the final product contains sulfur or other impurities, which is easy to cause environmental pollution, product application limitation, and other problems. In order to solve these problems, researchers have done a lot of research on the influence of the ratio of oxide intercalation agent and reaction conditions on the expansion volume of expandable graphite in recent years, in order to prepare low energy consumption, pollution-free, and high-quality expandable graphite. This paper introduces the expansion mechanism and evolution process of expandable graphite analyzes and summarizes the influence of various factors in the preparation process on the expansion volume, in order to promote the further research and development of expandable graphite preparation.
Expansion mechanism and structure of expandable graphite
1.1 Expansion mechanism
Chemical treatment and high-temperature heating are the main reasons for the volume expansion of graphite. The density of graphite is 2360 kg / m3. After chemical treatment, new compounds are formed between graphite layers, and the interlayer distance is 3.35 × 10-10m to 6 × 10-10~11 × 10-10m, forming the first expansion. Due to the instability of the intercalation compound, when heated at a high temperature, the expansion force generated by the vaporization of the intercalation compound is greater than the molecular force of the interlayer bonding, which further expands the interlayer distance, which is called the second expansion. The density after the expansion is 800-1600 kg / m3, and the interlayer spacing is 80-300 times larger than before, forming expandable graphite.
1.2 Structural features
The shape and structure of exfoliated graphite are quite different from that of natural flake graphite. The internal pore structure of exfoliated graphite can be divided into four levels. From the macro point of view, it is mainly composed of microcells of micron level; In terms of microstructure, there are many fine pores on the microcell, which form the rich internal pore structure of expandable graphite; Under the action of high temperature, the original plane layer of graphite is fissioned, the structure is deformed unevenly, and the overall appearance is curly wormlike. The origin of this shape can be explained by FIG. 1A ~ Fig. 1C: firstly, it is assumed that a, B, C, D, and E are certain concentration points of the intercalation compound, as shown in Fig. 1a. When the graphite is heated, a, B, D, and e produce extrusion pressure pa-PB and PDPE toward both ends of the C surface, as shown in Fig. 1b. Because the pressure PC needs to push the C layer away from both sides, the vermicular graphite block.
The evolution of expandable graphite
2.1 Conventional expandable graphite
In 1841, German scientist shafautl immersed graphite in the mixture of concentrated sulfuric acid and concentrated nitric acid, and found the precursor graphite interlayer compound (GIC) of expandable graphite for the first time; In 1859, Brodie was prepared by using flake graphite as raw material and KClO3 as an oxidant in the concentrated nitric acid system; In 1898, staudenmaier prepared graphite oxide by oxidation reaction of graphite-based on Brodie method with concentrated nitric acid and sulfuric acid as the system. These two methods can control the oxidation degree by changing the oxidation reaction time, but it takes a long time to fully react and a large number of toxic gases will be produced during the reaction.
In 1958, Hummers proposed that the reaction products were diluted and washed to neutral with 5% HCl solution and deionized water wash in the low temperature (0 ℃), medium temperature (35 ℃) and high temperature (below 98 ℃) with KMnO4 and nano 3 as oxidants in the concentrated sulfuric acid system. Finally, the graphite oxide was dried in a vacuum drying oven. The method has the advantages of short reaction time and high oxidation degree. KMnO4 instead of KClO3 improves the safety of the experiment and reduces the production of toxic gas. However, due to its long process, there are many factors to be controlled. Some researchers have found that it can be further optimized.
In 2010, Marcano, based on the Hummers method, used KMnO4 as an oxidant, and pre-oxidized graphite with 98% concentrated sulfuric acid, which increased the reaction time at low temperature, and finally washed and dried to get the graphite oxide. The improved Hummers method not only has the advantages of the Hummers method but also reduces the use of NaNO3. The graphite oxide crystal structure is regular, the oxidation degree is high and the by-products are few. After that, the researchers mainly changed the types, dosage, reaction temperature, and reaction time of reaction reagents, and optimized the preparation process. It was found that in the improvement of the Hummers method, the oxidation degree of graphite was very small in the low-temperature reaction stage. Therefore, the low-temperature stage was saved and the time of the reaction stage was increased appropriately, and the preparation process was further simplified, The preparation efficiency is improved. This method is called the “simplified Hummers” method and is a common method for the preparation of graphite oxide.
Jiang Lina prepared a kind of low-temperature flame retardant additive expandable graphite from natural flake graphite, KMnO4, and 68% HNO3 and 70% H2SO4. In the reaction process, a certain amount of oxidant was added to the reaction. The influence of various factors on the expansion volume was analyzed by changing the proportion of nitric acid in the mixed acid, the reaction temperature and time, and the amount of oxidant, The expandable graphite was 400 ml / G under the condition of expansion at 600 ℃ after 50 min. the expandable graphite was tested to be stable and nonhygroscopic in the air; On the basis of Jiang Lina, lvpu added iron trichloride as an auxiliary intercalator. The influence of KMnO4, FeCl3, the amount of mixed acid, the ratio of H 2SO4 to HNO3, reaction time, and reaction temperature on the expansion volume of graphite was observed, The expansion volume of 240 ml / g was determined by orthogonal experiment under the conditions of scale graphite: potassium permanganate: iron trichloride: mixed acid (sulfuric acid: nitric acid = 2:1) = 1:1:0.1:3, reaction time 30 min, reaction temperature 15 ℃; Fengxiaotong used potassium dichromate as oxidant, and sulfuric acid, phosphoric acid, and nitric acid as intercalating agents respectively. The expandable graphite prepared by the best ratio technology knew that the best intercalation effect of sulfuric acid was obtained, the highest expansion rate, the expansion volume reached 260 ml / g, followed by nitric acid, and phosphoric acid was the lowest.
This is because sulfuric acid and nitric acid are also oxidizable while they are intercalators. When the oxidation intercalation is carried out, it can play the oxidation role with potassium dichromate. The graphite layer is fully opened, and the low oxidation of phosphoric acid leads to a poor intercalation effect, so the expansion degree is the lowest.
The oxidant usually uses potassium permanganate or potassium dichromate, and the intercalator selects sulfuric acid or nitric acid with oxidation properties. It can not only reduce the discharge of nitrogen and the amount of sulfuric acid but also enhance the oxidization of oxidants. Therefore, chemical oxidation has become the most widely used and mature method in the industry. However, because the solid oxide is not volatile and it is not easy to clean in the process of water washing, it will eventually lead to the large sulfur content of the product, and it is easy to cause environmental pollution and equipment corrosion. Therefore, it is very important to reduce the sulfur content of the product by changing the type and dosage of oxidant and intercalator.

2.2 Low sulfur expandable graphite
Generally, sulfuric acid needs to be strengthened with an oxidant to improve its intercalation power, but it will cause environmental pollution and high sulfur content of products. Based on this problem, some scholars try to use hydrogen peroxide as an oxidant, add ice acetic acid, iron trichloride, and other auxiliary intercalators to reduce the sulfur content of samples and obtain satisfactory results. Zhang pengguo first immersed the flake graphite in the mixed acid solution of H2SO4 HNO3 for pre-oxidation, then added KMnO4 and FeCl3 to carry out an oxidation reaction, and then the expandable graphite with low sulfur was obtained by filtration, drying, and expansion.
According to the experimental results, it is found that the effect of FeCl3 content and expansion temperature on expansion volume is consistent with previous research results in the best process of sulfuric acid + nitric acid system, and the reason for the difference of the optimal proportion of oxide intercalators may be due to the difference between the purity and particle size of graphite raw materials, The general trend of expansion volume and oxide intercalator content of expandable graphite is parabola, and the maximum expansion ratio is close to 375 times; The expandable graphite with an expansion volume of 225 times is obtained by the method of one-step method at room temperature. The method can be completed at room temperature without heating, and the concentration of sulfuric acid can be reduced by about 85%.
Song intercalated with flake graphite with ammonium persulfate and concentrated sulfuric acid as oxidation intercalator. After that, 80% of sulfuric acid in the reaction solvent was removed and the acid graphite was soaked in the mixed acid solution of nitric acid oxalic acid. The sulfuric acid molecules or hydrogen sulfate ions in sulfuric acid were replaced by nitrate ions and oxalic acid molecules, However, oxalic acid can be reduced to low-cost compounds due to its strong reducibility during high-temperature expansion, and only 0.65% of the expandable graphite with sulfur content can be obtained; Liping and Li Jihui prepared low sulfur expandable graphite with a sulfur content of 0.11% by using hydrogen peroxide as oxidant and acetic anhydride as intercalator respectively, which is far lower than 4.5% of the traditional method.
The sulfur content of the product is reduced by changing the type of oxide intercalator. However, there are still sulfur ion groups between graphite layers. When heated at high temperatures, some of the sulfur ion groups are oxidized to SO2 gas and escape. While other sulfur ion groups continue to adsorb on the surface of expandable graphite, the residual sulfur will still affect the equipment and environment, The application of expandable graphite in some fields is limited; Although the reaction of hydrogen peroxide is mild and stable, its oxidation ability is weak, which is not enough to open the graphite sheet layer to make the intercalation enter. Therefore, it is still the main research direction to prepare sulfur-free expandable graphite by selecting materials and optimizing the ratio while ensuring the high quality of expandable graphite.
2.3 Sulfur-free expandable graphite
In recent years, researchers at home and abroad try to change the preparation sequence or use nitric acid, phosphoric acid, and other non-sulfur acid solutions instead of concentrated sulfuric acid as intercalation agents to prepare expandable graphite and have made some breakthrough progress. For the first time, Inagaki et al. Prepared sulfur-free expandable graphite by putting graphite and sodium in tetrahydrofuran solution, but this method is not suitable for wide application because of its harsh reaction conditions and slow reaction process; Yang Wei designed an orthogonal experiment to prepare expandable graphite with oxidant, intercalation agent, reaction time and temperature as factors. Firstly, the flake graphite was intercalated in the mixed acid system (phosphoric acid + nitric acid), and then the prepared sample was immersed in sodium dihydrogen phosphate solution for intercalation reaction again. Then, the sample was filtered to pH 6-7, dried and expandable at 1000 ℃, The expandable graphite prepared by this method has no sulfur, but its expansion volume is not too high. The reason is that the reaction between nitric acid and graphite is an exothermic reaction. The decomposition and volatilization of nitric acid at high temperature leads to the decrease of nitric acid concentration, and the nitrate ion that has been inserted into the interlayer also overflows the interlayer because of the volatilization and decomposition of nitric acid, resulting in the decrease of expansion volume.
Yao Yongping used hydrogen peroxide, nitric acid, and phosphoric acid as oxidation intercalation agents to prepare sulfur-free expandable graphite by chemical oxidation method through a series of processes including oxidation intercalation, filtration, drying, and expansion, The expandable volume of expandable graphite is 312ml / g; The sulfur-free expandable graphite was prepared by using concentrated nitric acid and acetic acid, 95% concentrated nitric acid and propionic acid, respectively. In the reported cases of preparation of sulfur-free expandable graphite, potassium permanganate and hydrogen peroxide are mostly used as oxidants, phosphoric acid, acetic acid, propionic acid, and other mixed acid solutions are used as intercalation agents, but the expansion volume is not too high, so the preparation of sulfur-free expandable graphite with high expansion volume is still the main research direction at present.
Under the action of strong oxidant potassium dichromate, xiuxiankai uses perchloric acid and concentrated nitric acid as the main intercalation agent, glacial acetic acid as the auxiliary intercalation agent, and takes advantage of the lower decomposition temperature of perchloric acid. Under the double oxidation of nitric acid and potassium dichromate, the optimal process is determined by orthogonal experiment, and the volume of expandable graphite is 375 ml / g; Wei Xinghai used nitric acid as the main intercalation agent and acetic anhydride as the auxiliary intercalation agent to prepare high expansion volume of 478 ml / g sulfur-free expandable graphite by orthogonal experiment. The characterization showed that acetic anhydride could be well intercalated between graphite layers under the action of strong oxidant, which was a good auxiliary intercalation agent; In the mixed oxidant system, Tian Alin prepared acetic anhydride phosphoric acid perchloric acid mixed acid intercalation agent in the order of weak acid to strong acid for graphite reaction. Acetic anhydride absorbed excess water in the reaction, greatly increased the concentration of H + in the solution, and further improved the oxidizability and oxidation rate of the reaction system, When m (flake graphite) ∶ V (mixed acid) ∶ m (mixed oxidant) = 1 (g) ∶ 4 (ML) ∶ 0.2 (g), m (potassium permanganate) ∶ m (potassium dichromate) = 1 ∶ 1, reaction at 50 ℃ for 60 min, drying at 40 ℃ for 2 h, and expansion at 500 ℃, 665ml / g sulfur-free expandable graphite was obtained The pore structure is rich, so it has high application value as adsorption material and graphene precursor material.
Through the experimental study of using hydrogen peroxide, perchloric acid, and phosphoric acid instead of sulfuric acid to prepare low sulfur and sulfur-free expandable graphite, the diversification of liquid phase materials is explained. The corresponding reactants can be selected according to the requirements of specific products. The order structure of interlayer compounds can be controlled by changing reactants and adjusting reaction conditions. At the same time, mineral-modified acid can be used instead of conventional acid The expandable graphite was prepared by mixed oxidant instead of single oxidant to improve the utilization rate of acid solution and the oxidizability of oxidant.

3. Factors affecting expansion volume
3.1 Purity and particle size of graphite
In the oxidation process of graphite, the chemical reaction can be carried out at the edge and between layers of graphite at the same time. If the graphite is impure or has too many impurities, it will cause lattice defects and dislocations of graphite, affect the diffusion speed and depth of chemical substances between layers of graphite, and can not form more interlayer compounds, thus affecting the expansion volume; In general, if the graphite particle size is larger, the interlaminar area is larger, and the number of overlapping layers is more, the amount of intercalation compound is more; If the particle size is too small, the specific surface area of graphite will be large and the interlayer pores will be small, which will hinder the insertion of the compound and affect the expansion volume.
Liu Rongrong used three kinds of expandable graphite with 50 mesh, 80 mesh, and 100 mesh to expand 0.7G each time in a 500 ml beaker. The results showed that the expansion volume was 357234180ml / g in turn. Through observation, it was found that there was basically no residue on the wall and bottom of the 50 mesh expandable graphite beaker, and there was a large amount of unexpandable expandable graphite on the bottom of the 100 mesh beaker, By observing its microstructure, it is found that the expandable graphite with the largest mesh is worm-like, thick and long, with large porosity, while the expandable graphite with the smallest mesh is short and fine. The reason for this phenomenon is that the expandable graphite with small particle size is small and denser, and the area that can be radiated by microwave is relatively small. Some expandable graphite can not be expandable, which leads to the decrease of expansion volume; Zhao Jijin used 50 mesh flake graphite and graphite powder to prepare expandable graphite under the same conditions. The particle size of flake graphite is larger than that of graphite powder, and the lower layer spacing is larger under the same oxidation, which can provide a more relaxed channel for the intercalation agent and reduce the intercalation resistance. The results show that the expandable volume of graphite powder is much smaller than that of flake graphite.
The results show that the pore structure characteristics of expandable graphite with different particle sizes are basically the same, but the winding space size, V-type cracking degree, and network pore size decrease with the decrease of particle size, The direct result is that the expandable graphite with larger particle size has larger expansion volume and more obvious vermicular shape. Therefore, in the relationship between graphite particle size, pore structure size, and expansion multiple, the influence of graphite particle size on graphite expansion volume is greater. The relationship between the particle size of flake graphite and the expansion volume of graphite is obtained by summing up the data of several kinds of literature.
Shi Shudong prepared expandable graphite by heating 50 / 80 / 100 mesh expandable graphite to 950 ℃. Under the same magnification scanning electron microscope, the microanalysis of expandable graphite with different mesh numbers was carried out. The results show that with the decrease of particle size of expandable graphite, the size of expandable graphite decreases correspondingly, and the morphology of expandable graphite changes from typical vermicular shape to irregular strip shape, Then the expandable graphite with different mesh numbers was mixed with paraffin to form composites, and the thermal conductivity of the composites was tested. The results showed that the density of 100 mesh eg / PCM composite was 15.8% higher than that of 50 mesh eg / PCM composite.
According to a large number of experimental research and actual production, the expandable graphite with the purity of more than 99% and particle size range of 30-100 mesh has good quality and high expansion volume. In addition, the graphite particle size should be uniform, that is, the particle size of the largest flake graphite particle should not be too different from that of the smallest particle so that the expansion effect is better.
3.2 Graphite intercalation method
The chemical treatment of graphite also has a great influence on its expansion effect. The traditional primary intercalation can not open the edge of graphite in time due to the insufficient concentration or content of oxidant, which affects the quality of intercalation. Therefore, some scholars have proposed a step-by-step intercalation method, that is, the second oxidation intercalation after the first oxidation intercalation, which can re-open the graphite edge, fully insert the intercalation agent, increase the content of the intercalation compound, and then increase the expansion volume.
Zhang Dawei washed the direct intercalation products to different degrees and then used phosphoric acid as solvent, (NH4) 3PO4, and app (ammonium polyphosphate) as intercalation agent to prepare expandable graphite by step intercalation method. After comparison, it was found that EV and aw (weight gain) increased before and after expansion, which strongly proved the formation of GIC (graphite intercalation compound), XRD results show that the intercalation agent with larger molecular weight can lead to the increase of graphite interlayer spacing. For the same intercalation agent, the larger the intercalation mass is, the larger the expansion volume is; Chen Wei used nitric acid and acetic acid, mixed acid of nitric acid, and phosphoric acid as intercalation agents to prepare EG1 (expandable graphite) with expansion volume of 116 ml / g and EG2 with expansion volume of 180 ml / G by direct intercalation method and step-by-step intercalation method respectively. SEM analysis showed that EG2 had a more developed pore structure and larger volume, which proved that the step-by-step intercalation method could reopen the graphite interlayer, The expandable volume of expandable graphite is better.
Using sulfuric acid (SA), phosphoric acid (PA), ammonium phosphate (AP), and ammonium polyphosphate (APP) as raw materials, Han Zhidong prepared direct intercalation expandable graphite and step-by-step intercalation expandable graphite by direct intercalation method and step-by-step intercalation method respectively, The expansion effect of expandable graphite with ammonium phosphate and sulfuric acid as intercalation agent is the best, and the weight gain of expandable graphite with ammonium polyphosphate sulfuric acid as intercalation agent is the largest. According to the experimental data, the relationship between intercalation mode and expansion volume is obtained.
This may be because the direct intercalation is that the intercalation agent is co intercalated into the same layer of graphite, while the step-by-step intercalation is not only co intercalated but also intercalated into the different layers of graphite, so the intercalation is more abundant. Due to the larger molecular size of the app, app (ammonium polyphosphate) – GIC has greater reaction weight gain and weight loss after expansion than AP (ammonium phosphate) – CIC, and the distance between graphite layers is also more significant. Therefore, the gas generated during thermal decomposition is more likely to overflow between graphite layers, resulting in a lower expansion range; The expansion volume of expandable graphite prepared by Zhao Jijin with the same raw material and method but changing the intercalation agent sequence is up to 450 ml / g, which is better than that obtained by direct intercalation. Finally, SEM analysis shows that high expansion volume is conducive to the attenuation of infrared radiation and millimeter-wave; Zhang Yingxin of Heilongjiang University of science and technology prepared expandable graphite with low temperature and high expansion rate by stepwise intercalation method with multiple factors as variables. The expandable volume was 407ml / g, which was much higher than 217ml / g obtained by the direct intercalation method.
3.3 Washing process
Due to the intercalation reaction, the residual acid on the edge and surface of graphite will not only hinder the formation of pore structure in graphite but also have adverse effects on equipment, such as corrosion. Therefore, the product needs to be washed after the reaction. Yang Yongqing studied the effect of washing temperature on the expansion ratio by washing the reactants prepared from sulfuric acid and hydrogen peroxide solution in the range of 0 ~ 100 ℃. Because the intercalation between graphite layers is easy to decompose under high temperature, it is easy to dissociate from the intercalation, so that the intercalation between graphite layers is reduced, and the vaporization is also reduced when the next step is heated and expandable, which leads to the decrease of an expansion force, and the graphite layer can not expand completely, thus affecting the expansion effect, The expandable graphite is more stable.
According to different experimental results, the relationship between washing temperature and expansion volume is obtained.

Guo Lei et al. Washed the expandable graphite to pH 1-2, 3-4, 5-6, and 7 at 0-20 ℃ to study the effect of pH on the volume of expandable graphite. When washing to pH 1-4, the vaporization only occurs at the edge of graphite flakes, resulting in incomplete expansion. When washing to pH 7, the intercalator overflows between layers due to too frequent exchange with deionized water, which will also affect the expansion volume. Only when the sample is washed to pH 5-6, the expansion effect is the best. According to the experimental data of Guo Lei.
3.4 Expansion mode
The traditional expansion method of expandable graphite is in a muffle furnace or resistance furnace. However, this expansion method has a long heating time and large power consumption in the initial stage. Besides, opening the furnace door at 800-1000 ℃ will cause irreversible damage to the furnace. In order to solve the above problems, the microwave method emerges.
Beata and others used the chemical oxidation method to obtain graphite interlayer compounds, and then the reactants were heated to 1000 ℃ and expandable by microwave respectively. According to the analysis of the expandable graphite, the properties of expandable graphite prepared by microwave method and high temperature 1000 ℃ were similar; Lai prepared 833ml / g and 613ml / g expandable graphite by microwave method with large scale graphite and fine-scale graphite as raw materials, which is much higher than that of traditional expansion mode. During the expansion process, the expansion time and heating power of large-scale graphite are larger than that of fine-scale graphite, Based on the advantages of the microwave method, it is more suitable for the expansion of graphite.
Qiu Ning used a high-temperature heating method, a common microwave equipment method (home microwave oven), and a special microwave equipment method (microwave graphene special furnace) to prepare worm graphite. According to the forming effect of worm graphite, it was found that the gap between the expandable graphite layers prepared by the high-temperature heating method and microwave method was not obvious, which was due to the uneven heat conduction, The structure of the lamellae is in a fragmentary state due to incomplete heating between the layers. After absorbing microwave energy, the graphite layer rises rapidly from inside to outside, and the heating is even, and the lamellar structure increases obviously. The obtained graphite worm has obvious advantages in volume, specific surface area, and micromorphology, and the expansion time is shorter, among which the special microwave equipment method has the best effect; Zhang Dong et al. Measured the expandable graphite prepared by microwave and expandable graphite prepared by high-temperature electric furnace method by mercury pressure method respectively. The results show that the pore structure of expandable graphite prepared by the two methods is very different. The former is basically a nanometer scale, and the latter is between nanometer and micron.
Based on the good conductivity of graphite, the microwave method usually expands 30-40 S. the heating effect is fast and strong, which greatly shortens the preparation period. However, it has a strong dependence on microwave equipment. The quality of expandable graphite will be determined by the performance of microwave equipment. Moreover, the pore size distribution of expandable graphite is very small, which is basically nanometer grade, and the yield needs to be improved.
3.5 Expansion temperature
The expansion volume of expandable graphite is usually 300 ml / g at 800-1000 ℃. However, this method is not only time-consuming and costly but also causes the structure of intercalation to undergo ordered or disordered phase transition, which affects the expansion volume. Moreover, due to the high temperature, the application of expandable graphite in low-temperature flame retardant and other fields is limited. Therefore, it is of great significance to study the preparation process with higher expansion volume at lower temperatures.
After analyzing the process flow of the traditional mixed acid method, the effects of various factors on EV were systematically studied. The expandable graphite with the expansion volume of 460420 ml / g was obtained by using a new chemical mixed acid method in the system of kmno4-hno3-perchloric acid-glacial acetic acid and hno3-h2so4-cro3 at the expansion temperature of 180220 ℃, This method makes up for the shortcomings of volatile and poor intercalation quality when organic acid is used as intercalation agent, and obviously reduces the initial expansion temperature on the premise of ensuring high rate volume.
Because perchloric acid and acetic anhydride are easy to decompose at low temperature, the composite acid formed by perchloric acid phosphoric acid acetic anhydride can provide a good environment for intercalation reaction, which is conducive to the uniform mixing of reactants, The expandable graphite with expansion volume of 350 ml / g was prepared at 300 ℃. The graphite has good low temperature and high expansion performance; The initial temperature of the expandable graphite prepared by Zhou Danfeng with perchloric acid potassium permanganate as intercalation system is 110 ℃, and its expansion volume at 300 ℃ and 400 ℃ is 230 ml / g and 380 ml / g respectively; After that, sodium hypochlorite and ammonium polyphosphate were added on the original basis, and the expansion volume reached 360 ml / g and 590 ml / g at the same temperature.
Conclusion and prospect
At present, scholars at home and abroad have done a lot of research on the preparation of expandable graphite and made significant progress, but the main problem is to develop appropriate preparation methods, produce high-yield, low-cost and controllable graphite, and promote the industrialization of graphite, so as to make graphite and its products have a broader development in the future. Through the above analysis, we can draw the following conclusions
(1) The essence of the chemical oxidation method is to control or avoid the formation of edge compounds while the formation of intercalation compounds. Therefore, the selection of oxidant and intercalation agents is particularly important. Usually, the oxidant with strong oxidizability should be selected to fully open the graphite sheet, but its concentration and dosage should be controlled to avoid excessive oxidation; The choice of intercalation agent should follow the principle that the diffusion rate of intercalation agent into graphite layer gap is faster than the edge oxidation rate; If the particle size is too large, it is difficult for the chemical substances between graphite layers to diffuse to the deep. If the particle size is too small, the graphite edge reaction is obvious, which is not conducive to the formation of the intercalation compound. Therefore, it is necessary to select the more suitable flake graphite according to the actual production conditions and chemical treatment.
(2) There are many synthetic methods and puffing methods, and each has its own advantages and disadvantages, so we should choose the appropriate method according to the preparation requirements and the actual situation; Whether it is high-temperature expansion or low-temperature expansion, in order to ensure the quality of expandable graphite and prevent its crushing or incomplete expansion in the process of expansion, the expansion temperature must be controlled in an appropriate range, and it should not fluctuate greatly to ensure its uniform heating. Finally, the residence time of expandable graphite in the high-temperature zone should be accurately controlled, The residence time is usually 20-40 s; Compared with muffle furnace, the microwave method is more efficient, safer, cheaper, and more suitable for laboratory operation.