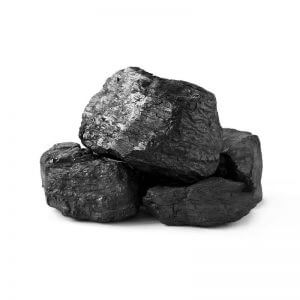
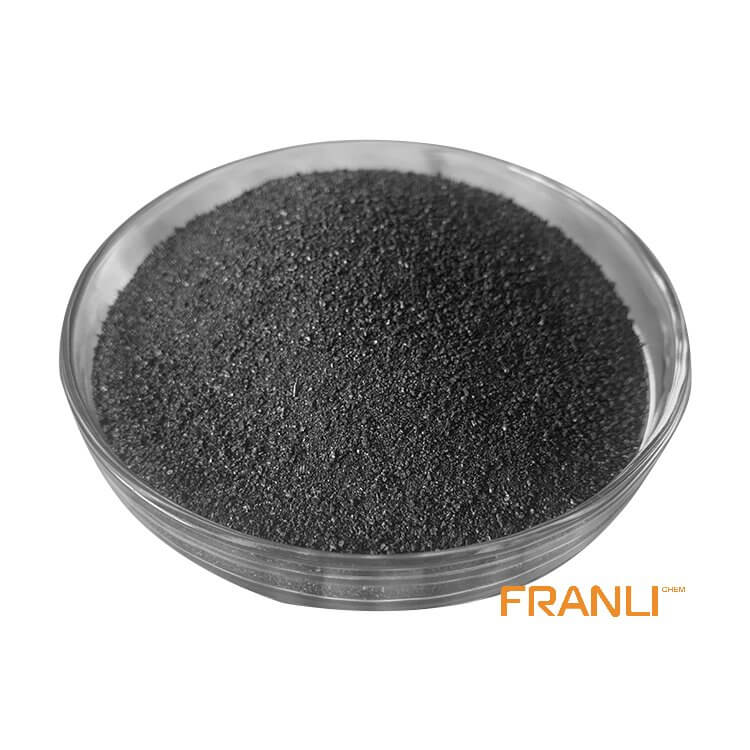
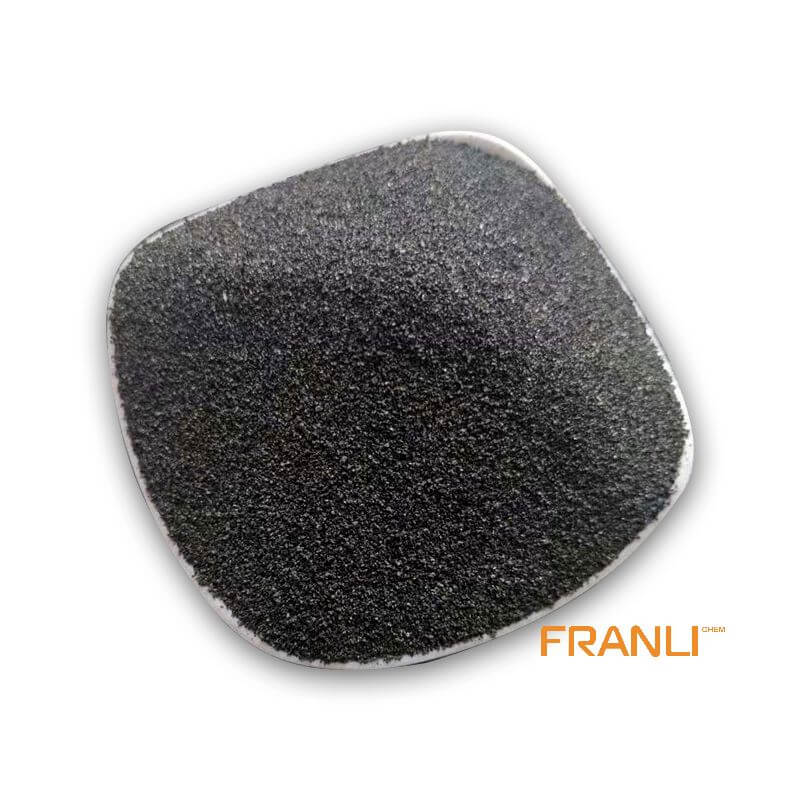
Petroleum Coke
Size
According to your requirements
Package
25 kg small bags into ton bags or ton bags
Features
Low ash content and low boiler ash discharge, etc.
Application
Depending on its quality, petroleum coke can be used in industries such as graphite, smelting and chemical industry, etc
Petroleum coke, as a byproduct of petroleum, is produced in the process of petroleum processing, that is, the crude oil is distilled to separate light and heavy oil, and the heavy oil is converted into petroleum coke by hot cracking. If petroleum coke can be obtained directly from petroleum processing, then the petroleum coke is raw coke or ordinary coke. Petroleum coke has irregular shape, dark gray or black, porous structure and metallic luster.
Request a quoteAt this stage, the domestic calcined petroleum coke rotary kiln is based on the technology of the Japanese rotary kiln to digest and introduce, so as to complete the corresponding production design, but compared with the Japanese calcined petroleum coke production capacity, China’s calcined petroleum coke production capacity is relatively low.

The production capacity of the rotary kiln currently used in the production of a company is about 6.5 t per hour, and if it is compared with some other running rotary kilns in the domestic counterpart, the difference in the petroleum coke calcination process and environmental protection governance and energy-saving utilization is still relatively obvious.
Calcination process of petroleum coke
At this stage, the vast majority of rotary kilns rely on the volatile combustion released by them to complete the calcination of petroleum coke, and in order to achieve the temperature required for calcined petroleum coke. Therefore, in this case, the temperature in the kiln can be divided into the following areas, namely: preheating area, calcination area and cooling area. In normal production, the combustion of volatiles is the main source of energy for petroleum coke calcination, and in this process, there can be no supplementary or small amount of external fuel, and production will not be affected.
Treatment of exhaust gas from petroleum coke calcination
As far as the current situation of domestic petroleum coke calcination is concerned, most of the petroleum coke calcination in the process of production, a small number of volatiles can not be fully burned, in addition, in the relevant treatment, these insufficiently burned volatiles will be discharged from the combustion chamber together with the exhaust gas. At this stage, gravity settlement chamber and combustion chamber are the methods used in most rotary kilns in China to treat exhaust gas.

Cooling cylinder cooling flue gas treatment
In the domestic cooling cylinder, the flue gas produced by cooling petroleum coke is first through the cyclone dust collector, and then through the cloth bag or water film dust collector to collect dust to complete the dust collection treatment, and the dust collection treatment is directly discharged into the atmosphere after the dust collection treatment is completed. This method has the following problems: (1) The replacement cost of the bag dust collector is higher, which increases the production and operation cost; (2) When the cloth bag dust collector is vibrating, the negative pressure control of the rotary kiln head will be seriously disturbed and affected by calcination; (3) It is impossible to effectively treat harmful gases such as sulfur dioxide in the flue gas.
Petroleum coke calcination after cooling
The domestic rotary kiln usually adopts the cooling method of combining internal and external, and the high-temperature petroleum coke is cooled accordingly in the cooling cylinder. In the actual production process, because this method requires external cooling, the structure of the cooling cylinder becomes complicated, increasing the cost of manufacturing and maintenance. Some factories use the internal cooling method of segmented direct water injection to avoid problems.
Petroleum coke calcination after cooling
The domestic rotary kiln usually adopts the cooling method of combining internal and external, and the high-temperature petroleum coke is cooled accordingly in the cooling cylinder. In the actual production process, because this method requires external cooling, the structure of the cooling cylinder becomes complicated, increasing the cost of manufacturing and maintenance. Some factories use the internal cooling method of segmented direct water injection to avoid problems.
This is an effective method of calcining petroleum coke at the Franli plant to deal with harmful gases produced during the calcination of petroleum coke at high temperatures. Franli Co., Ltd. can also provide better petroleum coke products, interested parties can consult.