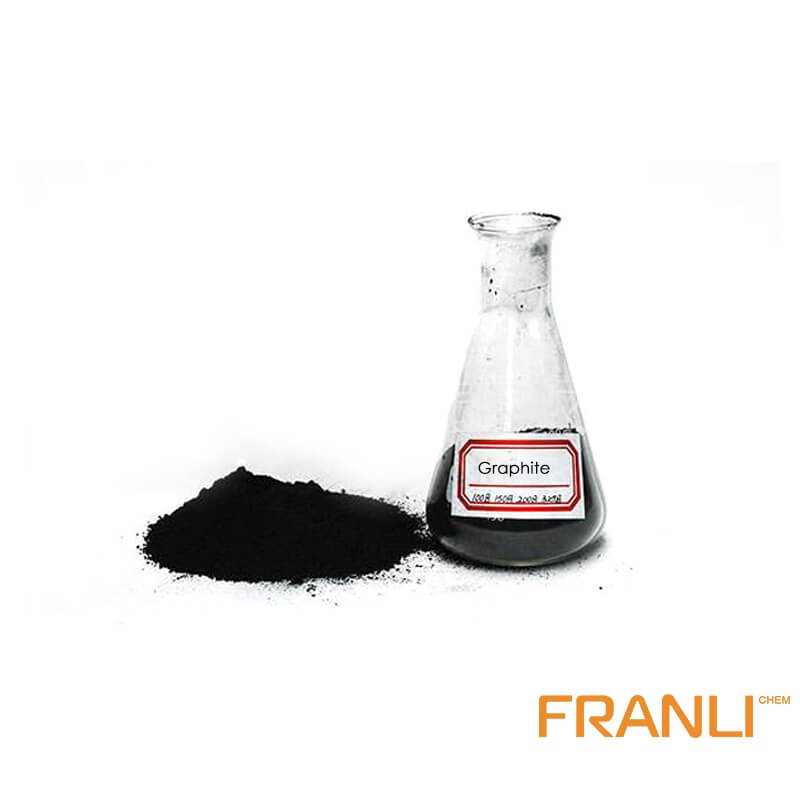
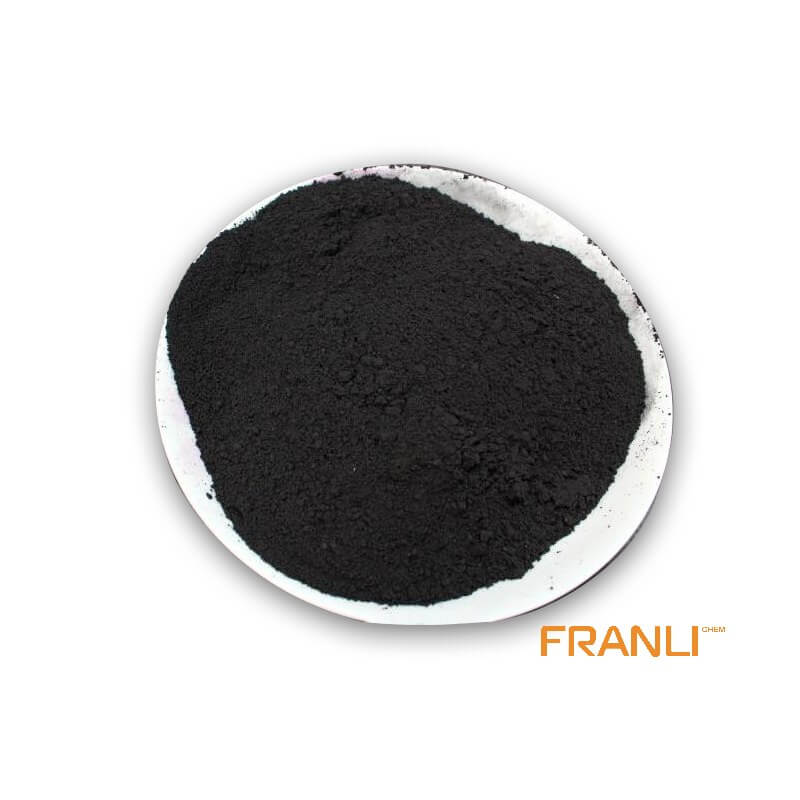
Graphite Powder
Size
1≥60%, etc
Package
25kg small bags into ton bags or ton bags
Features
High temperature resistance, conductivity and thermal conductivity, etc.
Application
As refractory material, conductive material and wear-resistant lubricating material, etc.
Graphite powder is a widely used industrial material, which is obtained from high-purity graphite after crushing, grinding, and screening. The classification of graphite powder is mainly based on the particle size, ranging from 50 mesh to 30000 mesh. The larger the mesh, the finer the particle size, and the higher the price.
Request a quote
High-purity graphite powder is a kind of natural flake graphite powder. High purity graphite powder has high carbon content and good purity. Here, high purity also means that the carbon content of high-purity graphite powder is as high as 99.99%. High purity graphite powder has the following characteristics.

First, the high-temperature resistance of high-purity graphite powder is about 2300 degrees. Even if it is burned by ultra-high temperature arc, the weight loss is very small and the coefficient of thermal expansion is very small. The strength of graphite increases with the increase of temperature. At 2000 ℃, the strength of graphite doubles.
Second, the lubricity of high-purity graphite powder. The lubricity of high-purity graphite powder depends on the size of the graphite scale. The larger the scale, the smaller the friction coefficient, the better the lubricity.
Third, the conductivity and thermal conductivity of high-purity graphite powder and graphite is 100 times higher than that of general non-metallic minerals. Thermal conductivity exceeds that of steel, iron, lead, and other metal materials. The thermal conductivity of high-purity graphite powder decreases with the increase of temperature. Even at extremely high temperatures, high-purity graphite powder becomes an insulator.
Fourth, the plasticity of high-purity graphite powder is good, and the toughness of high-purity graphite powder is good, which can be ground into very thin sheets.
Fifth, the chemical stability of high-purity graphite powder. High purity graphite powder has good chemical stability at room temperature and can resist acid, alkali, and organic solvent corrosion.
Sixth, the thermal shock resistance of high-purity graphite powder. When used at room temperature, high-purity graphite powder can withstand the drastic change of temperature without damage. When the temperature changes suddenly, the graphite volume changes little and will not produce cracks.

These are the six characteristics of high purity graphite powder, and there are many ways to purify high-purity graphite powder, each with its advantages and disadvantages. Now let’s talk about it.
The flotation method is one of the conventional purification methods with the least energy and reagent consumption and the lowest cost, which is the biggest advantage of graphite purification by the flotation method. For flake graphite, multi-stage grinding is not only unable to completely dissociate the monomer, but also not conducive to the protection of large flake graphite. Therefore, it is neither economical nor scientific to further improve graphite grade by flotation. To obtain high carbon graphite with more than 99% carbon content, it is necessary to purify graphite by chemical method.
(1) Alkali acid purification method. The carbon content of graphite purified by the alkali acid method can reach more than 99%, which has the characteristics of less one-time investment, higher product grade, and strong process adaptability. Besides, it also has the advantages of conventionality and versatility
Alkali acid method is the most widely used method in China; Its disadvantages are large energy consumption, long reaction time, a large amount of graphite loss, and serious wastewater pollution.
(2) Hydrofluoric acid method. The main advantages of the hydrofluoric acid process are high impurity removal efficiency, high-grade products, little influence on the performance of graphite products, and low energy consumption. The disadvantage is that hydrofluoric acid is highly toxic and corrosive. Strict safety protection measures must be taken in the production process. Strict requirements for equipment also lead to higher costs. In addition, the wastewater produced by the hydrofluoric acid process is highly toxic and corrosive, which can only be discharged after strict treatment. Environmental protection investment also greatly reduces the advantages of the low cost of the hydrofluoric acid process.
(3) Chlorination roasting method. The low roasting temperature and low chlorine consumption of the chlorination roasting method make the production cost of graphite decrease greatly. Meanwhile, the carbon content of graphite products is equivalent to that of graphite treated by the hydrofluoric acid method, and the recovery rate of the chlorination roasting method is higher. However, due to the toxic and corrosive nature of chlorine gas, high requirements for equipment operation, strict sealing, and proper treatment of tail gas, its popularization and application are limited to a certain extent.
(4) The biggest advantage of the high-temperature method is that the carbon content of the product is very high, which can reach more than 99.995%. The disadvantage is that the high-temperature furnace must be specially designed and built, the equipment is expensive, the one-time investment is large, in addition, the energy consumption is large, and the high electricity cost increases the production cost. Moreover, the application scope of this method is extremely limited due to the harsh production conditions. Only when there are special requirements for the purity of graphite products, such as national defense and aerospace, can we consider using this method for small batch production of graphite, and it can not be popularized in industry. Comparative analysis shows that several methods of graphite purification have their advantages and disadvantages. Alkali acid process is easy to operate, has low production cost, and has low requirements for production conditions, but the fixed carbon content of graphite is low, which can not reach 99.9% at present. The hydrofluoric acid method has a good impurity removal effect and high fixed carbon content, but hydrofluoric acid is highly toxic and corrosive, which requires strict safety protection measures and production conditions, and the wastewater is not easy to treat. Because chlorine gas is poisonous and corrosive, the chlorination roasting method also needs to be strictly sealed. The high-temperature method can produce very high-grade high-purity graphite, but because of its limitations, it can not be popularized at present and is only applied in a small range.