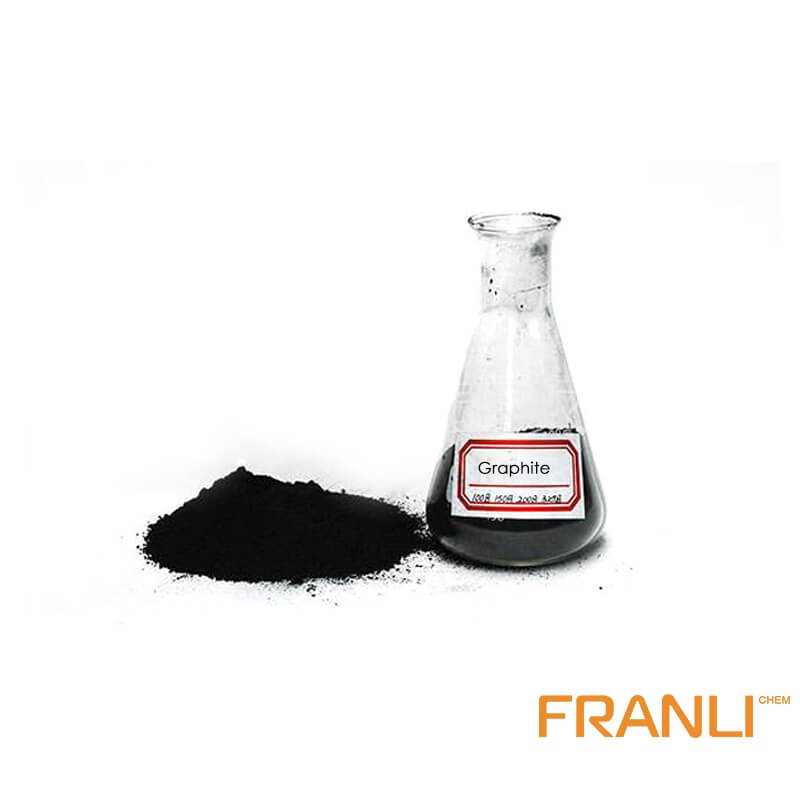
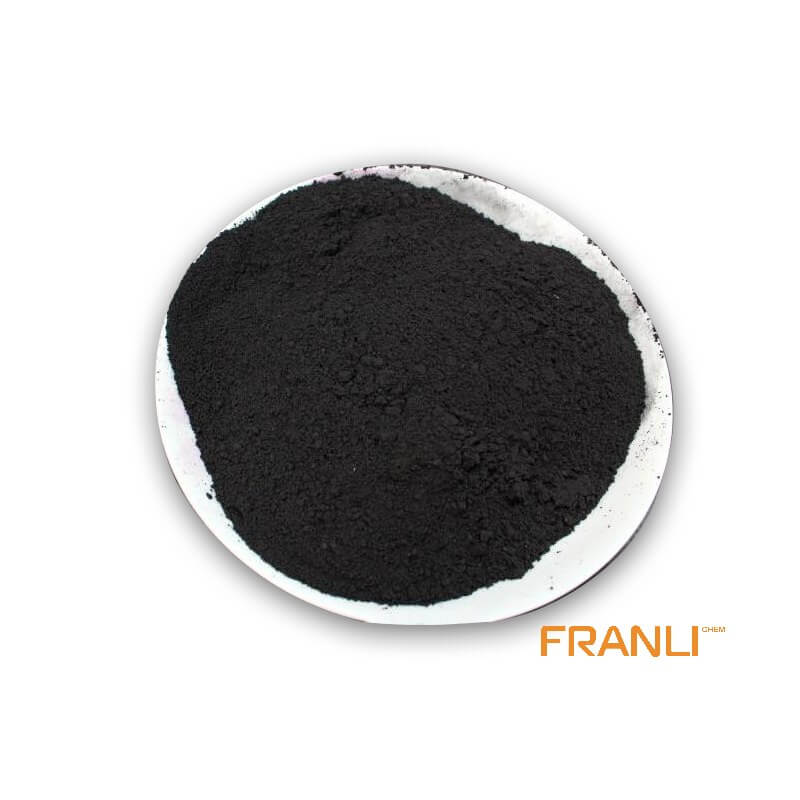
Graphite Powder
Size
1≥60%, etc
Package
25kg small bags into ton bags or ton bags
Features
High temperature resistance, conductivity and thermal conductivity, etc.
Application
As refractory material, conductive material and wear-resistant lubricating material, etc.
Graphite powder is a widely used industrial material, which is obtained from high-purity graphite after crushing, grinding, and screening. The classification of graphite powder is mainly based on the particle size, ranging from 50 mesh to 30000 mesh. The larger the mesh, the finer the particle size, and the higher the price.
Request a quote
Graphite powder has many functions, such as casting. What is the role of graphite powder in casting? Let’s take a look.
Casting can be divided into precision casting and ordinary casting. According to the surface requirements of the castings, non-ferrous metals such as copper, iron, aluminum, tin, lead, etc. are generally cast. Casting refers to the molding method of smelting metal, manufacturing mold, pouring molten metal into the mold, and obtaining metal parts with a certain shape, size, and performance after solidification. Casting is the process of melting the metal into a liquid that meets certain requirements and pouring it into the mold. After cooling, solidification, and cleaning, the casting with a predetermined shape, size, and performance can be obtained. Casting blank is almost formed, which can achieve the purpose of free machining or a small amount of processing, reduce the cost and reduce the production time to a certain extent. Casting is one of the basic processes in the modern plant manufacturing industry.

Casting is a kind of metal hot working technology mastered by human beings earlier, which has a history of about 6000 years. China has entered the heyday of bronze casting from 1700 BC to 1000 BC, and the technology has reached a fairly high level. Casting is a kind of processing method that melts the solid metal into liquid and pours it into the mold of a specific shape, waiting for it to solidify. The metals to be cast are copper, iron, aluminum, tin, lead, etc. the materials of common mold are raw sand, clay, water glass, resin, and other auxiliary materials. The mold of special casting includes investment casting, lost foam casting, metal mold casting, ceramic mold casting, etc( Raw sand includes quartz sand, magnesia, zircon sand, chromite sand, forsterite sand, kyanite sand, graphite sand, iron sand, etc.)
The graphite powder coated on the surface of the solid can form a smooth film with firm adhesion, which is the good coating performance of graphite. It is a good casting film remover. The graphite powder commonly used in casting includes crystalline graphite powder (flake graphite powder) or cryptocrystalline graphite powder (earthy graphite powder, also known as microcrystalline graphite powder and black lead powder). So far, there are many small factories in villages and towns that produce thin-walled small pieces by hand. Instead of adding pulverized coal in the molding sand, they use a soft brush to brush earth like graphite powder on the surface of the wet sand mold, and the casting surface is quite smooth.

Although graphite powder does not form bright carbon when pouring molten iron, the wetting angle of graphite to molten iron is much greater than 90 °, That is, the sand mold is not wetted by molten iron. Moreover, the pores on the surface are blocked by the earth rock toner, and the molten iron is not easy to penetrate and drill into the sand particles, which can prevent the casting from sticking sand and improve the surface smoothness of the casting. Graphite powder has a good lubrication effect, which can improve the compactness and fluidity of molding sand, decrease the air permeability, reduce the ejection resistance of samples, and improve the mold performance of molding sand.