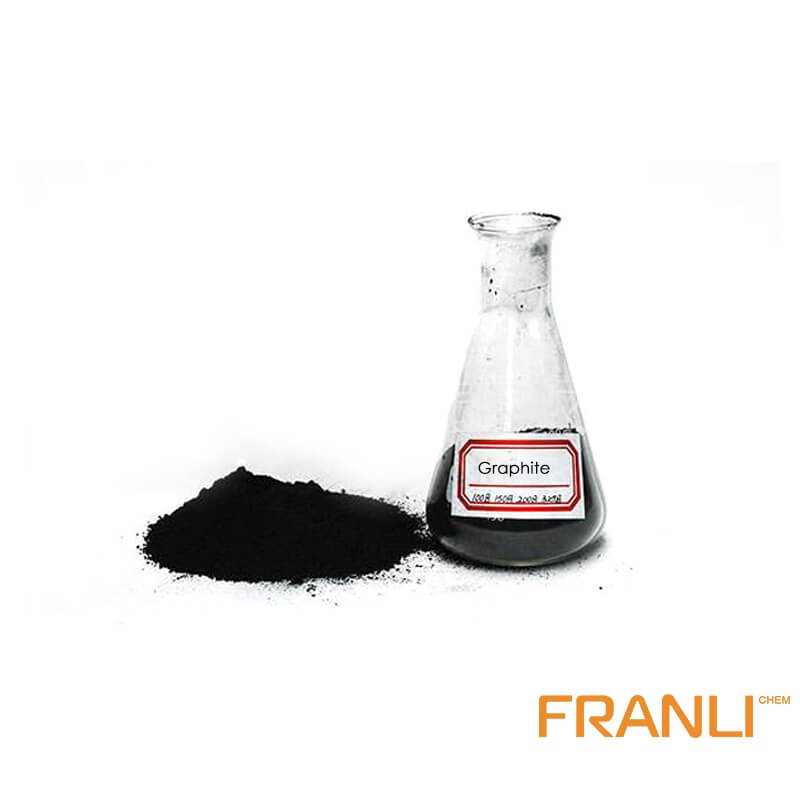
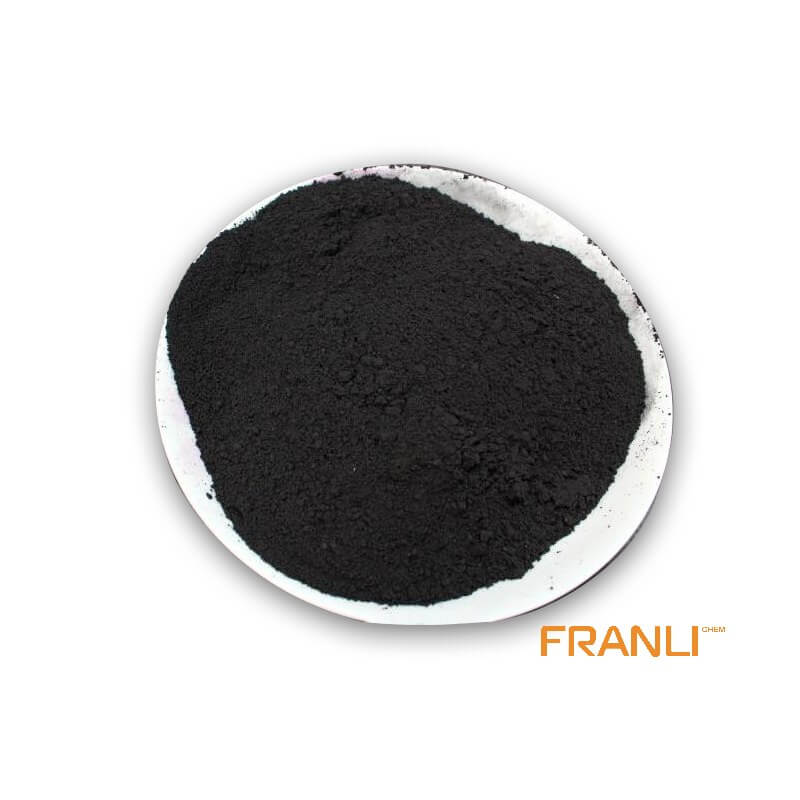
Graphite Powder
Size
1≥60%, etc
Package
25kg small bags into ton bags or ton bags
Features
High temperature resistance, conductivity and thermal conductivity, etc.
Application
As refractory material, conductive material and wear-resistant lubricating material, etc.
Graphite powder is a widely used industrial material, which is obtained from high-purity graphite after crushing, grinding, and screening. The classification of graphite powder is mainly based on the particle size, ranging from 50 mesh to 30000 mesh. The larger the mesh, the finer the particle size, and the higher the price.
Request a quoteGraphite is a kind of carbon material that has been widely used in many fields of the national economy. It is an allotrope of carbon with carbon black, diamond, carbon 60, carbon nanotubes, graphene, and so on. In brief, graphite has the characteristics of temperature resistance, electrical conductivity, thermal conductivity, lubricity, chemical inertia, plasticity, and so on. Graphite is commonly used in the manufacture of refractory materials, conductive materials, wear-resistant materials, lubricating materials, high-temperature sealing materials, corrosion-resistant materials, thermal insulation materials, adsorption materials, friction materials, and anti-radiation materials.

Examples of some new technological progress of graphite powder in the field of heat conduction and heat dissipation materials:
FRANLI discloses a high thermal conductivity magnetic shielding and high strength waterproof potting adhesive made of graphite powder, which has high thermal conductivity, good waterproof performance, and high tensile strength, and has a good application prospect.
Features of graphite lubricants
The raw material formula of the high thermal conductivity magnetic shielding high strength waterproof potting adhesive described in the graphite includes one or more of the following raw materials by weight: 25-35 parts of alumina, 5-15 parts of silicon carbide, and 5-35 parts of aluminum nitride; One or more of flaky nickel powder 1-8 parts, hydroxyl iron powder 3-15 parts, ferrosilicon aluminum 2-40 parts and ferronickel powder 10-38 parts; One or more of 5-40 parts of graphene, 1-9 parts of graphite powder and 3-18 parts of graphite rubber powder; 2-7 parts of epoxy resin and 1-9 parts of polyurethane.
The high thermal conductivity magnetic shielding high-strength waterproof potting adhesive prepared by the invention is used for electronic potting and has high strength, waterproof, good thermal conductivity effect, good insulation, and magnetic shielding effect, and the preparation process of the high thermal conductivity magnetic shielding high-strength waterproof potting adhesive is simple, the production energy consumption is low, and no “three wastes” are produced.
FRANLI also discloses a method for producing a thermally conductive film using synthetic graphite powder. Compared with the existing natural graphite film or metal film, the thermally conductive film has excellent thermal conductivity and lower production costs.
The existing production process of thermal conductive graphite film is to calcine expensive polymer film such as polyimide film at 2000 ℃ – 3000 ℃. The cost of raw materials and equipment is relatively high, and it is difficult to produce large-width (such as 1000mm) roll products.

The manufacturing method of the heat-conducting film comprises the following steps:
① Pretreating and synthesizing graphite powder under pressure or pressure reduction conditions;
② intercalation agent is added to the pretreated synthetic graphite powder;
③ The synthetic graphite powder with intercalation agent was heat-treated;
④ Rolled synthetic graphite powder after heat treatment.
The discloses a preparation method for high thermal conductivity carbon composite. Due to their excellent high-temperature mechanical properties and good ablation resistance, C / C composites have been successfully used in the preparation of the throat liner, gas rudder, and other key components of the solid rocket motor.
Firstly, the graphite is placed on the ultrasonic cleaning machine, and the 2.5% KOH solution is poured into the ultrasonic cleaning machine, and the graphite is cleaned by ultrasonic. After cleaning, the graphite is put into the hot air box for drying, and the graphite is cut by the cutting machine to make it uniform in size.
After cutting, the graphite is put into the pulverizer for preliminary crushing, and the crushed graphite particles are put into the vibrating screen so that the graphite particles with uniform size can be obtained. At the same time, because the graphite is of uniform size, it is convenient to crush the graphite, and then the crushed graphite particles are placed on the grinder, Finally, the graphite particles are put into the oscillation box to vibrate the graphite, making the graphite present a fluffy state.
By cleaning, cutting, crushing, and grinding the graphite, the graphite can be uniformly crushed, so that the obtained graphite can form powder particles with uniform size. Therefore, when the graphite is pressed later, there will be no voids and no quality problems.
FRANLI discloses a high thermal conductivity silicone grease and its preparation process. The utility model relates to the technical field of heat-conducting interface materials for high-power electronic and electrical equipment. The thermal conductive silicone grease is composed of the following components: powder 60-90 parts; Silicone oil 10-0 phr; 1-5 phr of coupling agent; The powder is a mixture of alumina, zinc oxide, and graphite powder, wherein the powder is composed of the following components by weight: alumina: 20-35 parts; Zinc oxide: 10-15 phr; Graphite powder: 60-70 phr. The particle sizes of alumina, graphite, and zinc oxide are 10-40 μ m, 1-30 μ m, and 1-5 μ m respectively.
The graphite powder further reduces the thermal resistance of the thermally conductive silicone grease and speeds up the heat absorption of the thermally conductive silicone grease to the heat source by matching a variety of powders with different particle sizes. Alumina and zinc oxide combined with graphite powder can form a kind of modified coated graphite powder. The modified coated graphite powder has a good interface with silicone oil, which is the main component of thermal conductive silicone grease. It is conducive to its dispersion in the thermally conductive silicone grease and can improve the compatibility and affinity of the two, reducing the contact thermal resistance between the two interfaces and improving the thermal conductivity. As one of the additives, the thermal conductivity of graphite powder is 150-300w / (m · K). The addition of graphite powder improves the thermal conductivity of the product. Low cost, suitable for industrial production and use.