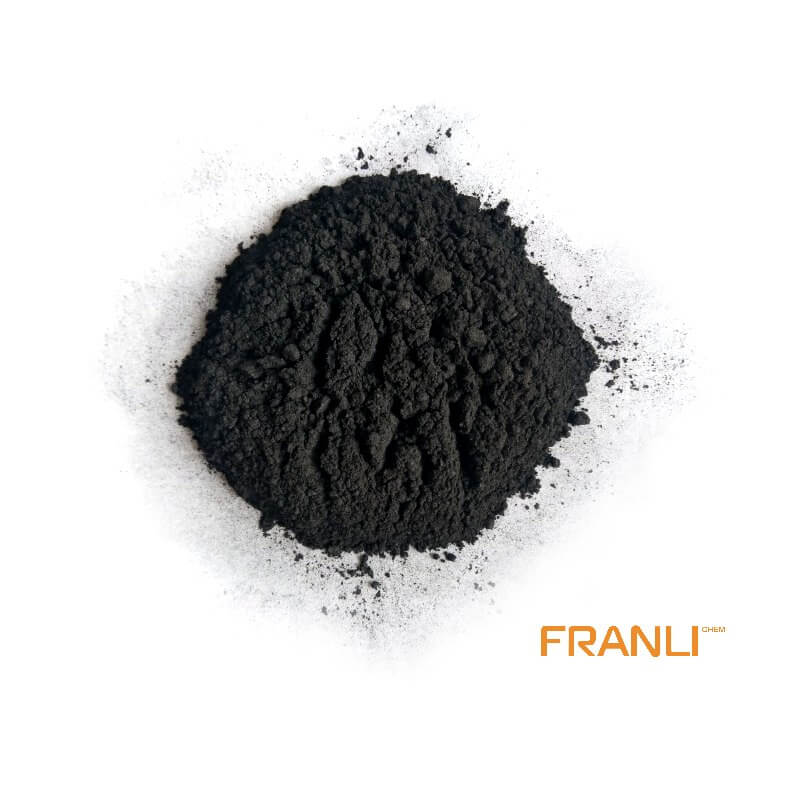
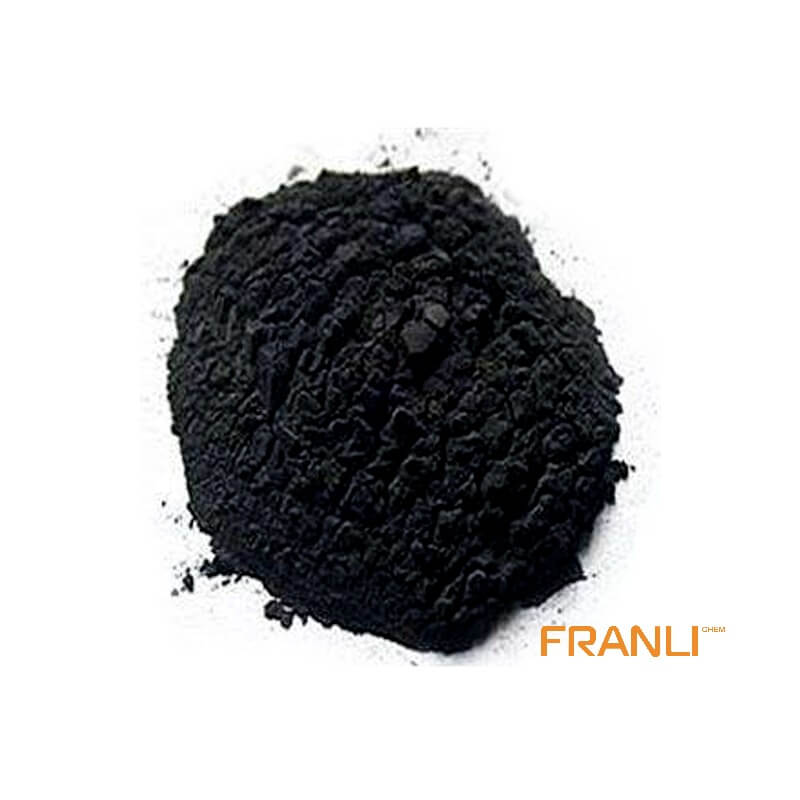
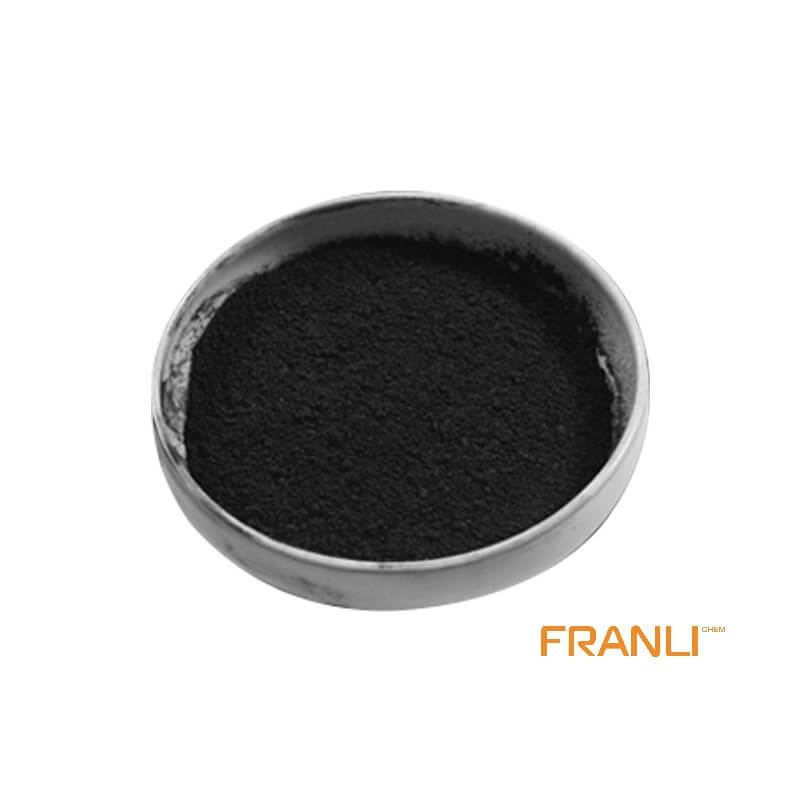
Purity Graphite
Size
According to your requirements
Package
25 kg small bags into ton bags or ton bags
Features
good temperature resistance, self lubrication, conductivity, etc.
Application
Can be used in machinery, metallurgy, chemical industry, military industry, etc.
High purity graphite is also called molded graphite, which means that the carbon content of graphite is more than 99.99%, which has good electrical conductivity, high temperature resistance, oxidation resistance, low resistance coefficient, corrosion resistance, high purity, self lubrication, thermal shock resistance, isotropy, easy to be machined and so on.
Request a quote
High-purity graphite refers to the carbon content is greater than 99.9% of graphite, with high strength, high density, high purity, high chemical stability, high density and uniform structure, high-temperature resistance, high conductivity, good wear resistance, self-lubrication, easy processing, and other characteristics, widely used in metallurgy, chemical industry, aerospace, electronics, machinery, nuclear energy, and other industrial fields.
The alkali-acid method is the main method of chemical purification of graphite, and it is a relatively mature process at present. Through strong alkali and acid, insoluble impurities will be changed into soluble salts, in the process of repeated washing discharge, so as to achieve the purpose of purification and get high purity graphite.

The alkali purification method of the principle of graphite is the NaOH with graphite according to a certain proportion mixing calcination, in 500-700 ℃ high-temperature graphite impurity such as silicate, silicon aluminate, quartz, and other components react with sodium hydroxide, generate soluble sodium silicate or acid-soluble silica sodium aluminate, and then washed with water to remove in order to achieve the purpose of desilication and get high purity graphite
Another part of impurities such as metal oxides, after alkaline fusion remains in graphite, a product of desilication in acid leaching, made of metal oxide into soluble metal compounds, and the impurities such as graphite in the carbonate formation in the process of the alkali leaching and acid-soluble compounds into the liquid after reaction with acid, then by filtering, washing, and separation of graphite, then we can get high purity graphite.
Graphite has great chemical inertia and good stability. It is insoluble in organic and inorganic solvents and does not react with lye. In addition to nitric acid, concentrated sulfuric acid, and another strong oxidizing acid, it does not react with many acids; Does not react with water and steam below 6000℃. Therefore, high purity graphite properties remain unchanged during purification.
The production process of high purity graphite with an annual output of 30,000 tons takes graphite concentrate with a carbon content of 96.8% as raw material, and chemical purification of graphite is carried out by alkali fusion and acid leaching (sulfuric acid)

(1) Alkali fusion
The graphite raw material package is placed above the feeding port by mechanical lifting, and the dust at the feeding port is collected by the air collecting hood and treated by the filter element dust collector. The graphite powder in the material package is conveyed into the graphite powder silo by pneumatic and is put into the mixing mixer through the metering tank. The recovered 30% lye is pumped into the mixer by a metering pump. After opening and stirring evenly, it is put into the rotary alkali furnace. After opening and heating the jacket of the alkali furnace, the melting temperature is 500-800℃, and the reaction is about 1h this is an important step towards obtaining high purity graphite
Alkali furnace is closed equipment, indirect heating, the heat source for the gas from the gas producer through the burner combustion produced by high-temperature flue gas. At the high temperature of 500-800℃ impurities in graphite such as silicate, aluminate, quartz, and other components and sodium hydroxide chemical reaction, the formation of soluble sodium silicate or acid-soluble sodium aluminate, part of iron, calcium, magnesium, and other converted into hydroxide is still in solid form in high purity graphite.
Including alkali furnace flue gas in the gas combustion gas and alkaline fusion volatilization in the process of water vapor and a small amount of alkaline gas, alkali furnace for indirect heating, a heat source for high-temperature flue gas from the burning of coal gas bubbled into an external heating jacket, alkali furnace heating and alkali furnace flue gas after waste collected by after discharge line together, each stage alkali furnace flue gas leads to alone, Centralized into the desulphurization tower for desulphurization treatment, and finally discharged through an exhaust cylinder. The desulphurization tower adopts the double alkali method.
After alkaline fusion reaction, open the discharge valve, the material through the screw conveyor to sink in a row, add pure water agitation leaching, an alkaline fusion of reactants soluble sodium silicate or acid-soluble silica in the sodium aluminate soluble in water, after vacuum suction filter, leaching liquid alkali recovery pool, into the filter cake and water washing to remove excess alkali, after 3-4 clean, filtered again after getting the desilication of graphite. The alkali leaching solution is discharged into the alkali recovery tank to recover caustic soda, and the washing alkali wastewater is collected and processed in the wastewater treatment station.

Alkali leaching liquid contains a large amount of sodium hydroxide, sodium carbonate into the alkali recycle pool, such as alkali pump into the causticizing, add lime causticizing treatment, steam indirect heating reaction to about 95 ℃ for 30 minutes, recovery of sodium hydroxide solution, add some sodium carbonate recycled get 30% of the lye, alkali furnace for raw materials, precipitation by causticizing objects bottom slag discharge. The alkali recovery rate is about 60%.
The pollutants produced in the alkali melting process mainly include alkali furnace feeding dust, alkali washing wastewater, gas combustion waste gas, and so on. The feed dust of the alkali furnace is collected by the air collecting hood and purified by the filter core type dust collector. A sodium silicate or acid-soluble sodium silicoaluminate and excess alkali are discharged into the wastewater treatment station for treatment. The sulfur dioxide produced by heating gas combustion in an alkali furnace is desulphurized by a double alkali process.
(2) Sulfuric acid leaching
After desilication, the product is leaching with acid to convert the metal oxides into soluble metal compounds, and the impurities in graphite such as carbonate and acid-soluble compounds formed in the alkaline leaching process react with acid into the liquid phase, and then through filtration and washing to achieve separation with graphite.
The acid used for acidification of high purity graphite in this project is the acid recovered from the expandable graphite workshop. After desilication, the graphite is sent into the pickling tank, and the acid recovered from the expandable graphite workshop is put into the pickling tank, and stirred to react for 2h at room temperature. Metal oxides are converted into soluble metal compounds, and impurities such as carbonate in graphite and acid-soluble compounds formed in the alkali leaching process react with acid and enter the liquid phase. After the reaction, vacuum filtration is performed, and the leachate is discharged into the wastewater treatment station. The filter cake is washed with water to be neutral, and the acid-washing wastewater is discharged into the wastewater treatment station for treatment. Filter cake discharged into the dryer.

(3) Drying
After purification, the high purity graphite filter cake is sent to the dryer, which is heated indirectly by steam. The drying operation is divided into two stages to ensure that the moisture of the product is 0.5%.In the first stage, the water content is reduced from 30% to 7-8%.In the second stage of the selection of stable and reliable, dust-free energy-saving stainless steel disc dryer, material, and hot medium do not directly contact, to ensure the purity of graphite.
The dryer is closed equipment, the high purity graphite dust in the drying process is captured by the filter element type dust collector, the exhaust gas after purification, the dried graphite is screened for slag removal, and further remove the large proportion of salt impurities in the graphite products and the powder whose particle size does not meet the requirements, etc., qualified products are packed into storage.