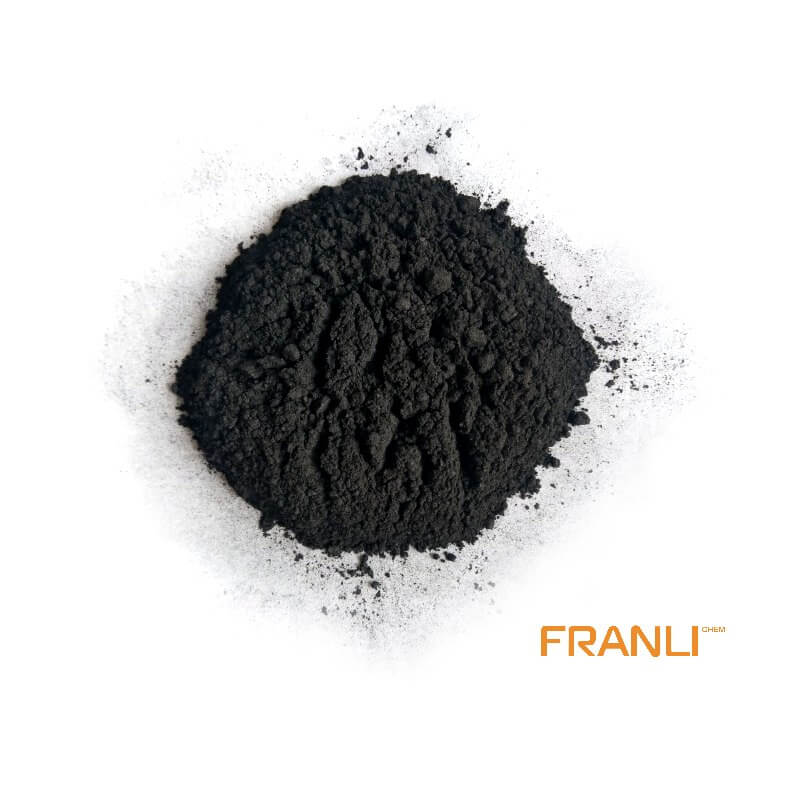
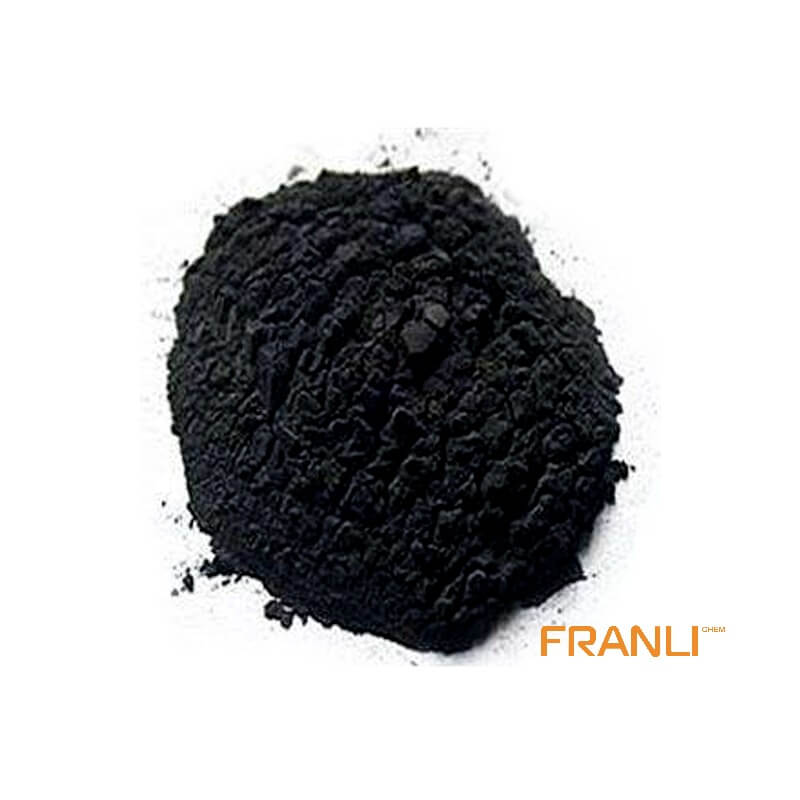
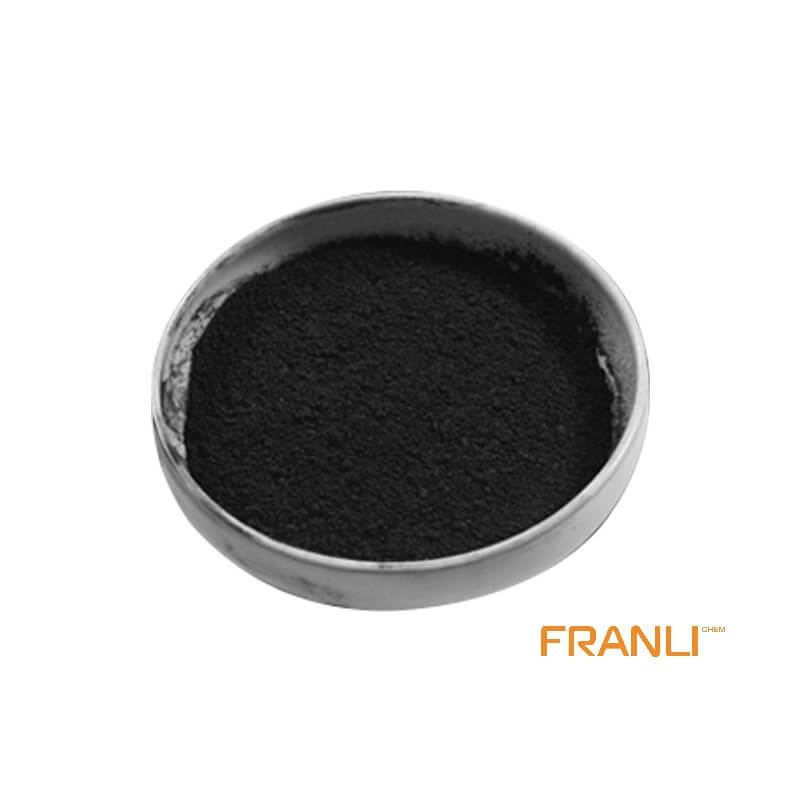
Purity Graphite
Size
According to your requirements
Package
25 kg small bags into ton bags or ton bags
Features
good temperature resistance, self lubrication, conductivity, etc.
Application
Can be used in machinery, metallurgy, chemical industry, military industry, etc.
High purity graphite is also called molded graphite, which means that the carbon content of graphite is more than 99.99%, which has good electrical conductivity, high temperature resistance, oxidation resistance, low resistance coefficient, corrosion resistance, high purity, self lubrication, thermal shock resistance, isotropy, easy to be machined and so on.
Request a quoteGraphite is an allotrope of carbon, and each carbon atom is surrounded by three other carbon atoms, which are covalently bonded to form a covalent molecule. Graphite is an electrical conductor because each carbon atom emits an electron and those electrons are free to move. Graphite has the characteristics of self-lubrication, chemical stability, high temperature resistance, electrical conductivity, thermal conductivity, plasticity, etc., and its application fields are very wide. At present, the application of high-purity graphite is divided into two categories: powder and product etc.

Application of high-purity graphite
1. Battery anode material
The negative electrode material of the power battery is mainly composed of carbon materials, including natural graphite, artificial graphite, and graphitized intermediate carbon microspheres.
In the world, graphite anode materials account for 90% of the total shipments, and they are in the absolute mainstream of anode materials. Driven by end-market demands such as tablet PCs, ultrabooks, electric bicycles, new energy vehicles, and energy storage, the output of lithium batteries will maintain steady growth. As one of the four key materials of lithium batteries, anode materials determine the performance of lithium batteries, such as charge and discharge efficiency, cycle life and so on. To prepare high-performance battery negative electrode materials, the purity of raw materials will be one of the most critical indicators. The purity of graphite will directly affect its internal resistance, charge and discharge speed, etc. Generally, the purity of graphite raw materials for battery negative electrodes should not be lower than 99.99% %. Isostatic graphite refers to a molding method of graphite, which is the most important means of preparing high-performance graphite products. According to different application directions of graphite products, the requirements for the purity of graphite products are different.
2. Solar cells and semiconductor wafers
In the solar energy and semiconductor industries, a large number of high-performance isostatic graphite is used to make graphite components in the thermal field of single crystal Czochralski furnaces, heaters for polysilicon melting and casting furnaces, heaters for compound semiconductor manufacturing, crucibles and other components. In recent years, solar photovoltaic power generation has developed rapidly, and the production of monocrystalline silicon and polycrystalline silicon in the photovoltaic industry has a huge demand for graphite. At present, both monocrystalline and polycrystalline silicon products are developing towards large-scale and high-end products, and there are higher requirements for isostatic graphite, namely: higher purity, higher strength, larger specifications, and graphite materials for high-performance crucibles. The purity of graphite is required to reach more than 99.95%.
3. Electrode graphite
In EDM, most of the traditional high-purity copper is used as the electrode material. Nowadays, graphite is gradually replacing copper as electrode raw material, which has great potential. The main reasons are as follows:

(1) Graphite has no melting point, is a good conductor of electricity, has good thermal shock resistance, and is an excellent electrode material for EDM.
(2) Faster processing speed: Normally, the machining speed of graphite can be 2~5 times faster than that of copper; and the speed of electric discharge machining is 2~3 times faster than copper.
(3) The material is less prone to deformation: it has obvious advantages in the processing of thin rib electrodes; the softening point of copper is about 1000 degrees, and it is easy to deform due to heat; the sublimation temperature of graphite is 3650 degrees; the thermal expansion coefficient is only 1/ of that of copper 30.
(4)The discharge consumption is smaller; since the spark oil also contains C atoms, during the discharge machining, the high temperature causes the C atoms in the spark oil to be decomposed, and a protective film is formed on the surface of the graphite electrode, which compensates for the loss of the graphite electrode .
(5)There is no burr; after the copper electrode is processed, it needs to be manually trimmed to remove the burr, while the graphite has no burr after processing, which saves a lot of cost and is easier to realize automatic production. Graphite is easier to grind and polish; since the cutting resistance of graphite is only 1/5 of that of copper, it is easier to grind and polish manually.
It is this incomparable advantage that graphite has gradually replaced copper as the material of choice for EDM electrodes.
In today’s industrial production, graphite has become an essential key material, especially in the solar industry, semiconductor industry and nuclear industry, the demand for graphite is increasing sharply, and the quality requirements are getting higher and higher. The production of high-purity graphite raw materials is an important bottleneck for the development of our finished static pressure graphite and battery negative electrode materials. How to prepare various types of high-performance graphite raw materials that meet market and research needs at low cost and without pollution is what our factory has been pursuing the goal.