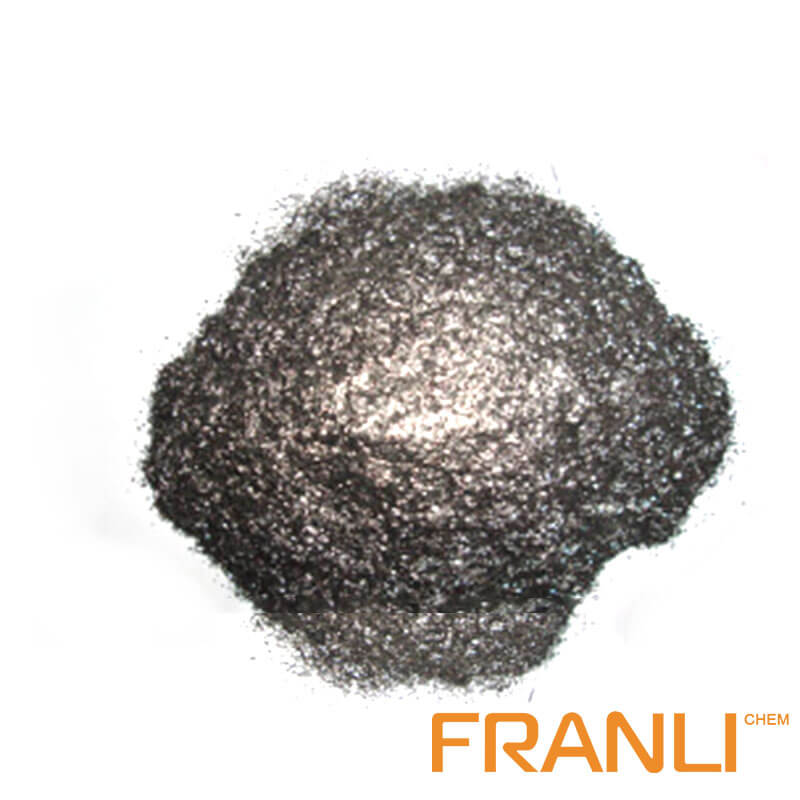
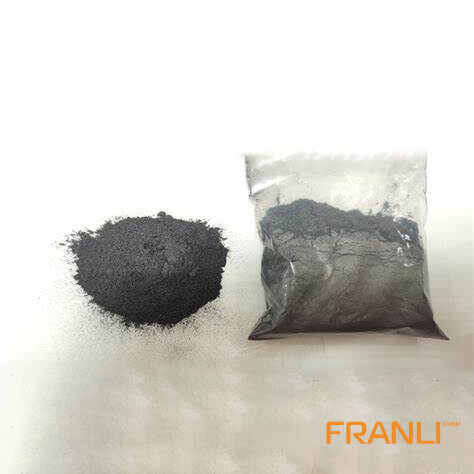
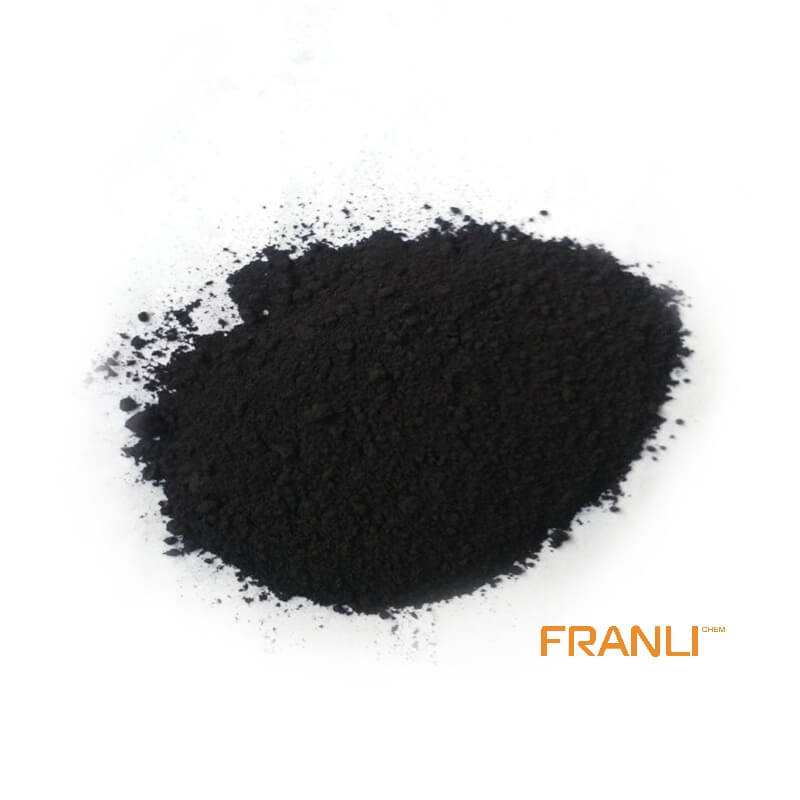
Flake Graphite
Size
0.01mm
Carbon Content
99%min
Package
25kg small bags into ton bags
Origin
China
Features
thermal shock resistance, lubricity, conductivity and plasticity…
Application
Lead battery plates positive and negative conductive agent, lithium batteries nickel hydrogen etc
Natural flake graphite has superior physical and chemical properties and is widely used in metallurgy, coatings and refractory industries. It is an important non-metallic raw material that is indispensable for today’s high-tech. Flake graphite is divided into large flake graphite and fine flake graphite according to the size of its scales. Usually, large flakes refer to +32 mesh, +50 mesh, +80 mesh, and +100 mesh flake graphite.
Request a quoteChina has the world’s largest flake graphite market. Graphite flakes are crystals formed by metamorphism under high pressure and appear flake-like. The Franli factory produces flake graphite with different carbon content standards. It has better plasticity than other types of graphite. great industrial value.
For quite a long time, flake graphite has been widely used in advanced refractory materials and coatings in the metallurgical industry. Such as magnesia carbon bricks, crucibles, etc. Desulfurization accelerator in the smelting industry, pencil lead in the light industry, carbon brush in the electrical industry, electrode in the battery industry, catalyst in the fertilizer industry, etc. Flake graphite is deeply processed and used in lubricants, mold release agents, wire drawing agents, conductive coatings, etc. It can also produce expanded graphite, which is used as raw material for flexible graphite products, such as flexible graphite seals and flexible graphite material products.

Classification of flake graphite
(1)According to the total graphite carbon content, flake graphite is divided into high purity graphite (carbon content ≥ 99.9%), high carbon graphite (carbon content 94.0% ~ 99.9%), medium carbon graphite (carbon content 80.0% ~ 94.0%) and low carbon graphite. Carbon graphite (carbon content ≤ 50.0% ~ 80.0%) has four categories.
(2) According to the size of flakes, flake graphite is divided into large flake graphite (>147 µm) and small flake graphite (<147 µm).
Flake graphite with different carbon content
(1) High-purity flake graphite (≥99.9) is used for melting chemical reagents, lubricant base material, flexible graphite sealing material, etc.
(2) High carbon flake graphite (94.0~99.9) is used in battery raw materials, brush raw materials, electric carbon products, refractory materials, lubricant base materials, pencil raw materials, fillers, coatings, etc.
(3) Medium carbon flake graphite (80.0-94.0) is used for battery raw materials, casting materials, casting coatings, refractory materials, crucibles, pencil raw materials, dyes, etc.
(4) Low carbon flake graphite (50.0~80.0) is suitable for casting coatings, etc.
Market demand for flake graphite
(1)Anti-corrosion material: chopped fiber material with good resistance to deformation and cracking is a solvent-free thick film conductive coating with functional filler. The coating has the characteristics of anti-corrosion medium penetration, low curing residual stress, good resistance to matrix deformation and cracking, stable construction performance, and long-term static electricity conduction. It can be used for electrostatic conductive coating on the inner wall of crude oil storage tanks. According to data reports, electroless plating technology is used to coat graphite powder with metals, such as copper, nickel, silver, etc. to prepare composite conductive fillers, which are used in conductive coatings in an amount of 30%, which not only has good electrical conductivity, but also has further corrosion resistance. improve.

(2)Thermally conductive material: It can be made into thermally conductive graphite paper. The greater the thermal conductivity, the better the thermal conductivity of the graphite paper. Flake graphite has good thermal conductivity, and its coefficient is related to humidity, temperature and pressure, structure, density and other factors.
(3)Conductive material: flake graphite can be directly used as carbon conductive filler or made into composite conductive filler for conductive paint. However, due to the large amount of graphite flakes added, the performance of the coating will become brittle and its application will be limited. Therefore, measures should be taken to further improve the conductivity of graphite and effectively reduce the amount of graphite flakes added. The domestic Tianhua Chemical Machinery Research Institute has developed a high-temperature corrosion-resistant resin as the base material and large flake solid graphite flakes with strong electrostatic conductivity as the main aggregate, with high body strength and good wear resistance.
(4)Wear-resistant material: With the increase of pressure, the wear rate and the friction coefficient of flake graphite will also increase rapidly. For different flake graphite-metal friction surfaces, in all cases, the higher the allowable pressure, the better the orientation of the graphite film formed on the friction surface. In the air medium with a temperature of 300 to 400 degrees, sometimes the friction coefficient increases due to the strong oxidation of flake graphite.
The Franli factory is accelerating the research and development of flake graphite processing technology, making breakthroughs in key technologies, and the development of strategic emerging industries, which puts forward higher requirements for the supply guarantee, scientific planning, development, and utilization of graphite resources. Optimize the technology in the field of flake graphite purification and deep processing, to provide various industries with more kinds of high-quality flake graphite, and develop my country from a country with large graphite resources to a powerful country in graphite manufacturing.