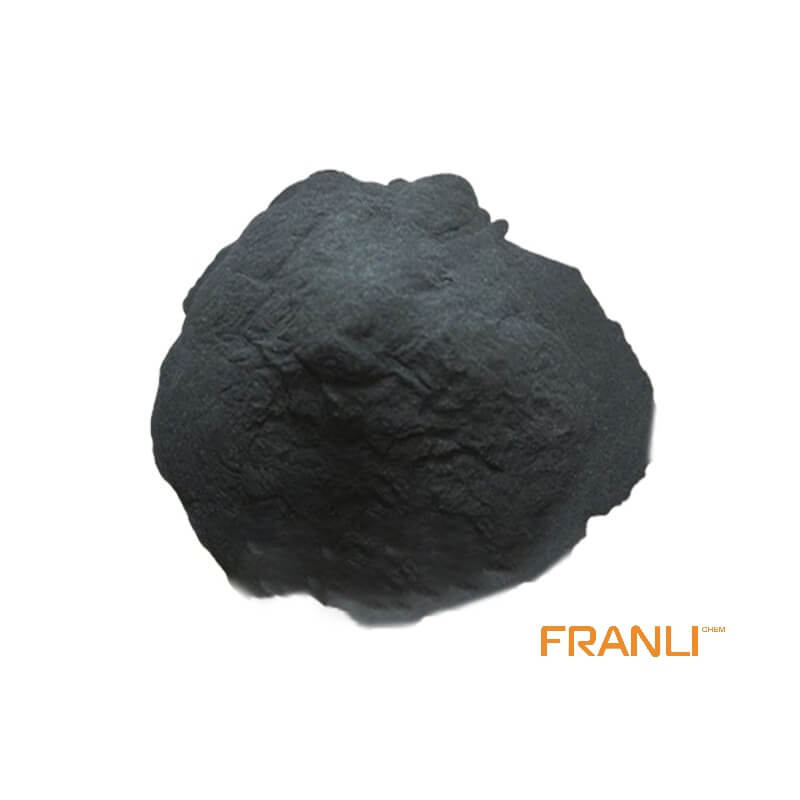
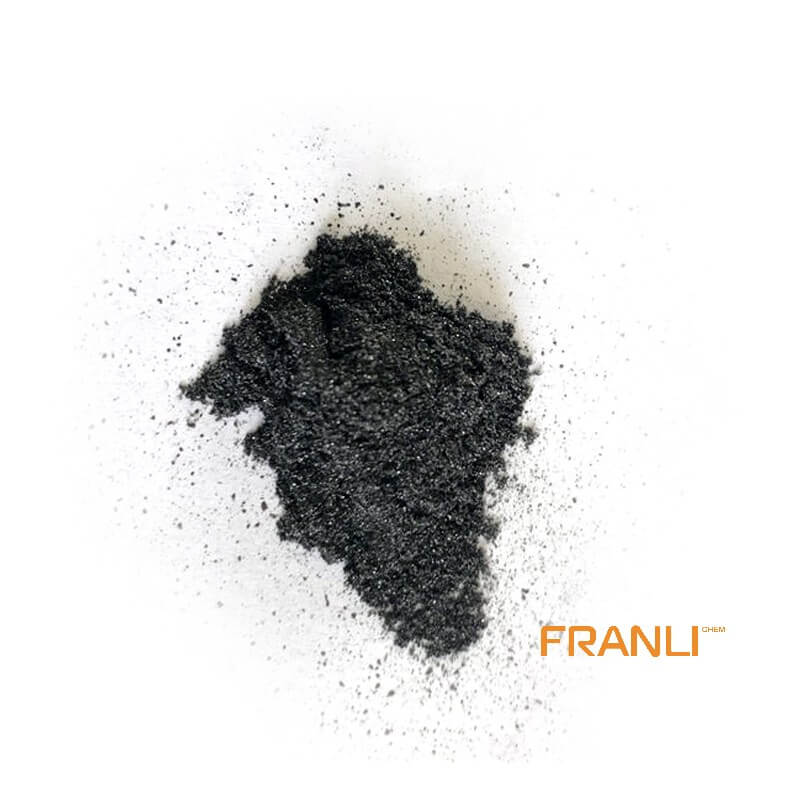
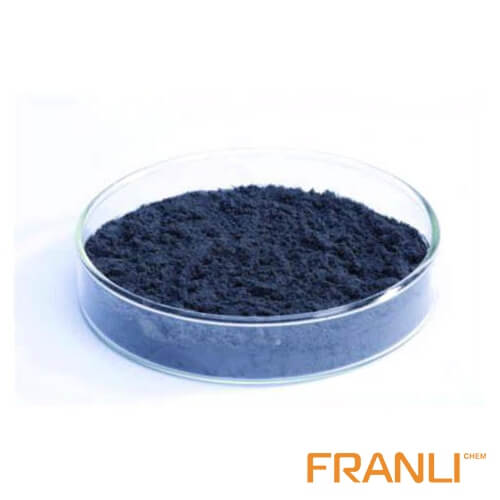
Expandable Graphite
Size
0.50mm or 0.106mm, etc
Package
25 kg small bags into ton bags
Origin
China
Features
Preservative/Electrical and thermal conductivity, etc.
Application
Fireproof sealing element, flame retardant, refractory brick, etc.
Expandable graphite crystal is a typical layered carbon material. Other heterogeneous particles such as atoms, molecules, ions, and even atomic clusters are inserted into the interlayer of crystalline graphite by physical or chemical methods to form a new layered compound, which is called graphite interlayer compound, namely expandable graphite.
Request a quote
Reading guide
A flexible expandable graphite bipolar plate is a kind of bipolar plate based on expandable graphite and modified by composite materials. It is derived from the type of composite bipolar plate and has a wide range of potential applications. It has been successfully applied in the fuel cell market. This chapter will introduce the molding process of the expandable graphite bipolar plate.
The bipolar plate is an important part of the fuel cell (PEMFC). In the process of fuel cell work, it is an important task to find new materials and processing methods of the bipolar plates with excellent performance and low cost.

At present, bipolar plates can be divided into graphite bipolar plates, metal bipolar plates, and composite bipolar plates according to the different matrix materials. Because composite bipolar plate overcomes the problems of poor mechanical properties, difficult processing, and poor corrosion resistance of metal bipolar plates, it has become a key research direction. Among them, flexible expandable graphite bipolar plate is a kind of bipolar plate that is based on expandable graphite and modified by material composite. It belongs to the type of composite bipolar plate which has wide application potential and has been successfully applied in the fuel cell market.
The following three aspects are introduced, including the molding materials, molding technology, and the existing problems.
1 . Molding material
Granular graphite bipolar plate: molding/filling / granular graphite composite. Using natural & synthetic graphite particles (D50 ~ 30-60) with high content (77-87 wt%) μ m) Large volume molding materials with carbon fibers are molded in thermosetting resins( Typical is epoxy/vinyl ester/phenolic / bismaleimide). 150-180 ℃ at 20-50 MPa, and the typical compression time is 1-5 minutes. The thickness of bipolar plate/web is similar to that of expanded graphite.
Expanded graphite: expanded graphite, also known as flexible graphite or worm graphite, is a new type of carbon material. expandable graphite has many advantages, such as large specific surface area, high surface activity, good chemical stability, and high-temperature resistance. The common preparation process of expandable graphite is to use natural flake graphite as material, first produce expandable graphite by the oxidation process, and then become expandable graphite by expansion treatment. expandable graphite material can instantly expand 150 ~ 300 times at high temperature, from flake to wormlike, so that the structure is loose, porous, and curved, the surface area is expanded, the surface energy is improved, the adsorption capacity of flake graphite is enhanced, and the wormlike graphite can be self embedded, so that the material has the functions of flame retardant, sealing, adsorption, etc Chemical industry, and other fields have a wide range of applications.
Material factors in molding:
① The resin ensures the high mechanical strength and airtightness of bipolar plate; During the molding process, the resin can be filled into the pores of expandable graphite rapidly under low pressure, and it can be mixed with expandable graphite fully and evenly.
② Conductivity: low conductivity of resin, adding carbon fiber, carbon nanotubes, and other auxiliary conductive materials to increase conductivity
③ Conductive materials: expandable graphite has advantages of flexibility, easy processing, and airtightness compared with natural graphite.
2. Molding process
(1) Preparation route: it can be divided into two types: direct molding and prefabrication plate molding
① Direct die expanded graphite
Bipolar plate material is formed by uniformly and fully mixing expanded graphite, polymer curing resin, and auxiliary conductive material, and then it needs to be cured. Compared with traditional graphite and artificial graphite, the direct molding of expandable graphite does not need additional secondary graphitization treatment, and the flexible expandable graphite has a good pressing and forming properties. In the process of pressing, additional polymer resin was added to mix with it to enhance the strength of the plate and improve the airtightness of the plate.
② Expandable graphite pressed by prefabricated plate
The bipolar plate is based on expanded graphite. It is made of a low-density flexible graphite plate by rolling. Firstly, expandable graphite is pressed into a low-density flexible plate, then the flexible graphite plate is simulated filled with polymer resin vacuum injection, and then the single-pole plate with flow channel is pressed, Finally, the polymer / expandable graphite bipolar plate can meet the practical environmental conditions is solidified in the oven. The method uses the continuous graphite phase of expanded graphite, which has excellent conductivity and good flexural properties.
Ballard uses expandable graphite as bipolar plate material, first, roll expandable graphite into the low-density flexible plate, then press to form a high-density plate, then vacuum impregnate polymer and oven curing, and finally prepare the expandable graphite bipolar plate with excellent performance.

(2) The process flow of the common expandable graphite bipolar plate
Natural graphite material expansion treatment flexible graphite plate preparation die pressing flexible graphite plate preparation single pole plate vacuum impregnation resin treatment hot pressing leveling plate screen printing adhesive bipolar plate bonding treatment plate edge cutting. The preparation, vacuum pressing, and impregnation of flexible graphite plates are the core of the whole process.
① The preparation process of the expandable graphite plate
The natural flake graphite material was used to prepare the compound between graphite layers by strong acid oxidation. The distance between layers of graphite was increased on the basis of the structure of the original continuous phase of graphite. Some characteristics of the original graphite were changed, and a kind of material with excellent softness and elasticity was formed.
The key to the preparation of expandable graphite is the formation of intercalation compounds, while in the chemical oxidation of natural flake graphite, the edge and interlayer areas of graphite are simultaneously carried out. In the early stage, the excess minerals in the raw materials are removed to ensure sufficient purity, and impurities will cause the defects of graphite lattice and dislocation, which will affect the conductivity.
The graphite particle size is too large in general, which shows that the formation of interlayer compounds is not enough; The size of graphite particles will lead to the rapid oxidation of graphite edge, which is not conducive to the formation of interlayer compounds. The number of graphite particles screened is usually about 80-200 mesh.
The intercalator and flake graphite are mixed evenly and fully reacted in proportion. The intercalator can control the formation of intercalators, reduce the formation of edge compounds, and then achieve expansion. Commonly used intercalators are nitric acid, sulfuric acid, potassium permanganate, etc. After the oxidation reaction of graphite is sufficient, the residual intercalator is removed through deamidation, washing, and drying, and the corresponding antioxidants are added to prevent the graphite from oxidation under high temperatures. The dried graphite was placed at 800-1200 ℃ for high-temperature expansion, which made the graphite intercalation compound decompose rapidly. The space between layers was enlarged by the thrust of decomposition, and the final shape of the vermicular graphite strip was 1-2cm.
② Vacuum pressing
The main content of the pressing is to press the low-density flexible graphite plate into the high-density plate and print the corresponding channel structure. The flexible graphite is fluffy in a low-density state, and there are many holes and gas in the inner. In the process of pressing, in order to minimize the drum phenomenon caused by the accumulation of internal gas, the pressing molding should be carried out in a vacuum state as much as possible.
③ Impregnation modification
When the density of flexible graphite plate is very low, there are a lot of semi-closed holes in the plate, even some big holes. When the forming pressure reaches 100MPa, the density of the flexible graphite plate can reach 1.5g/cm3 or higher. The surface structure and the layered structure after opening can be observed by scanning an electron microscope. It is found that the surface is relatively smooth, with only a small gap, the semi-closed hole is obviously reduced and the airtightness is improved obviously.

There are still various kinds of micropores in the inner part, which still directly affect the airtightness of the plate; On the other hand, the mutual engagement between the worm graphite is difficult to bear the bending strength of the structure, which is easy to lead to crack, tear and destructive damage. Therefore, the sealing and mechanical properties of the plate need to be improved than the impregnation and injection process.
The formed flexible bipolar plate was placed in vacuum immersion irrigation, and the resin solution which needed to be impregnated with glue was prepared in proportion; Vacuum extraction is carried out. After the pressure in the tank reaches the set value, stop vacuuming and open the valve of the impregnation solution. Close the infusion valve when the set liquid level is reached, and then press the impregnation, and the pressure is set at about 1.5MPa. The immersion time is determined by the type of impregnator. After the immersion, the pressure will be reduced to 2.0 bar. The valve will be immersed in the hydraulic back to the reservoir. Then the graphite plate was cleaned, dried, and cured.
3 Existing problems
Although expandable graphite has been successfully applied in the fuel cell field, there are still some technical problems in the process of direct molding or pre-pressing and injection of glue to prepare expandable graphite bipolar plate
(1) The expansion graphite bipolar plate was prepared by direct molding. The mixing of expandable graphite and resin is the most important part of the molding process. Traditional dry mixing is to mix expanded worm graphite and resin particles through screw extrusion or three-dimensional shaker evenly, which will result in the local concentration of resin particles because the density of resin particles is much greater than that of expandable graphite powder. The resin and graphite are mixed by grinding method, but this method is to destroy the loose structure of expandable graphite by shear force, so that the graphite worm is crushed, thus losing the use-value of expanded graphite.
(2) Natural graphite consists of hexagonal arrays or layers of carbon atom networks. The laminated structure of graphite, which is composed of carbon atoms connected by weak van der Waals force, has great differences in-plane and vertical plate plane. In order to solve this problem, it is necessary to add some auxiliary materials to the pre-expansion process to change the ordered structure of the expandable graphite worm and enhance the conductivity and thermal conductivity of the plate in the vertical direction.