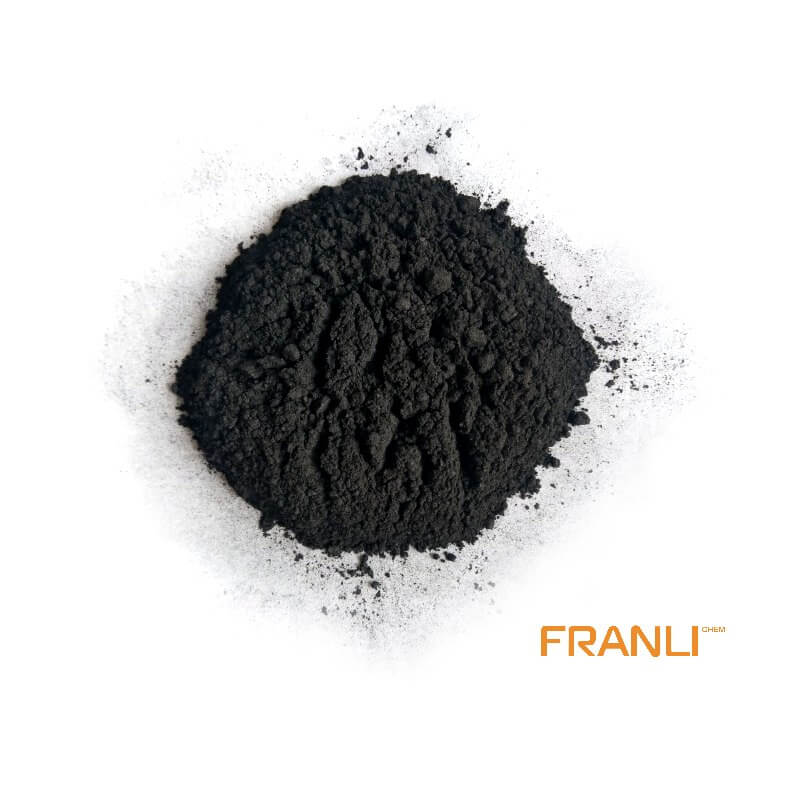
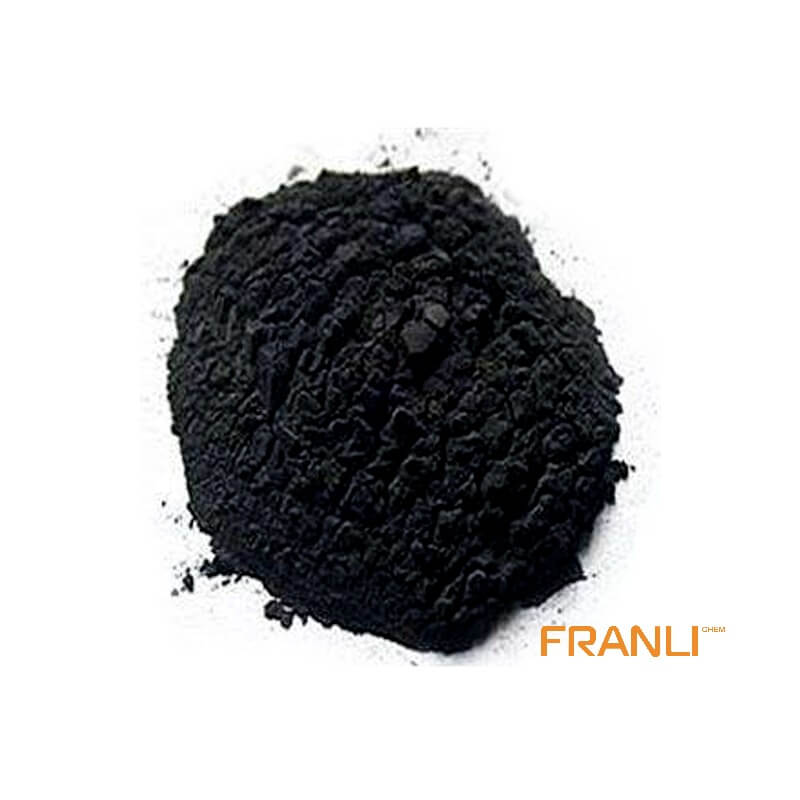
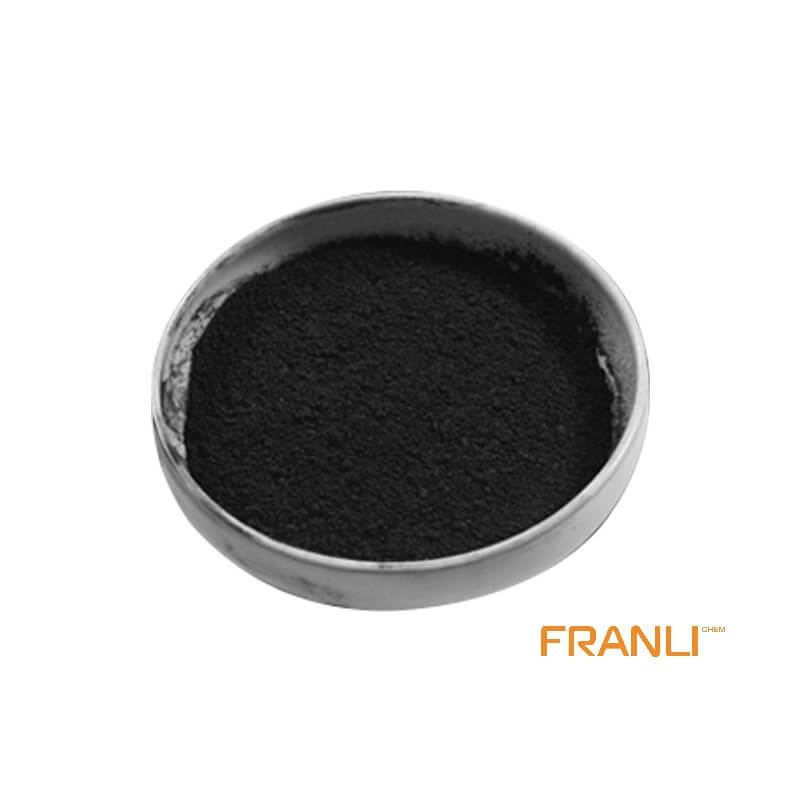
Purity Graphite
Size
According to your requirements
Package
25 kg small bags into ton bags or ton bags
Features
good temperature resistance, self lubrication, conductivity, etc.
Application
Can be used in machinery, metallurgy, chemical industry, military industry, etc.
High purity graphite is also called molded graphite, which means that the carbon content of graphite is more than 99.99%, which has good electrical conductivity, high temperature resistance, oxidation resistance, low resistance coefficient, corrosion resistance, high purity, self lubrication, thermal shock resistance, isotropy, easy to be machined and so on.
Request a quoteHigh-purity graphite is used more and more in daily life because of its characteristics.
Graphite has high-temperature resistance, good conductive and thermal conductivity, good lubricity, plasticity, thermal shock resistance, and chemical stability. Therefore, graphite materials are more and more widely used in atomic energy, automobile, aerospace technology, metallurgy, chemical industry, machinery, and other industries, and become an indispensable non-metallic material in modern industrial technology. As an industrial raw material, graphite materials play an important role in some special industries and high-tech fields, such as atomic energy, automobile industry, aerospace technology, etc., the graphite used in these industries must be high-purity graphite with a carbon content of over 99.9%. The purity of graphite products can not meet the requirements of the high-purity graphite industry. Therefore, the development and production of high-purity graphite materials have become one of the problems that need to be solved in the development of graphite materials to a wider and deeper field.

Since the 1990s, people have developed wet purification methods (flotation method, acid-base method, etc.) based on the characteristics of chemical properties of graphite, high melting point, and boiling point, and the noninteraction with various strong acids, bases, strong oxidants, and reducers, organic and inorganic solvents under general conditions The purity and quality of graphite products were improved by hydrofluoric acid method and fire purification (chlorination roasting method, high-temperature method. This paper mainly introduces the principle and method of graphite purification, summarizes the research progress and achievements of graphite purification in recent years. Meanwhile, the advantages and disadvantages of various high purity graphite production methods are compared and analyzed, which aims to provide a reference for the researchers and producers of graphite purification.
1. Principle and method of graphite purification
According to the physicochemical principle of the process of graphite purification, the purification methods of graphite are divided into two categories: 1. Wet purification, including flotation, acid-base, and hydrofluoric acid; 2、 The purification method by fire method mainly includes chlorination roasting method and high-temperature method.
1.1 Wet purification
1.1.1 Flotation method
Flotation is to enrich and purify graphite by using floatability of graphite, which is mainly suitable for natural flake graphite with good floatability.
The final concentrate grade of graphite after flotation is usually about 90%, sometimes 94-95%. Because some silicate minerals and potassium, sodium, calcium, magnesium, aluminum, and other compounds are very fine-grained immersed in graphite flakes, even fine grinding is not easy to cleavage monomer, so it is difficult to remove this part of impurities by physical beneficiation method. Therefore, the flotation method is mainly used for the initial purification of graphite, and the purity after purification is not high. If the grade of graphite is to be improved, chemical or thermal methods shall be adopted to further remove impurities in graphite. Yuechenglin confirmed this point. In the experimental study of the rapid flotation process of flake graphite, he concluded that the rapid flotation process can make the raw ore with a grade of 4.35%, and obtain the graphite concentrate with grade 91.89 and recovery rate of 92.52%. Compared with the common flotation method, the grade of graphite concentrate in the rapid flotation process is increased by 1.15%, the recovery rate is increased by 4.28%, and the yield of large graphite is also improved significantly.
1.1.2 Acid-base method
The acid-base method is also known as the alkali acid method, also known as the molten alkali method or the sodium hydroxide method. Impurities in graphite such as
SiO 2, Al 2O 3, Fe 2O 3, MgO, and Cao react with NaOH at high temperatures. Some impurities (SiO 2) form water-soluble products and are removed by washing with water. The other impurities do not react or form water-insoluble hydroxides, which are then soaked in hydrochloric acid to convert into soluble chlorides and are removed by washing with water. Therefore, the purification method of graphite is divided into the alkali melting process and the acid hydrolysis process. The alkali melting process is to mix a certain amount of graphite, sodium hydroxide, and water evenly put them into the reactor and heat them to melt. After reaction for a period of time, it was cooled to below 100 ℃ and filtered until the pH value of the washing solution was 7 ~ 8. The reaction principle is as follows
SiO 2 +2NaOH NaSiO 3 +H 2 O
M + +OH – M(OH) n
Under the pressure of autoclave, a low concentration alkali solution can be used to replace molten NaOH or KOH to remove silicon. If liquid ammonia is used to treat graphite raw material, the content of Na + and Cl – in graphite can be reduced to less than 80ppm.
The acidolysis process is to mix the alkali-soluble (fused) graphite with a certain concentration of hydrochloric acid solution for hot leaching, react at a certain temperature for a period of time, then wash with filtered water until neutral, dry, and purified. The reaction principle of acidolysis is as follows
Fe 2 O 3 +6HCl 2FeCl 3 +3H 2 O
M (OH) n + HCl mcln + H 2O (where n = 2 or 3)
High purity graphite can be obtained after acid hydrolysis. Tang Xingming, a scientific research institute of Pangang refractory company, used the acid-base method to purify 90% of flake graphite produced by Panzhihua Jinjiang graphite ore and obtained more than 99.5%, the highest purity
99.79% of high purity graphite. Li Changqing of Beijing University of chemical technology used a similar method (adding boric acid or sodium metaborate as a cosolvent in the alkali melting process, and using a certain concentration of hydrofluoric acid in the acid hydrolysis process) to purify flake graphite with medium carbon graphite. The results showed that when the reaction temperature was 600 ℃ and the reaction time was 60min, the ratio of sodium hydroxide solution to graphite was 1 ∶ 0.6, The purity of graphite can reach 99.6% when the concentration of NaOH is 35% and the amount of HCl is 50% of the mass of graphite. X.j.lu of Shandong University purified graphite with 87-88% carbon to 99.4% by acid-base method and reduced sulfur content from 0.6% to 0.05%.

Hydrofluoric acid method
The hydrofluoric acid purification method is to use hydrofluoric acid to react with almost all impurities in graphite to produce water-soluble compounds and volatiles, and then wash with water to remove impurities, so as to achieve the purpose of purification. That is to say, the graphite is soaked in a certain concentration of hydrofluoric acid, filtered to neutral, dried, and purified to obtain high-purity graphite. The reaction principle is as follows
Na 2 O+2HF 2NaF+H 2 O
K 2 O+2HF 2KF+H 2 O
SiO 2 +6HF H 2 SiF 6 +2H 2 O
Al 2 O 3 +6HF 2AlF 3 +3H 2 O
At the same time, hydrofluoric acid reacts with Cao, MgO, and Fe2O3 to form precipitates
CaO+2HF CaF 2 +H 2 O
MgO+2HF MgF 2 +H 2 O
Fe 2 O 3 +6HF 2FeF 3 +3H 2 O
The covering of precipitates CaF 2, MgF 2, and FEF 3 hindered the further reaction
CaF 2 +H 2 SiF 6 CaSiF 6 +2HF
MgF 2 + H 2 SiF 6 MgSiF 6 +2HF
2FeF 3 +3H 2 SiF 6 Fe 2 (SiF 6 ) 3 +6HF
It can be seen from the above that the solubility of insoluble fluoride increases greatly in the presence of hydrochloric acid or dilute nitric acid. Hydrofluoric acid and mixed acid can dissolve almost all minerals under normal temperature and pressure, which is an ideal chemical deashing agent for removing minerals. Mo Haibo [3] made the mixed acid solution (hydrofluoric acid, hydrochloric acid, nitric acid, sulfuric acid solution, and water) react with the impurities in graphite by steam heating. The impurities in graphite were removed by washing, stirring, drying, and other processes. The fixed carbon content of purified graphite can reach 99.99% to 99.995%. Qingdao graphite Co., Ltd. adopts the mixed acid system of hydrofluoric acid, hydrochloric acid, and sulfuric acid to establish the first domestic automatic production line of high purity graphite with an annual output of 500 tons, creating a precedent for large-scale production of high purity graphite in China.
The hydrofluoric acid method has been widely used in graphite manufacturers at home and abroad, and the research on the Purification of graphite by the hydrofluoric acid method is also very active. Zheng Dongming et al. obtained high purity graphite by hydrofluoric acid purification method, with a purity of 99.95%. Zhang ramping used sulfuric acid hydrofluoric acid step-by-step purification method to purify 97% high carbon graphite to a high purity level of 99.94% carbon content. In addition, Zhang qingcen ] and others studied the process route of producing high-purity microcrystalline graphite and the behavior of silicon element in each process by hydrofluoric acid method combined with high-temperature alkali roasting method, and the purity of graphite can reach 99.56%.

1.2 Fire purification
1.2.1 Chlorination roasting method
The chlorination roasting method is to roast graphite in a certain high temperature and specific atmosphere, and then pass chlorine gas for chemical reaction, so that impurities in graphite can be chlorinated, and chloride and complex (with low melting boiling point) in the gas phase or condensate can escape, so as to achieve the purpose of purification. The reaction principle is as follows
2MO+2Cl 2 2MCl 2 + O 2
In order to improve the conversion of impurities, it is necessary to add reducing agent C. the reaction is as follows:
MO+Cl 2 +C 2MCl 2 + CO
Li Jiye used the chlorination roasting method to increase the carbon content of graphite from 86.09% to 98.76% and proved that the chlorination roasting method has the characteristics of high recovery and low cost. The patent in a closed graphitization furnace, one or more of inert gas, chlorine, Freon, or tetrafluoromethane are used for graphitization purification, and high purity graphite with ash content less than 50ppm is obtained.
1.2.2 High-temperature method
The high-temperature purification method is developed on the basis of high-temperature graphitization technology.
One of the important properties of graphite is its high melting point and boiling point. Graphite is one of the substances with the highest melting point in nature, and its melting point and boiling point are much higher than those of impurities. Therefore, it is theoretically believed that as long as the graphite raw material is heated above 2700 ℃, the impurities with a low boiling point can be removed by gasification first. After holding for a certain time, the impurities can be removed by heating, This is the theory of high-temperature purification of graphite.
Literature has studied the significant influence factors of graphite purification by high-temperature method, mainly including the following points: 1. Impurity content of graphite raw material. The higher the impurities in raw materials, the higher the quality content of the product. The purity of raw materials purified by the high-temperature method is generally more than 99%. 2、 The quality of the graphite crucible is also discussed. The ash content of graphite is higher than that of graphite crucible, which is conducive to the gasification and escape of ash in graphite. Otherwise, the ash content of graphite crucible material will diffuse through the crucible to the graphite material with a lower concentration to be purified, resulting in poor purification effect of graphite; 3、 Temperature rise curve of graphitization process. The graphitization temperature increases rapidly with high current heating, which is beneficial to the gasification and escape of ash in dispersed graphite. 4、 Particle size of raw material. Generally speaking, the smaller the particle size, the better the purification effect.
Zhang Xiangjun et al. purified graphite by the high-temperature graphitization method so that the carbon content of graphite reached more than 99.99%.
In addition to the wet and pyro purification methods, the researchers used pyro and wet methods (pyro wet purification method) to purify graphite. The results show that the improved pyro wet purification method can purify cryptocrystalline graphite with 84.18% fixed carbon content to 99.25% fixed carbon content.
Comparison of advantages and disadvantages of graphite purification methods
2.1 Flotation
Flotation is a common method. It is the one with the least energy consumption and reagent consumption and the lowest cost in the conventional mineral purification scheme, which is the biggest advantage of graphite purification by flotation. However, when using this method to purify graphite, the grade of graphite can only be limited, and it is very difficult to further improve the grade, and the recovery rate of graphite is very low, so its application scope is limited. In order to obtain high carbon graphite with about 99% carbon content, it is necessary to purify graphite by chemical method.
2.2 Acid-base method
The acid-base method is the most widely used method in high-purity graphite manufacturers in China. In addition to the characteristics of less one-time investment, high product grade, and strong adaptability, it also has the advantages of easy realization and strong versatility. Its disadvantages lie in high-temperature sintering, melting, large energy consumption, long reaction time, and serious equipment corrosion, The loss of graphite is large and the pollution of wastewater is serious.
2.3 Hydrofluoric acid method
The main advantages of the hydrofluoric acid process are high impurity removal efficiency, high product grade, little influence on the performance of graphite products, and low energy consumption. The disadvantage is that hydrofluoric acid is highly toxic and corrosive. Strict safety protection measures must be taken in the production process. Strict requirements for equipment also lead to higher costs. There are problems such as overflow of fine flake graphite and a lower recovery rate. In addition, the wastewater produced by the hydrofluoric acid process is highly toxic and corrosive, which needs to be treated strictly before being discharged. The investment in environmental protection greatly increases the cost of the hydrofluoric acid process.
2.4 Chlorination roasting method
The advantage of the chlorination roasting method is that the low roasting temperature and chlorine consumption make the production cost of graphite higher, and the high purification efficiency (more than 98%) and the high recovery rate can be obtained by the chlorination roasting method. However, the tail gas from the chlorination roasting process is difficult to treat, seriously polluted, seriously corroded to equipment, and high cost of chlorine gas, which limits the popularization and application of this method.
2.5 High-temperature method
The biggest advantage of the high-temperature method is that the carbon content of the product is very high, which can reach more than 99.995%. The disadvantage is that the purity of raw materials is high, so the high-temperature furnace must be specially designed and built, the equipment is expensive, the investment is huge, and the electric heating technology is strict. In addition, the application scope of this method is extremely limited due to the high electricity cost. Only when there are special requirements for the purity of graphite products, such as national defense and aerospace, can we consider using this method for small batch production of graphite.
3 Conclusion
With the development of the atomic energy industry, nuclear industry, aerospace technology, the solar energy industry, and other high-tech industries, ordinary purity graphite products can no longer meet the needs of users, and the research and development and production of high purity graphite products have become the focus of research and attention. The current graphite purification methods have their own advantages and disadvantages. In order to obtain high-purity graphite products with low cost and high performance, it is necessary to comprehensively consider the properties of raw materials, process characteristics, equipment investment, production energy consumption, and environmental treatment.