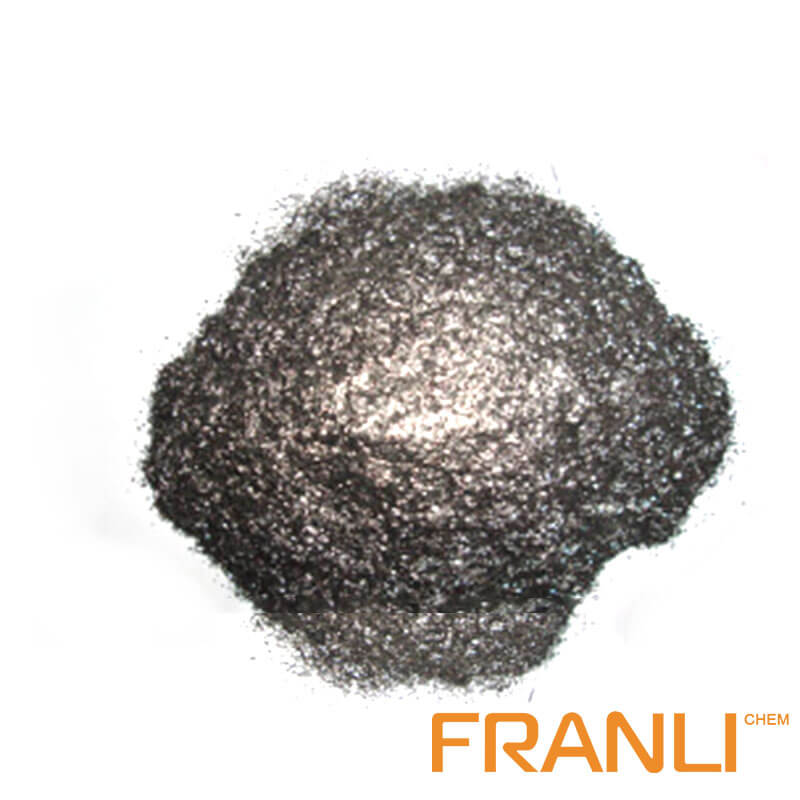
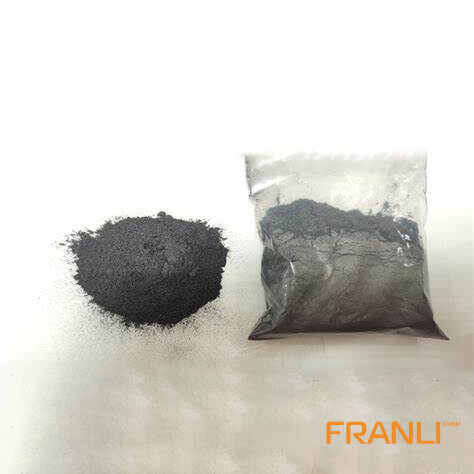
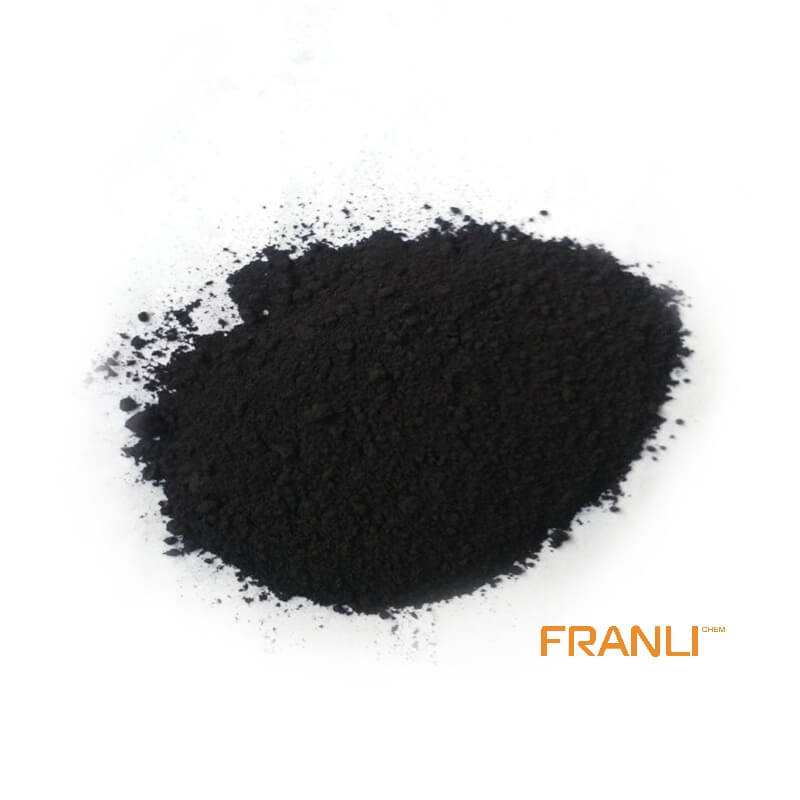
Flake Graphite
Size
0.01mm
Carbon Content
99%min
Package
25kg small bags into ton bags
Origin
China
Features
thermal shock resistance, lubricity, conductivity and plasticity…
Application
Lead battery plates positive and negative conductive agent, lithium batteries nickel hydrogen etc
Natural flake graphite has superior physical and chemical properties and is widely used in metallurgy, coatings and refractory industries. It is an important non-metallic raw material that is indispensable for today’s high-tech. Flake graphite is divided into large flake graphite and fine flake graphite according to the size of its scales. Usually, large flakes refer to +32 mesh, +50 mesh, +80 mesh, and +100 mesh flake graphite.
Request a quoteNatural flake graphite is a kind of high-quality refractory material, but it is difficult to prepare uniform and dense amorphous refractory due to the strong hydrophobicity of the graphite surface. In order to make graphite widely used in refractory materials, it is necessary to modify the surface of graphite to change from hydrophobicity to hydrophilicity. Generally speaking, surface modification is mostly used to modify the surface of the powder. This paper introduces a variety of graphite modification methods.

First, the wettability of graphite and its application limitationsr
The surface tension of graphite is small, there is no defect in a large area, and there are about 0.45% volatile organic compounds on the surface of graphite, which all deteriorate the wettability of graphite. The strong hydrophobicity of graphite surface worsens the fluidity of castable, and graphite is easy to aggregate rather than disperse evenly in refractory, so it is difficult to prepare uniform and dense amorphous refractory.
The microstructure and properties of graphite after high-temperature sintering depend largely on the wettability of high-temperature silicate liquid to graphite. When wetting, silicate liquid phase under the action of capillary force, into the particle gap, by the adhesion between them to bond the flake graphite particles, forming a layer of film around the graphite, cooling after the formation of the continuum, and the formation of high adhesion interface with graphite. If the two are not wetted, graphite particles form aggregates, silicate liquid phase is confined in the particle gap to form an isolated body, it is difficult to form a dense complex under high-temperature sintering.
Therefore, it is necessary to improve the wettability of graphite in order to prepare excellent carbon refractories. In recent years, a great deal of surface modification of graphite has been studied and some progress has been made.

Two, the flake graphite surface modification method
1, Low-temperature calcination graphite
The flake graphite surface has 0.45% volatile organic compounds, which is one of the reasons leading to the decrease in wettability. The wettability of graphite can be improved after calcination at 300~400℃.
2, Surfactant modified flake graphite
Modification by surfactant method refers to the use of the special structure of surfactant, so that one end of the hydrophobic group adsorption on the surface of flake graphite, and the other end of the hydrophilic group points to water, so as to change the surface properties of flake graphite so that its hydrophilic is improved. Modification of flake graphite with surfactants is one of the earliest developed methods, which has the characteristics of low cost, simple process, and obvious improvement of wettability.
3, Broken body method
Flake graphite and other refractory materials are mixed evenly in a certain proportion and pressed into a blank body on a pressure machine. After roasting at a certain temperature, a dense and high-strength blank body is obtained. Then the blank body is broken into different granular materials, which are introduced into the amorphous refractory material to achieve the purpose of introducing more graphite.
4, Granulation
Flake graphite or other refractory materials for granulated core, namely “grain core”, under the action of external force, through the bonding force of binder, so that flake graphite or other refractory materials bonded on the surface of grain core, with the growth of grain core, finally become a certain density and strength of large particles.
Zhou Ningsheng introduced flake graphite into castable by crushing body method and granulated method. Compared with directly adding flake graphite into castable, the amount of adding water was significantly reduced, the fluidity was improved, and the degree of compactness was correspondingly increased. The cold and hot states are one to two times stronger than the latter. Graphite is introduced into castable by granulation method and broken body method, which can improve the problems of low density and poor filling property of graphite. These two methods are worthy of further study and discussion.
5. Spherification of flake graphite
Spherification refers to the application of external force on the flake graphite. When the flake is finely broken, the flake is bonded to each other or bent in the thickness direction, causing the flake diameter to decrease, the thickness to become larger and the flake becomes granular. At this point graphite gradually loses orientation because the diameter and thickness of the difference becomes smaller. After spherification, the specific surface area and surface energy of flake graphite are reduced, and the filling and dispersibility in castable are improved. However, the improvement of wettability of graphite by this method is limited and cannot meet the requirements of graphite use.

6. Strong acid treatment
Graphite powder was immersed in concentrated sulfuric acid, concentrated nitric acid or hydrofluoric acid and reacted at room temperature to 100℃ to change the surface of graphite particles into hydrophilic surface. However, it is difficult to remove the compounds left in the crystalline layer because of the acid component immersed in the crystalline layer of graphite and the cambium interlayer compounds. In the later construction, the acid component is dissolved in mud or mud water, so that the PH value changes and affects the performance of the material.
7, a Surface coating method
Flake graphite surface coating method refers to the use of physical or chemical methods to cover a layer of hydrophilic substances on the surface of graphite, such as oxides, metals, carbides, nitrides and so on with good wettability. This method can not only improve the hydrophilicity of graphite, but also improve the oxidation resistance of flake graphite through the coating layer on the surface of graphite, enhance the interface bonding strength between graphite and surrounding matrix or grain in the composite material, and reduce the density difference between graphite and other refractory materials through the adsorption layer of higher density. So the surface coating method is a promising method
The advantage of graphite surface coating method is that the surface coating can not only improve the wettability of graphite, but also improve the oxidation resistance of graphite, and enhance the bond strength between graphite and the surrounding matrix or crystal particles. However, the problem is that due to the weak binding force between coated particles and graphite master particles, the coated particles are easy to be desorbed from the graphite surface in the process of raw material mixing, thus affecting the modification effect.
Some progress has been made in the study of surface modification of flake graphite, but there is still a long way to go before practical application. In addition to developing new modification methods, it will be a developing trend to synthesize various modification methods at the same time.