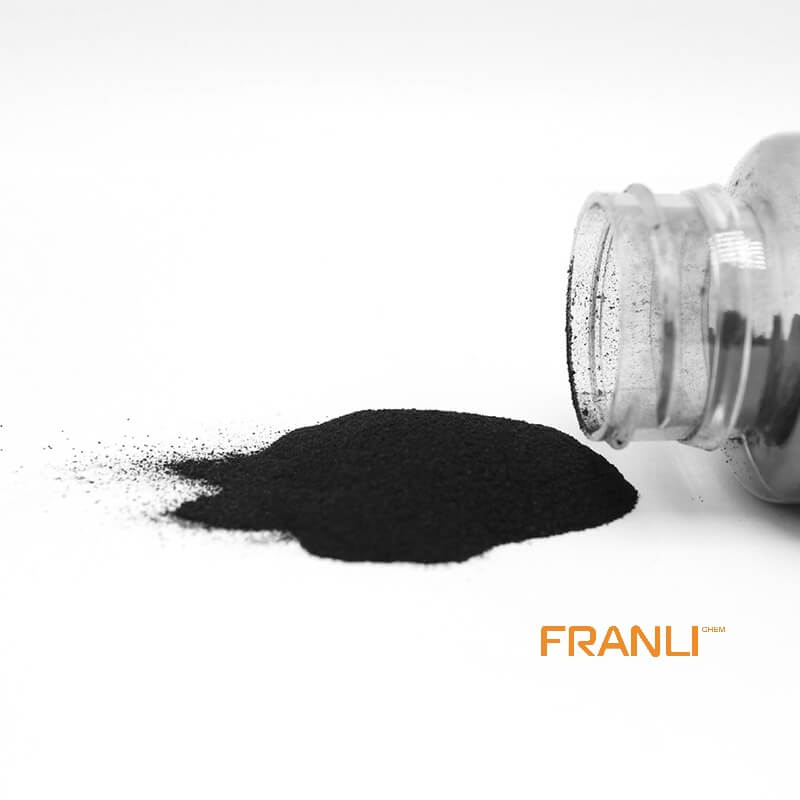
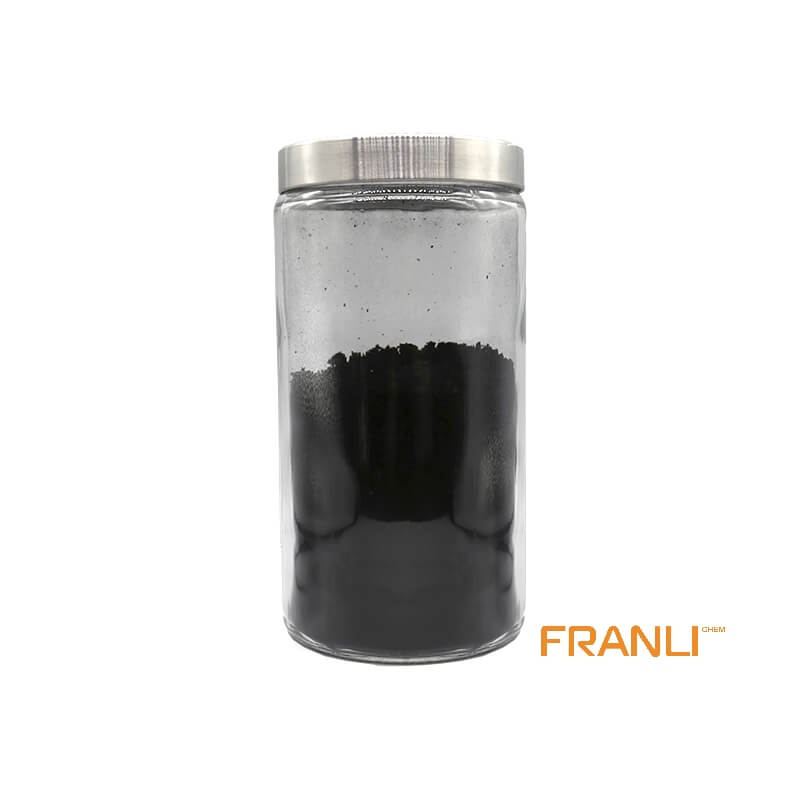
Graphene
Size
1-2nm thick x 0.5-5microns wide
Package
According to customer requirements
Features
High strength, high electrical conductivity, etc.
Application
Can be used as filler(between 0.01% and 5%).
Graphene, as the thinnest, toughest and best conductive nano material found at present. It is a two-dimensional crystal composed of carbon atoms stripped from graphite material with only one layer of atom thickness. Known as “black gold”, it is “the king of new materials”. Scientists even predicted that graphene “will completely change the 21st century”.
Request a quoteThe product launched by the Franli factory – graphene, it not only has super anti-corrosion, but also has super hydrophobicity, thermal conductivity, electrical conductivity, graphene modified anti-corrosion coating has a good anti-corrosion effect, can play a protective role for metals, plastics, etc., with a good effect,
Graphene usually reflects its anti-corrosion performance in coatings, plays a role in anti-corrosion for metals, etc., and protects the life of non-ferrous metals; Heavy anti-corrosion coating refers to a class of anti-corrosion coating that can be applied in a relatively harsh corrosive environment and has a longer protection period than conventional anti-corrosion coating.

Physical mechanism of graphene corrosion protection
Graphene is how to show its functions in anti-corrosion. Due to the superposition and staggered arrangement of the sheet structure of nano-scale graphene, a “labyrinthine” shielding structure can be formed in the coating, forming a shielding barrier. In this way, the infiltration, penetration and diffusion of corrosive media can be effectively inhibited, and the physical barrier property of the coating can be improved. At the same time, it can also extend the permeation and diffusion path of corrosive media; This provides the penetration resistance and longevity of the coating.
Graphene has good physical barrier to small molecules: the volatilization of solvents during the film formation process of the coating may lead to defects such as micropores and pinholes in the coating, which makes the coating permeable to corrosive media. As a nanomaterial, graphene can be filled into the tiny defects of the coating after being used as a modified anti-corrosion coating, reducing the porosity of the coating, enhancing the compactness of the coating, and further delaying or preventing corrosion factors from leaching into the surface of the substrate.
Graphene conductive mechanism
Franili factory found that graphene and zinc powder form an effective micro-conductive cycle, so as to effectively ensure that zinc powder as an anode to play a protective role. Protect the cathode while protecting the properties of the paint from corrosion, thus achieving corrosion protection under low zinc conditions. Because the external anti-corrosion coating contains a large number of conductive particles, thus forming a smooth micro-conductive path, under the erosion of the corrosive medium, oxidation reaction occurs and electrons are lost. At present, in the traditional anti-corrosion coatings, the vast majority of primers use zinc powder as an additive. However, with the extension of the corrosion time, the zinc powder in the coating due to the oxidation of the conductivity decreased, it is possible to block the electron transport path, graphene due to excellent conductivity. Therefore, Graphite, which show a tremendous function in it.

Graphene hydrophobic mechanism
Because graphene has strong hydrophobicity, this makes the coating surface form a water barrier, so that water molecules in the air are not easy to enter the metal surface, thereby enhancing the protection of the metal and making it not oxidized.
Other applications of graphene in coatings
Graphene is extremely suitable for coating industry.
(1) Fireproof coating: graphene can be crosslinked and compounded with the resin in the coating to further form a dense protective film to block the air, thereby exerting the effect of flame retardancy.
(2) Antifouling coating: Mainly by adding heavy metals and other toxic materials to the coating, a toxic surface layer is formed on the surface of the coating film, and the marine life attached to the hull coating film is killed, so as to prevent marine life from adhering to the bottom of the ship or marine underwater facilities. Graphene has extremely high surface energy and strong hydrophobicity, and it is difficult for microorganisms to grow or adhere to the surface of graphene.
(3) Conductive coating: additive conductive coating is achieved by adding conductive substances to the coating, which are usually metal powder and graphene powder.
The Franli plant found that the cost increase after adding graphene was far less than the preservation benefits it bring. Low coating thickness, high adhesion, light film weight, excellent salt spray resistance and other advantages, is a good upgrade alternative to traditional anti-corrosion coatings, so graphene is expected to become a good upgrade alternative to traditional anti-corrosion coatings.