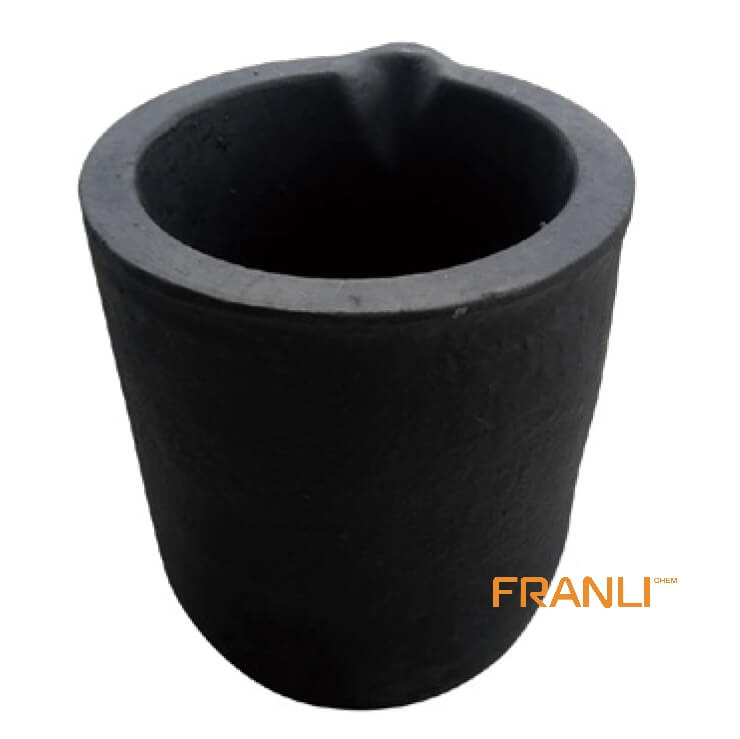
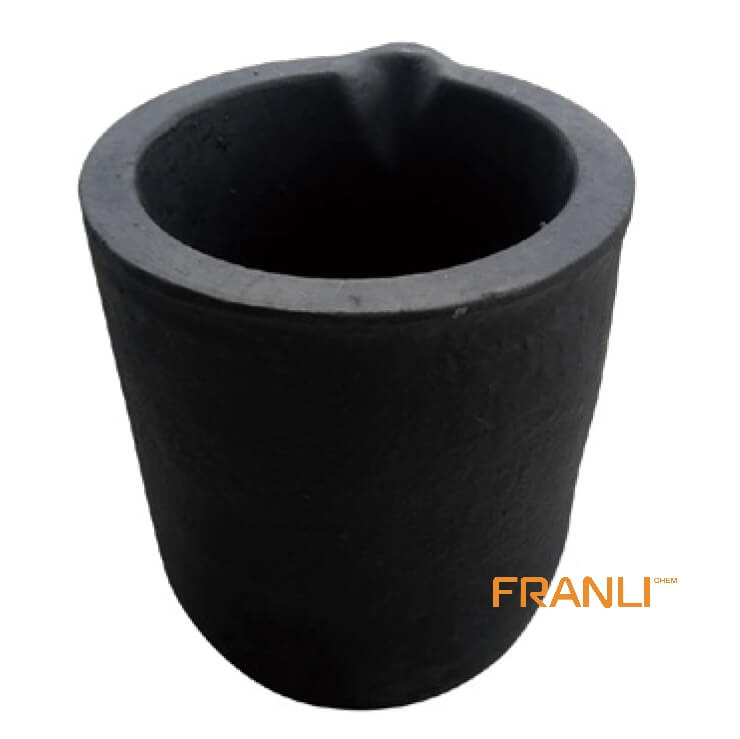
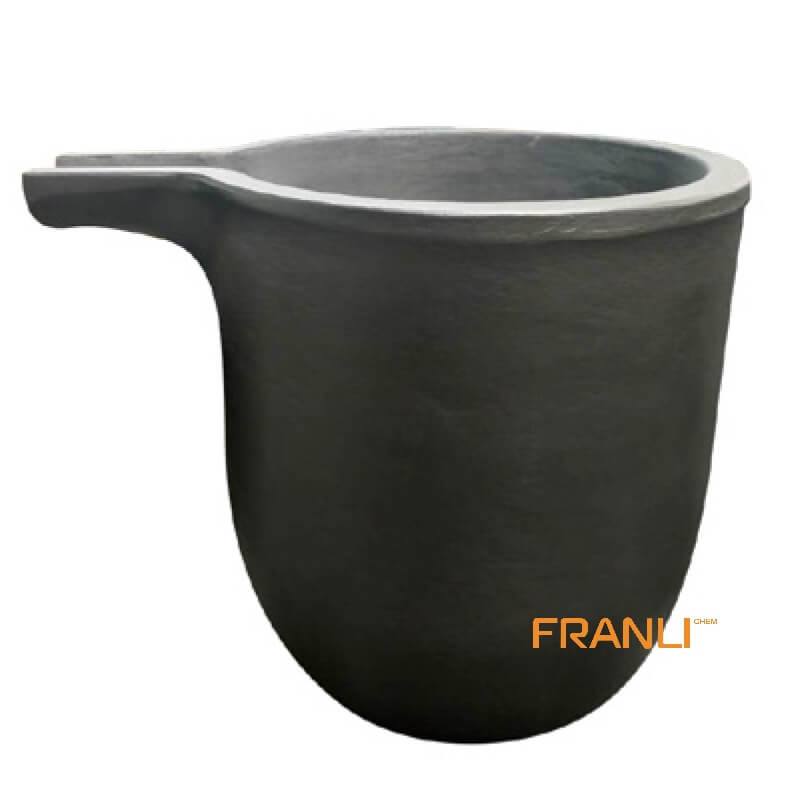
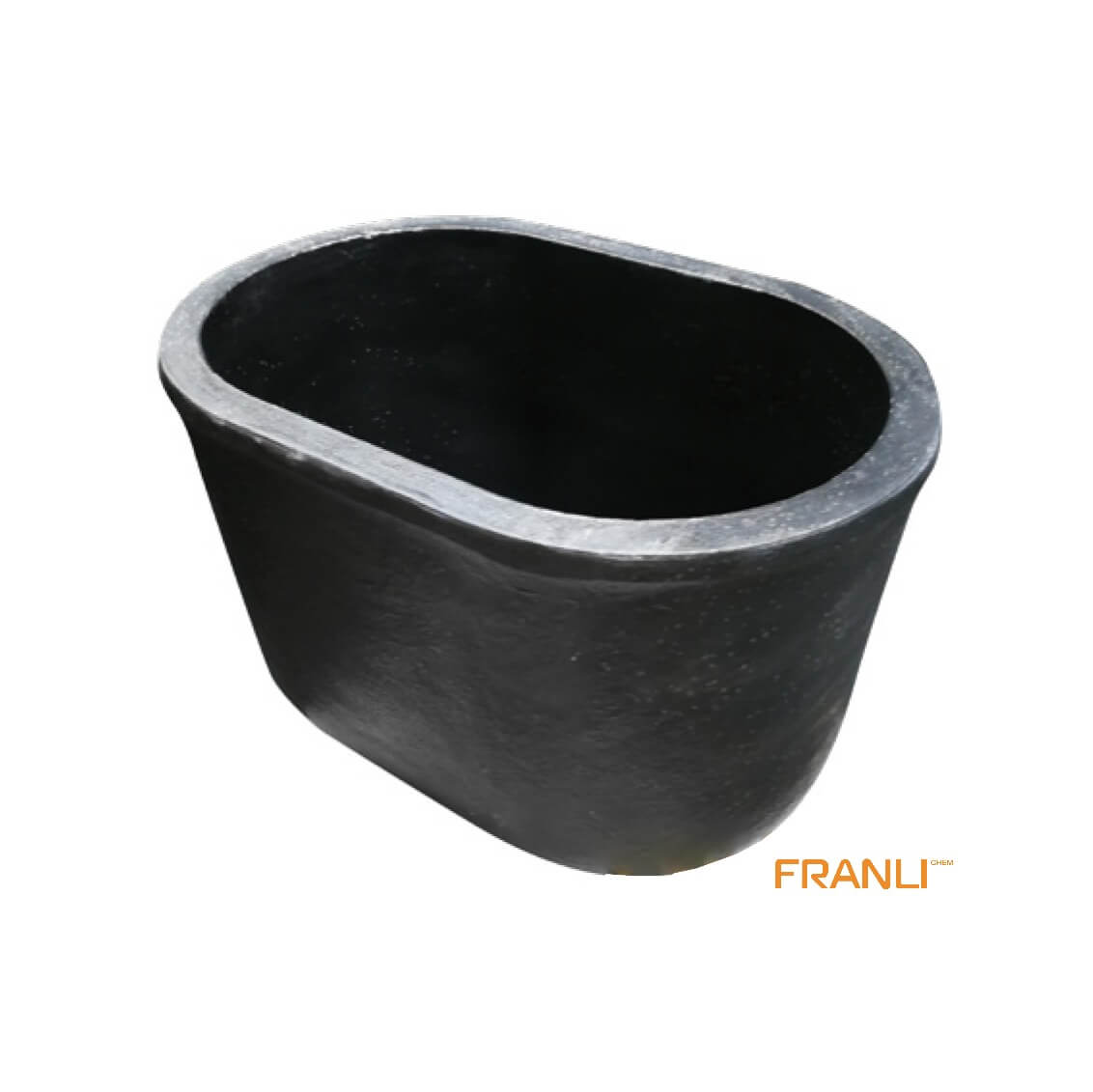
Graphite Crucible
Size
Different size is available, can be customized
Carbon Content
SiC graphite crucible, Spouted crucible, Inductor crucible, Elliptical crucible(U-shaped Crucible)
Material
Graphite and Silicon carbide
Working temperature
400-1600℃
Melting Metal
Aluminum, Copper, Brass, Bronze, Silver, Tin, Zinc, etc
Features
High density, high strength, dense uniform and defect-free.
Package
Wooden box
Graphite crucible is made of natural flake graphite as the main raw material and plastic refractory clay or carbon as binder. It has the characteristics of high temperature resistance, strong thermal conductivity, good corrosion resistance and long service life. It has strong corrosion resistance on acidic and alkaline solutions, has excellent chemical stability, and does not participate in any chemical reactions during the smelting process. The inner wall of the graphite crucible is smooth, and the melted metal liquid is not easy to leak and adhere to the inner wall of the crucible, so that the metal liquid has good fluidity and is suitable for various mold casting.
Request a quoteThe melting industry has always been in search of a crucible that can withstand high temperatures and provide durability. The introduction of the elliptical silicon carbide graphite crucible has revolutionized the melting industry. This crucible has been designed to meet the needs of the industry and is a perfect fit for melting cast iron.

Usage of elliptical crucible
The elliptical crucible is made of silicon carbide graphite, which is a combination of silicon carbide and graphite. This material is known for its high thermal conductivity and excellent thermal shock resistance. The crucible has an elliptical shape, which provides a larger surface area for the molten metal to spread out. This feature helps in reducing the thermal stress on the crucible and increases its durability.
The elliptical crucible is designed to withstand high temperatures, making it perfect for melting cast iron. Cast iron has a melting point of around 1150°C, and the elliptical crucible can withstand temperatures up to 1800°C. This makes it an ideal choice for the melting industry. It is also designed to prevent the formation of slag. Slag is a byproduct of the melting process and can cause problems in the casting process. The elliptical shape of the crucible allows for better control of the melting process, resulting in a cleaner melt and fewer impurities.
The use of the elliptical silicon carbide graphite crucible has many advantages over traditional crucibles. It has a longer lifespan, requires less maintenance, and provides a cleaner melt. This results in a higher quality casting and a more efficient melting process.
The common question in graphite crucible
1. How to clean slag
During the smelting process, additives and impurities in the molten metal form slag, which adheres to the walls of the crucible. Since the slag contains additives that will corrode the crucible wall, the slag should be removed once a day. Clean the bottom and all around one by one.
(1) Special tools should be used to remove slag when the slag has not solidified.
(2) Avoid scratching the crucible wall when removing slag.
(3) When the multi-layer slag solidifies and remains on the crucible wall, it will corrode the crucible and affect the thermal conductivity.
It can also cause the crucible to crack when heated and expand, thereby shortening the service life of the crucible.
Hence, the introduction of the elliptical silicon carbide graphite crucible has revolutionized the melting industry. Its unique design and material make it a perfect fit for melting cast iron. The crucible has many advantages over traditional crucibles and is a must-have for any melting industry. Its durability, high-temperature resistance, and ability to prevent slag formation make it an ideal choice for the melting industry.