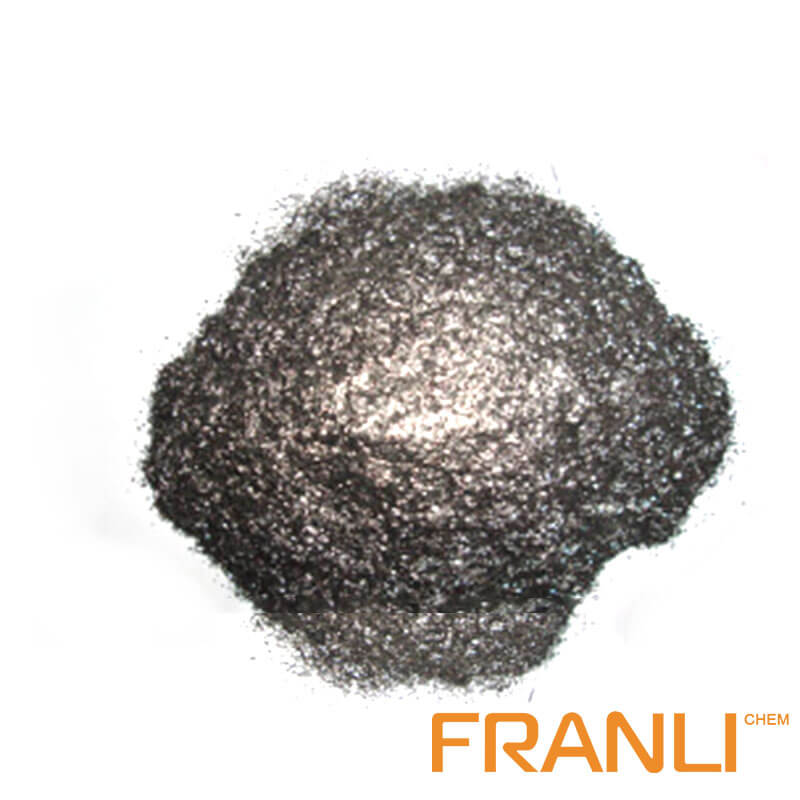
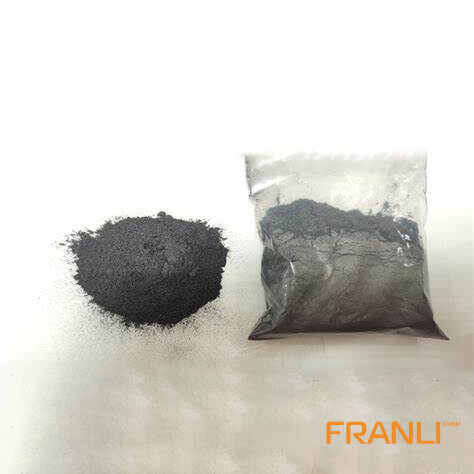
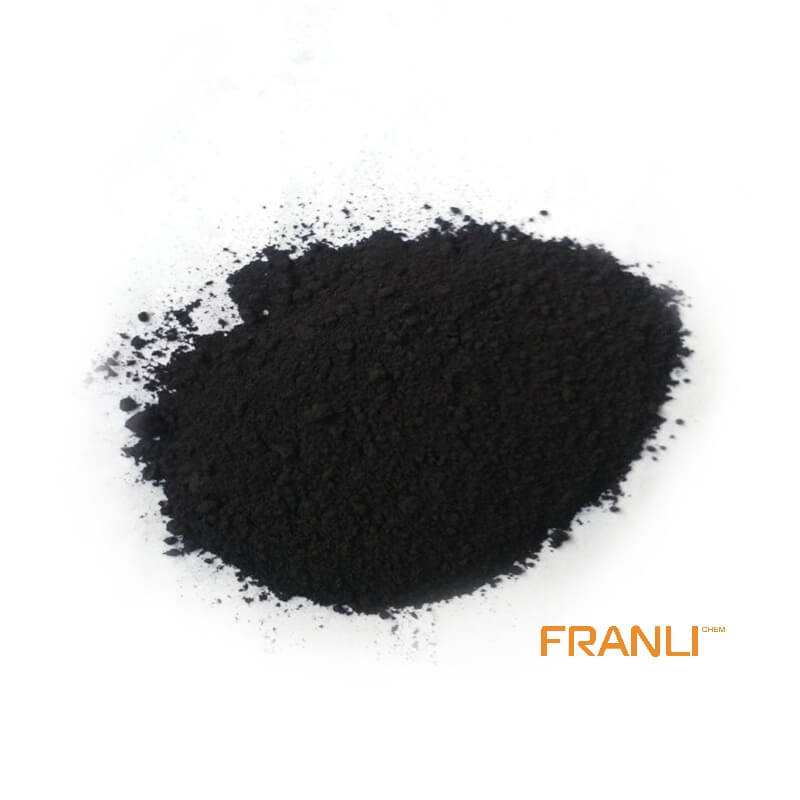
Flake Graphite
Size
0.01mm
Carbon Content
99%min
Package
25kg small bags into ton bags
Origin
China
Features
thermal shock resistance, lubricity, conductivity and plasticity…
Application
Lead battery plates positive and negative conductive agent, lithium batteries nickel hydrogen etc
Natural flake graphite has superior physical and chemical properties and is widely used in metallurgy, coatings and refractory industries. It is an important non-metallic raw material that is indispensable for today’s high-tech. Flake graphite is divided into large flake graphite and fine flake graphite according to the size of its scales. Usually, large flakes refer to +32 mesh, +50 mesh, +80 mesh, and +100 mesh flake graphite.
Request a quoteThe flake graphite is a kind of natural crystalline graphite. Graphite minerals are mined and purified. The general shape is fish scales, so it is called scale stone. Flake graphite has complete scale crystallization, thin flakes and good toughness, stable physical and chemical properties, good electrical conductivity, temperature resistance, lubrication, conductivity, thermal shock resistance, corrosion resistance, oxidation resistance, etc.
Why add flake graphite into magnesia carbon brick
Flake graphite is mainly used in refractory materials and metallurgical casting, conductive materials, lubricants, friction materials, etc.
In the graphite consumption structure, traditional industrial fields such as refractory materials and steel account for about 40%. Refractory castables have the advantages of convenient construction and easy repair, and have attracted widespread attention. However, their poor resistance to slag erosion and thermal shock also limits their development. Graphite and slag are non-wetting, and have good thermal conductivity and toughness. Therefore, in the preparation process of refractory castables, carbon materials such as flake graphite, carbon black, and carbon nanotubes are properly added to prepare carbon-containing refractory castables. Reduce its thermal expansion, and improve the slag resistance, thermal shock resistance, thermal conductivity, and impact resistance of refractory materials, which may prolong the service life of the furnace lining.
Factors affecting the quality of refractories
There are 5 factors affecting the end products with graphite
1. Purity of flake graphite
The purity of graphite is directly related to the high temperature flexural strength of magnesia carbon bricks and the melting loss rate during use. The high temperature flexural strength of magnesia carbon bricks increases with the increase of graphite purity. This is due to the difference in the microstructure of magnesia-carbon bricks. The magnesia-carbon bricks made of graphite with lower purity have a larger proportion of coarse pores (20 μm in diameter) after carbonization at 1000 ° C, and the porosity is also higher than that of magnesia-carbon bricks. Products made of high-purity graphite are high. This may be related to the high flexibility of high-purity graphite and its easy compression when making bricks. Another point is that the structure of magnesia-carbon bricks made of lower-purity graphite is locally weakened. After the magnesia-carbon bricks are treated at a sufficiently high temperature (such as 1600°C), the silicate minerals associated with graphite melt into a glass phase and combine with magnesia. Or the carbon reacts, causing the original mineral to be corroded, the volume is reduced, the contact area is reduced, and a pore zone is formed around the graphite, which leads to a decrease in the high-temperature strength of the magnesia-carbon brick as the purity of the graphite decreases.

2. Ash content
The greater the ash content of graphite, the lower the purity of graphite. The ash content of graphite is mainly composed of SiO2-Al2O3-Fe2O3–CaO and so on. Generally speaking, if the content of Al2O3 is high and the amount of other impurities is small, the refractoriness of ash will be high (about 1500~1600°C); if the content of Al2O3 is low and other impurities are large, the refractoriness of ash will be low (about 1250°C)
High SiO2 content in ash is very harmful. The SiO2 content in flake graphite is high, and the corrosion index of magnesia carbon bricks increases significantly. Generally, the SiO2 content in graphite should be limited to less than 3%. If SiO2 accounts for 50% of the ash, the graphite purity should be above 95%.
3. Flake Graphite particle size and shape
There is a direct relationship between the particle size of graphite and the oxidation temperature. Large flake graphite usually has high purity and good oxidation resistance. At the same time, large flake graphite can significantly improve the thermal shock stability of magnesia carbon bricks. Large flake graphite can also optimize the mixing and forming properties of the mixture. But the price of large flake graphite is higher.
In terms of graphite shape, the thinner the flakes, the better. Flake graphite first significantly improves the thermal shock stability of magnesia carbon bricks. This is because the modulus of elasticity of products made of flake graphite is lower than that of magnesia-carbon bricks made of ordinary graphite; at the same time, in the case of the same amount of graphite added, the dispersion of flake graphite is better, thereby improving the product. matrix, the number of obstacles to crack propagation increases during thermal shock. Secondly, the oxidation resistance of magnesia-carbon bricks made of flake graphite is also high, because the oxidation resistance of magnesia-carbon bricks made of flake graphite is also high, because the effective area of oxidation at the end of flake graphite is small. In the batching system, the smaller the size of the refractory aggregate, the better the effect of using flake graphite.
4. The amount of flake graphite added
In magnesia refractory materials, adding a certain amount of graphite is beneficial to improve the corrosion resistance and slag penetration resistance of the product. According to calculations, 3%~4% carbon in refractory materials can effectively prevent slag from penetrating into bricks. But carbon is easy to be oxidized, and its actual addition amount should be more.
When determining the amount of graphite added in actual production, it should be determined according to the conditions of use of carbon-bonded refractories, such as the type of smelting equipment, oxygen partial pressure in molten steel and slag, slag characteristics, smelting temperature and tapping temperature, etc.; it can also be based on Whether the produced product emphasizes corrosion resistance or thermal shock stability, or requires high strength or oxidation resistance determines the amount of graphite added.
The Franli plant mainly produces flake graphite, which has a unique high-stability structure and excellent long-cycle performance, which is particularly suitable for use as refractory material. Flake graphite in the field of refractory, can improve slag resistance, thermal shock resistance, thermal conductivity, and impact resistance of refractory materials may prolong the service life of the furnace lining.