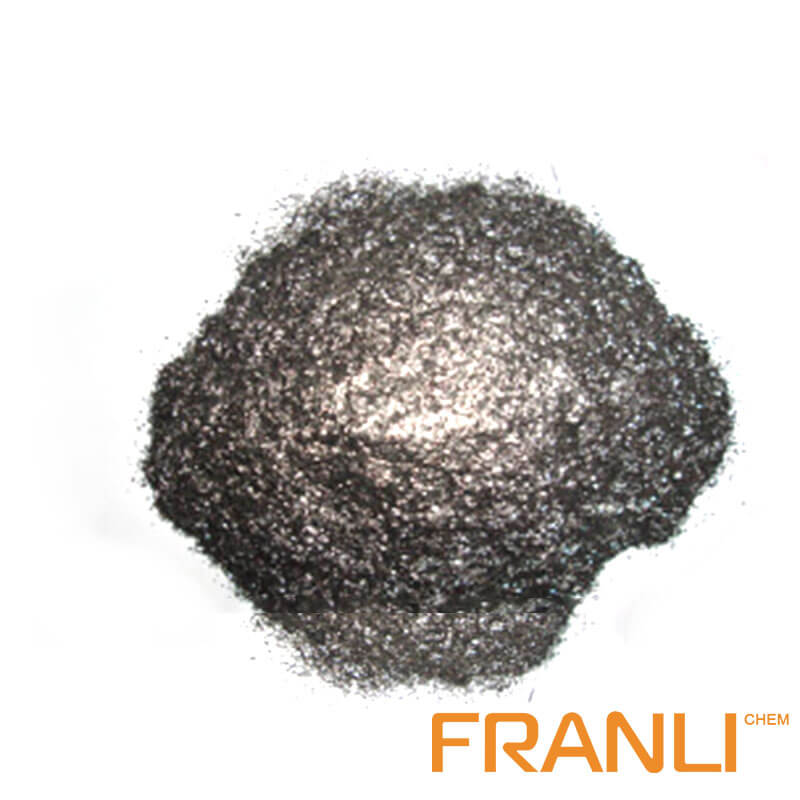
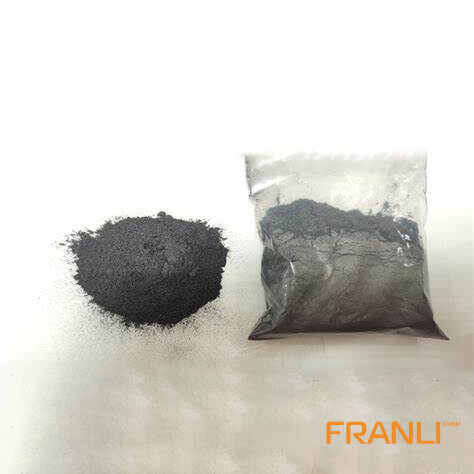
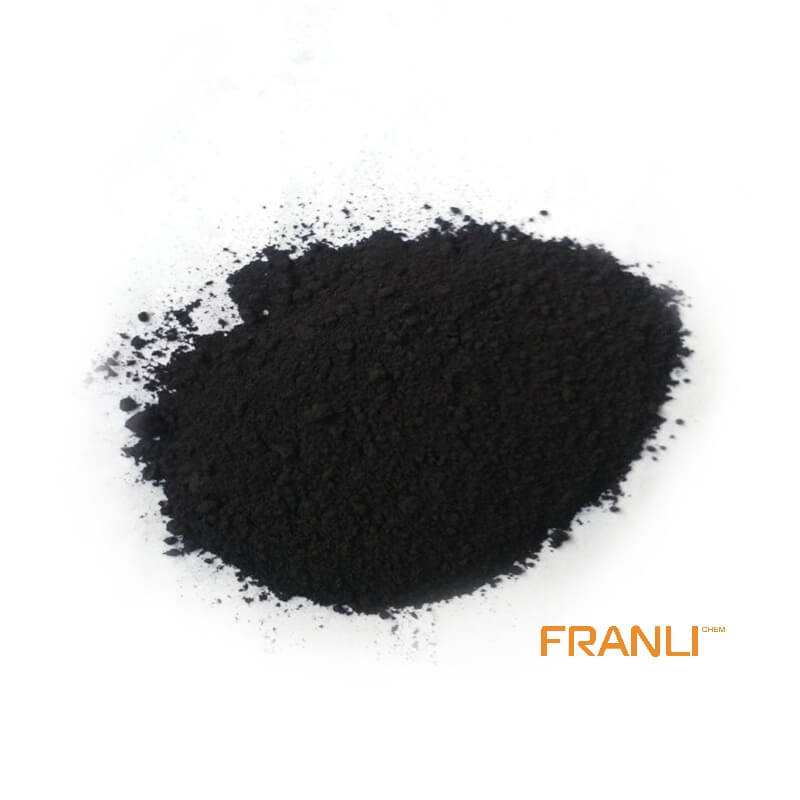
Flake Graphite
Size
0.01mm
Carbon Content
99%min
Package
25kg small bags into ton bags
Origin
China
Features
thermal shock resistance, lubricity, conductivity and plasticity…
Application
Lead battery plates positive and negative conductive agent, lithium batteries nickel hydrogen etc
Natural flake graphite has superior physical and chemical properties and is widely used in metallurgy, coatings and refractory industries. It is an important non-metallic raw material that is indispensable for today’s high-tech. Flake graphite is divided into large flake graphite and fine flake graphite according to the size of its scales. Usually, large flakes refer to +32 mesh, +50 mesh, +80 mesh, and +100 mesh flake graphite.
Request a quote
Introduce the distinction of natural flake grapihite and man-made graphite and advantage and disadvantage above all. natural flake graphite is divided into flake graphite and earthen graphite. The first-coulomb efficiency of flake graphite in lithium battery is 90%~93% and reversible capacity is 340~370mAh/g, so flake graphite is the most mainstream anode material. However, natural flake graphite has a regular layered structure, lithium-ion embedding speed is very slow, and due to the high anisotropy of the material, it is easy to lead to inadequate contact between the active substance and the collector, resulting in poor natural flake graphite ratio performance.

Artificial graphite is the petroleum coke, needle coke, asphalt, etc., calcined at a certain temperature, and then crushed, molding, grading, high-temperature graphitization, and other processes of graphite materials; With needle coke, attracts the most attention of needle coke is a kind of has obvious fibrous structure carbon materials, in a long-axis direction parallel to the particle has excellent electrical conductivity and thermal conductivity, and thermal expansion coefficient is small, easy graphitization, artificial graphite on capacity is close to or even surpass natural flake graphite, but the first-coulomb efficiency is low, and the preparation of the high cost.
In the process of graphite anode material preparation, the ball milling process can obtain better intercalation dynamics and electrolyte permeability, thus increasing the battery rate performance. But if the process is not precisely controlled, it can also have a detrimental effect on battery capacity and stability. Firstly, ball milling can increase the irreversible capacity of the battery’s first cycle and the electrolyte loss resulting from the increase of specific surface area, which leads to the formation of a solid electrolyte interface (SEI). Secondly, the higher the specific surface area of graphite anode is, the lower the interlayer bonding force is, and the ball milling process will reduce the stability of graphite particles during lithium-ion intercalation, leading to the graphite material falling off from the collector. Therefore, for different graphite anodes, only with the most appropriate ball grinding process, to obtain the best particle size, balance the advantages and disadvantages of the above.
However, the ball milling model, the number and mass of balls, the rotation speed, the mass and volume of ball milling materials are different among different research groups, so it is difficult to make a horizontal comparison and find the most suitable ball milling process. To find a possible comparison, Bartosz Hamankiewicz and Andrzej Czerwinski of the University of Warsaw, Poland, reported a method for calculating the energy per gram of graphite ball milling as a general unit of measurement, comparing the effects of various ball milling processes on battery performance. The optimum ball milling mode of natural flake graphite and artificial graphite is obtained.
Ball grinding process setting: The Fritsch Pulverisette planetary ball mill is used, grinding vials are made of zirconium dioxide, ceramic grinding balls are used, artificial graphite is marked as GSM, natural flake graphite is marked as GNTM, all samples are ground according to 10 steps, each step lasts for 60 minutes, the rest in the middle is 20 minutes, the total grinding time is 10 hours. Mill speed: 100-900 RPM.
It is obvious that the sample morphology is different under different energy. When the ball milling energy is low, the particle morphology almost does not change, which is consistent with the theoretical calculation results. When the ball milling energy is below 0.16Wh/g, the graphite packing structure will not be destroyed. When the MSE increases to 4.58Wh/g, it is enough to destroy the particles and reduce their size from hundreds of microns to tens of microns, and the graphite surface becomes very rough. When the MSE is 21.7Wh/g, the macroscopic grain structure disappears and only a few microns long graphite sheets exist. With the increase of MSE to 125.9 Wh/g, the size of the graphite sheet decreases to less than 1μm.
In the Raman spectrum, there is a narrow peak corresponding to the G peak of SP2 hybridization at 1580 cm-1 for good graphite structure, and the D peak corresponding to SP3 hybridization at 1350 cm-1. As can be seen from the figure above, almost all G peaks are located at 1580 cm-1. And with the increase of ball grinding speed, the intensity of the D band is strengthened. Disorder increases in graphite.

The value of IG/ID increases rapidly at 20-30 Wh/g, while the change of IG/ID is not significant at higher energy. At the highest ball milling energy, the crystal size (La) of GNTM and GSM samples is ~24 nm and ~21 nm, respectively, and the ball is milled at the highest energy. Compared with GNTM samples milled at the same energy, GSM samples have a higher structural disorder.
The ball milling process has a significant impact on the electrochemical performance of graphite materials. The figure above shows the comparison of the specific capacity of GSM and GNTM materials after the fifth and 100th laps. It can be seen that the capacity of the two materials is similar before ball milling, but with the increase of ball milling energy, the electrochemical behavior changes of the two materials have a big gap. At lower ball milling energy, the capacity of artificial graphite is greater than that of natural flake graphite, because natural flake graphite tends to form thin and flat sheets that spontaneously align in parallel, which makes the base surface of graphite in contact with the electrolyte rather than the edge surface; However, the diffusion rate of lithium ions through the base plane (8.7*10-12 cm2/s) is 6 orders of magnitude lower than that through the edge plane (4.4*10-6 cm2/s), thus resulting in electrolyte and lithium-ion channel blockage at low ball milling energy.
The second message from the figure above is that the higher the ball milling energy is not the better. Once the graphite particle size is excessively reduced, its lamellar structure may be damaged, resulting in a reduction in its lithium storage capacity. Therefore, each graphite material has an optimal ball milling energy.
The optimum ball milling energy of artificial graphite is 21.7Wh /g, and that of natural flake graphite is 31.2Wh /g, when the irreversible capacity is the minimum.
In this paper, the influence of the ball milling process on anode material is analyzed from a problem that is generally recognized by academia and industry, and a quantitative formula is given. The most appropriate ball milling process parameters can be obtained by calculation without testing. However, in this paper, the model is based on the mechanism of ball mill machine running, did not take into account the ball mill material itself, thus calculating the ball mill is a valuation, not only affected by the experience of phi, but also under the influence of natural flake graphite and artificial graphite material itself, though by this model will be able to get an about parameters of ball mill, thorough process optimization is still a little not.